LED被称为第四代照明光源或绿色光源,具有节能、环保、寿命长、体积小等特点,可以广泛应用于各种指示、显示、装饰、背光源、普通照明和城市夜景等领域。近年来,世界上一些经济发达国家围绕LED的研制展开了激烈的技术竞赛。其中LED散热一直是一个亟待解决的问题!
有研究数据表明,假如LED芯片结温为25度时的发光为100%,那么结温上升至60度时,其发光量就只有90%;结温为100度时就下降到80%;140度就只有70%。可见改善散热,控制结温是十分重要的事。
除此以外LED的发热还会使得其光谱移动;色温升高;正向电流增大(恒压供电时);反向电流也增大;热应力增高;荧光粉环氧树脂老化加速等等种种问题,所以说,LED的散热是LED灯具的设计中最为重要的一个问题。
LED芯片结温是怎么产生的
LED发热的原因是因为所加入的电能并没有全部转化为光能,而是一部分转化成为热能。LED的光效目前只有100lm/W,其电光转换效率大约只有20~30%左右。也就是说大约70%的电能都变成了热能。
具体来说,LED结温的产生是由于两个因素所引起的。
1.内部量子效率不高,也就是在电子和空穴复合时,并不能100%都产生光子,通常称为由“电流泄漏”而使PN区载流子的复合率降低。泄漏电流乘以电压就是这部分的功率,也就是转化为热能,但这部分不占主要成分,因为现在内部光子效率已经接近90%。
2.内部产生的光子无法全部射出到芯片外部而最后转化为热量,这部分是主要的,因为目前这种称为外部量子效率只有30%左右,大部分都转化为热量了。
虽然白炽灯的光效很低,只有15lm/W左右,但是它几乎将所有的电能都转化为光能而辐射出去,因为大部分的辐射能是红外线,所以光效很低,但是却免除了散热的问题。
LED的散热现在越来越为人们所重视,这是因为LED的光衰或其寿命是直接和其结温有关,散热不好结温就高,寿命就短。大功率LED白光应用及LED芯片散热解决方法
当今LED白光产品被逐渐运用于各大领域投入使用,人们在感受其大功率LED白光带来的惊人快感同时也在担心其存在的种种实际问题!
首先从大功率LED白光本身性质来说。大功率LED仍旧存在着发光均一性不佳、封闭材料的寿命不长尤其是其LED芯片散热问题很难得到很好的解决,而无法发挥白光LED被期待的应用优点。
其次从大功率LED白光市场价格来说。当今大功率LED还是一种贵族式的白光产品,因为大功率产品的价格还是过高,而且技术上还是有待完善,所以说大功率白光LED产品不是谁想用就能够用的。下面分解下大功率LED散热的相关问题。
近些年在业界专家的努力下对大功率LED芯片散热问题提出了一下几点改善方案:
1.通过提高LED晶片面积来增加发光量。
2.采用封装数个小面积LED晶片。
3.改变LED封装材料和萤光材料。
那么是不是通过以上三种方法就可以完全改进大功率LED白光产品的散热问题了呢?实则斐然!首先我们虽然将LED芯片的面积增大,以此获得更多的光通量(光单位时间内通过单位面积的光束数即为光通量,单位ml)希望能够达到我们想要的白光效果,但因其实际面积过大,而导致在应用过程与结构上出现了一些适得其反的现象。 那么是不是大功率LED白光散热问题就真的无法解决了呢?当然不是无法解决了。针对单纯增大晶片面积而出现的负面问题,LED白光业者们就根据电极构造的改良及覆晶的构造并利用封装数个小面积LED晶片等方式从大功率LED晶片表面进行改良从而来达到60lm/W的高光通量低高散热的发光效率。
其实还有一种方法可以有效改进大功率LED芯片散热问题。那就是将其白光封装材料用硅树脂取代以往的塑料或者有机玻璃。更换封装材料不仅能够解决LED芯片散热问题更能够提高白光LED寿命,真是一箭双雕啊。我想说的是几乎所有像大功率LED白光这样的高功率白光LED产品都应该采用硅树脂作为封装的材料。为什么现在大功率LED中必须采用硅胶作为封装材料?因为硅胶对同样波长光线的吸收率不到1%。但是环氧树脂对400-459nm的光线吸收率高达45%,很容易由于长期吸收这种短波长光线以后产生的老化而使光衰严重。
当然在实际的生产生活中还会出现很多像大功率LED白光芯片散热这样的问题,因为人们对大功率LED白光越广泛的应用就会出现越深入难解的种种问题!LED芯片的特点是在极小的体积内产生极高的热量。而LED本身的热容量很小,所以必须以最快的速度把这些热量传导出去,否则就会产生很高的结温。为了尽可能地把热量引出到芯片外面,人们在LED的芯片结构上进行了很多改进。为了改善LED芯片本身的散热,其最主要的改进就是采用导热更好的衬底材料。像Cree公司的LED的热阻因为采用了碳化硅作基底,要比其他公司的热阻至少低一倍。
即使能够解决从晶片到封装材料间的抗热性,但因从封装到PCB板的散热效果不好的话,同样也是造成LED晶片温度的上升,出现发光效率下降的现象。所以,就像是松下就为了解决这样的问题,从2005年开始,便把包括圆形,线形,面型的白光LED,与PCB基板设计成一体,来克服可能因为出现在从封装到PCB板间散热中断的问题。
因此,在面对不断提高电流情况的同时,如何增加抗热能力,也是现阶段的急待被克服的问题,从各方面来看,除了材料本身的问题外,还包括从晶片到封装材料间的抗热性、导热结构、封装材料到PCB板间的抗热性、导热结构,及PCB板的散热结构等,这些都需要作整体性的考量。
LED照明灯具散热的问题解答
对目前常见的白炽灯泡或是荧光灯来说,即便产品本身运行可能产生热能,但组件的高热仍可以被有效隔离,使光源与电源接座不会因热而产生意外的问题。但固态照明就不同,一来LED组件集中单点的运行高温,必须采取更多积极手段进行散热处理,同时搭配主动有效的热处理机制,才能避免灯具发生问题。LED固态光源热处理问题较传统灯具复杂得多。
传统光源或灯具多有运行过程产生高热的问题,例如卤素灯泡或白炽灯泡,若是白炽灯形式,即在特殊处理的灯球内加热钨丝产生光亮。
实际上,高温产生在灯丝上而非灯座,即便灯座会因灯球玻璃或是金属受钨丝发光的辐射热、热传导间接产生高温,但产生的温度都在可接受的安全范围,再加上非直接接触传导,安全性也相对较高。
但换成LED固态光源形式的灯具,其热处理便可能成为新的应用安全问题。多数人会认为LED具高能源转换效率、低驱动能源优势,自然使用安全性较高,但实际上LED固态光源为了达到日常照明的应用目的,必须透过加大单组组件的功率去强化单元件的输出流明,例如灯具厂会采取多LED组件整合形式加强输出效果,且多组件同时运行也能改善LED固态光源光型偏向点光源的问题,让LED固态光源技术的灯具可产生如灯泡般的面光源效果。如果要强化单元件的输出流明,必须更高的电流,以使LED芯片的PN接面产生更多流明,但更高电流也会让单点LED组件的温度升高、更难处理,甚至为了提高灯具的光型表现、发光效率而采取多组件并用形式,也会使LED灯具的高温问题加剧,让散热问题更难处理。
综观目前LED灯具市场的发展趋势,多数LED光源的厂商大多会先以市场为主导,因为高单价、高利润,也可以借由技术差异迅速打入发展技术较前卫的LED光源市场,例如,针对室内装潢、情境灯具应用的嵌灯、壁灯、吸顶灯就成为LED光源灯具较常见的设计形式,其替换传统灯具后的省电效益亦最受相关业者关注。 LED光源灯具必须重点处理的热管理设计,在可能于密闭或半密死循使用的嵌灯、壁灯、吸顶灯产品,形成更严苛的挑战,灯具开发商必须从材料、产品构型、主/被动散热机制、驱动芯片设计等方面投入更多资源,以避免产品的问题肇生。特别是LED嵌入式灯具体积小,且常采多组件整合,模块的散热设计难度较高。嵌入式灯具外壳采铝挤型或散热片设计,可发挥自体散热作用。但这还远远不够。
LED热管理:NTC持续运行温度维持LED灯使用安全
若LED灯具没有搭配足够的热管理设计,在使用过程中可能会导致灯具因为经常性高热运行造成寿命锐减,产生必须频繁更换故障LED灯具的困扰,严重者甚至可能酿成意外,因运行高温造成线或是周边装潢着火燃烧!
在产品开发阶段,可运用智能型LED灯光控制技术,透过主动式的监看LED灯具与整体光源模块的温度表现,简化装置的热管理工作,同时当灯具与周遭温度上升至区段时,灯具必须降低电功率、减少LED亮度输出,以此提升LED固态光源灯具的使用安全性。
像LED吸顶灯外壳考虑较简单的设计形式,若灯具本身所使用的驱动器功能较聚焦于电源转换与LED组件驱动,并未内嵌温控微处理器与散热处理模块,为避免增加产品原料件的成本,LED灯具可整合NTC(Negative Temperature Coeffient)负温度系数Thermistor Sensors电,是成本效益相对较高的安全设计方案。
所谓NTC电,其设置目的是藉由透过电子回去监看LED的模块灯具温度,透过默认温度警示或是对应自动处理驱动状况,采关闭LED固态光源模块方式,来提升LED灯具的使用安全,同时NTC电也能降低设计的复杂度。由于NTC电的温度系数非常大,因此可以侦测得知微小的温度变化表现,被广泛应用于需量测、控制与补偿温度的相关电设计中,而NTC电在LED光源模块设计中,基本上为量测LED固态光源灯具的产品周边温度变化,至于量测状况会随着NTC改变的电压现况,直接测得电压和NTC电的温度对应关系。
当NTC和周边电或整个模块温度提升时,NTC电的电阻随即降低,产品可依此相依关系进行相关安全控制机制反馈,例如减少LED发光组件的驱动电流或是直接强制关闭灯具照明,在灯具温度问题改善后自动回复照明状态,藉此获得灯具使用的安全性。
监控LED灯具温度亦可导入微控制器采SMD形式制作的NTCTHERMISTOR组件
前述NTC电的改善形式,若想达到更佳的设计,搭配MCU进行更精密的安全设计也是一种相对务实的作法,在开发项目中,可将LED光源模块的状态区分为灯光是否正常、灯光是否被关闭,搭配温度警示与温度量测的程序逻辑判断,建构更为完善的智慧灯具管理机制。
例如,若出现灯具温度警示,经温度量测得知模块温度仍在可接受范围,可维持正常途径,透过散热片自然散逸运行温度;而当警示告知所测得温度已达需执行主动散热机制的基准,此时MCU必须控制散热风扇作动,甚至当温度达到值,系统必须透过MCU直接关闭驱动器供应电源,LED组件暂时停止运行,自然进行散热处理。
判断灯具是否使用或关闭,可用简单的判断位来做变化与了解产品目前使用状态,比较关键的是温度量测部分,所量测的温度必须实时与系统的参照表进行比对,以确认目前模块状态的正常或异常程度,计算出温度间距后,自动对应进行温控管理。
同样的,当温度进入区段时,控制机制应随即关闭灯源,同时在系统关闭后60秒或180秒后再次进行温度确认,待LED固态光源模块温度达正常值,再重新驱动LED光源,继续提供照明。总之:
大众一直关注灯具的使用寿命。若仅仅依靠使用低热阻的LED元件是不能为灯具装置构建良好的散热系统,而必须有效地减小从PN节点到周围环境的热阻,才能大大降低LED的PN节点温度,而成功实践延长LED灯具的使用寿命并提高实际光通量的目标。另外;有别于一般传统灯具,印刷电路板既是LED的供电载体,也是LED的散热载体,所以散热片和印刷电路板的散热设计十分重要。除此之外,灯具制造商还须考虑散热材料的质量、厚度和尺寸以及散热界面的处理和连接等因素。
上一篇:室内LED照明灯具日益趋向节能化智能化与人性化
下一篇:解密LED品质影响因素及最佳解决方案
推荐阅读最新更新时间:2023-10-12 22:32
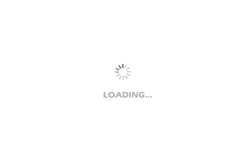
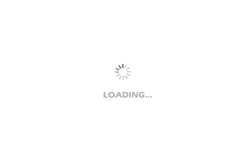
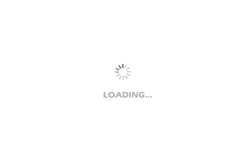
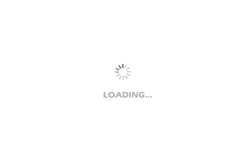
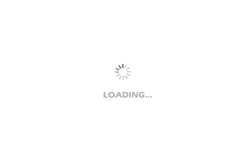
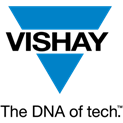
Vishay线上图书馆
- 选型-汽车级表面贴装和通孔超快整流器
- 你知道吗?DC-LINK电容在高湿条件下具有高度稳定性
- microBUCK和microBRICK直流/直流稳压器解决方案
- SOP-4小型封装光伏MOSFET驱动器VOMDA1271
- 使用薄膜、大功率、背接触式电阻的优势
- SQJQ140E车规级N沟道40V MOSFET

- 非常见问题解答第223期:如何在没有软启动方程的情况下测量和确定软启动时序?
- Vicor高性能电源模块助力低空航空电子设备和 EVTOL的发展
- Bourns 推出两款厚膜电阻系列,具备高功率耗散能力, 采用紧凑型 TO-220 和 DPAK 封装设计
- Bourns 全新高脉冲制动电阻系列问世,展现卓越能量消散能力
- Nexperia推出新款120 V/4 A半桥栅极驱动器,进一步提高工业和汽车应用的鲁棒性和效率
- 英飞凌推出高效率、高功率密度的新一代氮化镓功率分立器件
- Vishay 新款150 V MOSFET具备业界领先的功率损耗性能
- 强茂SGT MOSFET第一代系列:创新槽沟技术 车规级60 V N通道 突破车用电子的高效表现
- 面向车载应用的 DC/DC 电源