通过管理芯片和周围空气之间的热传递,维持光耦特性,避免失效。
任何半导体设备的动作依靠其模型温度,这就是为什么电子参数要按照特定温度给出。为维持光耦特性,避免失效,通过管理芯片和周围空气之间的热传递限制温度。不应该超过设计规定的连接温度,即使光耦也许没有被归入“功率器件”的种类。这么做有以下两个原因:
首先,全面增加光耦长期可靠性,因为任何固态设备的工作温度都与其长期可靠性成反比。因此应该是器件工作在最低的实际工作温度下。其次,某些参数与设备的问题紧密相连,这些随温度而变得参数包括漏电流、触发电流、CTR、骤回电压和电阻。
进行热计算的三个主要方法是通过使用器件降额值、随温度变化功率图或温度模型。最简单的方法是使用热降额值(假定用功率/度)。然而,制造商非常保守的得到这个数字,所以这个方法不能提供最精确的结果。
随温度变化功率图与第一种方法非常相似,但是用简单的数字代替,依照随温度变化功率图(图1)。并且,这是一个非常保守的方法,应该非常顾及可靠的设计,但是它也不能提供最精确的结果。
进行热计算更全面的方法是使用热模型。一些光耦的热模型已经建立,用于大多数简单精确的计算。
英文原文:
Thermal characteristics of optocouplers
Sustain an optocoupler\'s performance and avoid failure by managing the heat transfer between the chip and the ambient atmosphere.
By Roshanak Aflatouni and Bob Gee, Vishay Intertechnology -- EDN, 10/18/2007
The behavior of any semiconductor device is dependent on the temperature of its die, which is why electrical parameters are given at a specified temperature. To sustain an optocoupler\'s performance and to avoid failure, the temperature is limited by managing the heat transfer between the chip and the ambient atmosphere. You should not exceed the device\'s rated junction temperature, even if an optocoupler may not fall into what you consider the "power device" category. This is true for two main reasons.
The first is to increase the overall long-term reliability of the optocouplers, as the operating temperature of any solid-state device is inversely proportional to its long-term viability. Consequently, you should operate a device at the lowest practical operating junction temperature. Secondly, certain parameters are closely tied to the operating temperature of the device; these temperature-dependent parameters include leakage current, trigger current, CTR, snapback voltage, and on-resistance.
The three main ways of performing thermal calculations are by using a component derating number, or a graph of allowable power versus temperature, or a thermal model. The simplest approach is to use a thermal derating number (given in power/degrees). However, manufacturers are very conservative when deriving this number, so this approach does not provide you with the most accurate results.
A graph of allowable power versus temperature is very similar to the first approach, but instead of a simple number, you follow a graph of allowable power versus temperature (Figure 1). Again, this is a very conservative approach and should allow for a very reliable design, but it does not provide you with the most accurate results.
A more comprehensive method for performing thermal calculation is to use a thermal model. Thermal models have been created for some optocouplers containing multiple dice —including phototriacs — for the most simple and accurate calculations.
Multiple Dice Optocoupler Thermal Model
This article demonstrates a simplified resistive model. When used correctly, this model produces results that provide "engineering accuracy" for practical thermal calculations. Figure 2 provides the simplified electrical analogous model for any optocoupler.
θCA = Thermal resistance, case to ambient, external to the package.
θDC = Thermal resistance, detector to case
θEC = Thermal resistance, emitter to case
θDB = Thermal resistance, detector junction to board
θDE = Thermal resistance, detector to emitter die
θEB = Thermal resistance, emitter junction to board
θBA = Thermal resistance, board to ambient, external to the package
TJE = Emitter junction temperature
TJD = Detector junction temperature
TC = Case temperature (top center)
TA = Ambient temperature
TB = Board temperature
Thermal resistances and specified junction temperatures for a particular device are provided in select datasheets.
Thermal Energy Transfer
There are three mechanisms by which thermal energy (heat) is transported: conduction, radiation, and convection. Heat conduction is the transfer of heat from warm areas to cooler ones, and effectively occurs by diffusion. Heat radiation (as opposed to particle radiation) is the transfer of internal energy in the form of electromagnetic waves. Heat convection is the transfer of heat from a solid surface to a moving liquid or gas.
All three methods occur in optocouplers. However, for most products in most environments, the majority (~ 75 %)
of heat leaving the package exits through the lead frame and into the board. This occurs because θBA is a conductive phenomenon with a much lower thermal resistance than the convective and radiative phenomena associated with θCA (θCA is typically an order of magnitude larger than other thermal resistances). Because very little heat leaves through the top of the package (heat convection), junction-to-case temperatures (θDC and θEC) are negligible in most environments.
This phenomenon is shown graphically in Figures 3a-c by the package temperature profile and strong heat flux contours evident in the die, lead frame, and board via. Because very little heat leaves through the top of the package, the top case temperature is a poor indicator of junction temperature. This means that the majority of the heat is transferred to the board, and very little heat is transferred to the air via the case, which can be verified in the thermal network.
Therefore, θDC and θEC can be removed from the thermal model (Figure 2). In this situation, the critical package thermal resistances become θDE, θDB, and θEB. θBA is the thermal resistance from the board to the ambient, and is primarily driven by the geometry and composition of the board. The type of board design used defines this characteristic. Junction-to-case thermal resistances are removed based on the fact that very little heat is leaving through the top of the package (Figure 4).
Thermal to Electrical Analogy
[page] The thermal-resistance characteristic defines the steady-state temperature difference between two points at a given rate of heat-energy transfer (dissipation) between the points. The temperature difference in a thermal-resistance system in an analog to an electrical circuit, where thermal resistance is equivalent to electrical resistance, is equivalent to the voltage difference, and the rate of heat-energy transfer (dissipation) is equivalent to the current (Table 1).
In a thermal circuit, a constant current source represents power dissipation. This is because generated heat must flow (steady-state) from higher temperatures to lower temperatures, regardless of the resistance in its path.
Assuming that you know or can estimate the power dissipated from the detector and the emitter (LED) and the temperature of the board and ambient, you can calculate the node temperatures by solving the network equations. If you desire to use the complete thermal resistance model, a more complex set of network equations will need to be solved.
The network equations will provide you with an estimate of what the operating temperature(s) would be before the specific environment is known. As an example, Figure 5 illustrates the analogous electrical model for calculating the temperature at both detector and emitter junctions, given a set of thermal resistances at room temperature with 50 mW on the emitter (PE) and 500 mW on the detector (PD). In order to write an equation to calculate the node temperatures, we will need to assume some heat flow directions (Figure 5). Based on Figure 5, the following equations will calculate the node temperatures:
PDE + PDB + PEC = PE (1)
- PDE + PDB + PDC = PD (2)
TB - TJD + θDB x PDB = 0 (3)
TB - TJE + θEB x PEB = 0 (4)
TJE - TJD + θDE x PDE = 0 (5)
TB - θBA x (PEB + PDB) = TA (6)
TC - θCA x (PEC + PDC) = TA (7)
TC - TJD + θDC x PDC = 0 (8)
TC - TJE + θEC x PEC = 0 (9)
Where:
PDB = Power dissipation, detector junction to board
PDE = Power dissipation, detector to emitter
PEB = Power dissipation, emitter junction to board
PDC = Power dissipation, detector junction to Case
PEC = Power dissipation, emitter junction to Case
When the simplified thermal model is used, equations 7-9 do not play any role in the node temperature calculation, and equations 1 and 2 are simplified to equations 1\' and 2\'. Figure 6a shows a simplified thermal circuit model. Since θCA, θEC, and θDC are not included in the simplified thermal model, all equations that include these resistances (equations 7-9) can be excluded for node temperature calculation. When TA is known, the following equations will calculate the node temperatures:
PDE + PDB = PE (1\')
- PDE + PDB = PD (2\')
TB - TJD + θDB x PDB = 0 (3)
TB - TJE + θEB x PEB = 0 (4)
TJE - TJD + θDE x PDE = 0 (5)
TB - θBA x (PEB + PDB) = TA (6)
For a desired TB and/or when only TB is known, Figure 6a is further simplified (Figure 6b). When TB is given, θBA does not play any role in calculating the node temperature, and any equation(s) that includes θBA can be eliminated. Based on Figure 6, the following equations will calculate the node temperatures when only TB is known:
PDE + PDB = PE (1\')
- PDE + PDB = PD (2\')
TB - TJD + θDB x PDB = 0 (3)
TB - TJE + θEB x PEB = 0 (4)
TJE - TJD + θDE x PDE = 0 (5)
Example 1:
Based on our characterization, Table 2 shows the thermal resistances for a simplified 6-pin dip package optocoupler. As the θBA is dependent upon the material, number of layers, and thickness of the board used, the optocouplers in our analysis were mounted on 2- and 4-layer boards with a thickness of 4 mm. Obviously, the θBA for the two different boards are different (Table 2).
Using equations 1\'-2\' and 3-6, Table 2\'s thermal resistances, and assuming Figure 6a\'s emitter and detector power dissipations, Table 3 shows the node temperatures when TA is known.
Example 2:
You can use the complete thermal model to calculated node temperatures. However, the results would not vary drastically from thermal calculation based on the simplified model for most products and i n most environments. Hence, it is entirely up you to decide how accurate the results are needed for each individual deign. Table 4 provides all thermal resistances for 6-in dip package phototriac.
Using equations 1-9, Table 4\'s thermal resistances, and assuming Figure 5\'s emitter and detector power dissipations, Table 5 shows the node temperatures when TA is known.
Regardless of the package size and type, the thermal analysis will need to be performed to ensure a solid design. To aid this process, Vishay provides detailed thermal characteristics for newly released optocouplers and solid-state relays (SSRs) that have total power dissipation of 200 mW and higher. This thermal data supplied allows you to more accurately simulate heat distribution and thermal impedance for optocoupler and SSR devices and thus avoid the problems that can arise when thermal parameters are exceeded.
上一篇:电路设计基础知识(五)——继电器
下一篇:CMOS互补(推挽)放大器
推荐阅读最新更新时间:2023-10-18 16:45
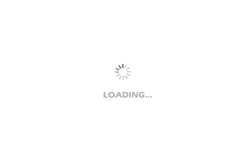
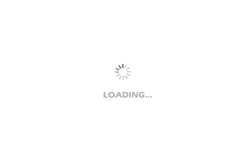
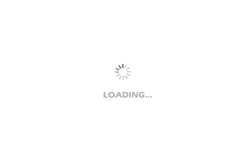
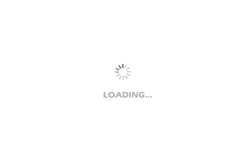
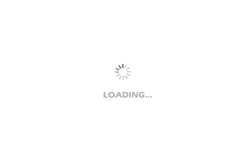
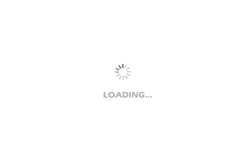
- 热门资源推荐
- 热门放大器推荐
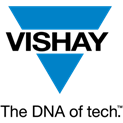
Vishay线上图书馆
- 选型-汽车级表面贴装和通孔超快整流器
- 你知道吗?DC-LINK电容在高湿条件下具有高度稳定性
- microBUCK和microBRICK直流/直流稳压器解决方案
- SOP-4小型封装光伏MOSFET驱动器VOMDA1271
- 使用薄膜、大功率、背接触式电阻的优势
- SQJQ140E车规级N沟道40V MOSFET

- Vishay推出适用于恶劣环境的紧凑型密封式SMD微调电阻器
- MathWorks 和 NXP 合作推出用于电池管理系统的 Model-Based Design Toolbox
- 意法半导体先进的电隔离栅极驱动器 STGAP3S为 IGBT 和 SiC MOSFET 提供灵活的保护功能
- 全新无隔膜固态锂电池技术问世:正负极距离小于0.000001米
- 东芝推出具有低导通电阻和高可靠性的适用于车载牵引逆变器的最新款1200 V SiC MOSFET
- 【“源”察秋毫系列】 下一代半导体氧化镓器件光电探测器应用与测试
- 采用自主设计封装,绝缘电阻显著提高!ROHM开发出更高电压xEV系统的SiC肖特基势垒二极管
- 艾迈斯欧司朗发布OSCONIQ® C 3030 LED:打造未来户外及体育场照明新标杆
- 氮化镓取代碳化硅?PI颠覆式1700V InnoMux2先来打个样
- Allegro MicroSystems 在 2024 年德国慕尼黑电子展上推出先进的磁性和电感式位置感测解决方案
- 左手车钥匙,右手活体检测雷达,UWB上车势在必行!
- 狂飙十年,国产CIS挤上牌桌
- 神盾短刀电池+雷神EM-i超级电混,吉利新能源甩出了两张“王炸”
- 浅谈功能安全之故障(fault),错误(error),失效(failure)
- 智能汽车2.0周期,这几大核心产业链迎来重大机会!
- 美日研发新型电池,宁德时代面临挑战?中国新能源电池产业如何应对?
- Rambus推出业界首款HBM 4控制器IP:背后有哪些技术细节?
- 村田推出高精度汽车用6轴惯性传感器
- 福特获得预充电报警专利 有助于节约成本和应对紧急情况