蓄电池技术是下一代汽车——电动汽车的核心技术之一。蓄电池是复杂的电化学系统,国内外对电池管理技术都进行了大量的研究,取得了许多成果。一般认为电池管理系统主要有如下功能:电池状态参数采集(包括温度、电压、电流等);电池荷电状态(State of charge,SOC)的准确估计;不健康电池的早期诊断;对电池组安全运行全面监控,如防止电池的过充电和过放电等等。
由于电动汽车蓄电池组通常是由几十个(上百个)单体电池组成,所以,每一个单体电池的工作状态正常与否不仅反映电池组性能的好坏,而且影响电池组的容量及剩余能量。实践表明,在电动汽车运行过程中,如不及时检测,找出老化电池给予调整,电池组的容量将变小,寿命将缩短,影响整个电池组的高效安全运行。
电池工作状态的检测由电池管理系统(Battery Management System,BMS)完成,而电池管理系统的其他功能(包括剩余能量的计算)都是建立在电池工作状态检测的基础之上的,研究蓄电池组工作状态检测方法对电动汽车的发展具有非常重要的意义。
l BMS的基本结构
湖南大学研发的电动汽车(EV一3号)采用的BMS结构示意图见图1。该BMS由电池监测系统、电池核电状态、(SOC)系统、数据显示系统3部分构成。传感器、电池监控系统和SOC系统构成底层系统,数据显示系统为上层系统,系统之间通过内部CAN总线通信。
2 蓄电池组工作状态检测方法
电动汽车蓄电池组一般都采用串联方式工作,工作电流与单体电池是一样的,检测比较容易,而端电压的检测则比较麻烦。若只检测电池组的端电压,方法很简单,只需在电池组的两端接上检测电路即可,但这样做是不行的,因为虽然可以得到总的工作电压,但无法判断具体单体电池的端电压,而只要有一块电池出问题就会影响整组电池的正常工作和性能;另外,对检测电路精度要求高。一个单体电池端电压的正常工作范围比较小,比如12V铅酸电池的终止电压在10V左右,电压变化范围在2~3V之间,检测电路只要10%的精度即可检测出1V的变化量。若24块12V铅酸电池串联,额定电压是288V,放电终止电压是240V,电压的正常变化范围是48V,如果一块电池的端电压降至9V,那么反映在总电压上为285V,只变化了大约1%。可见,检测电路的精度至少要达到1%以上才能检测出几伏电压的变化。而整组电池检测很难发现单体电池的缓慢变化,包括单体电池本身的老化和因单体电池一致性问题而带来的积累效应。整组检测无法检测电池及电池组实际容量,无法筛选其中已老化的电池。
实用的方法是检测每一个单体电池。但对于串联形成的电池组,要自动检测每个单体电池的端电压所遇到的主要问题是测量参考点的选择以及检测电路与被检测电池组的电隔离问题。电位参考点的选择不仅如上所述影响测量精度,还对测量电路的测量范围提出了很高的要求。而被检测电池组与检测电路的隔离不仅涉及到系统的安全还影响检测电路的复杂度和可实现性。目前采用的主要是分布检测和集中检测两种方法。
1)分布检测法
所谓分布式隔离检测技术,就是将单体电池电压及温度的检测模块化、本地化,然后再通过一定的通讯手段将这些检测模块检测的数据集中起来,最后统一处理。这样做的目的就是要解决集中检测方法所存在的种种问题。原理图见图2。
其主要优点是:
(1)连线简单,省去了多路转换开关,性能可靠。
(2)测量精度较高,比较符合汽车电器CAN总线化的发展趋势。
(3)分布式模块解决了参考点问题,利用总线通信方式(采用光耦器件)解决了主控机与电池组的隔离问题。
但应用分布式检测技术还必须解决以下几个问题:
(1)由于检测模块直接从被测电池上持续取电,不利于节能和安全。
(2)当电池较多时,模块数量也多,使得成本和复杂度提高,并且要求通信总线有较高的带载能力。
从功能上看,检测模块主要由检测子模块和通信子模块两大部分组成。检测子模块要完成数据的采集和调理任务,而通信子模块则要沟通与主控电路的信息交流,接收主控电路的指令,上传由检测子模块提供的检测数据。
因为汽车电器的发展方向是采用CAN总线技术,所以,通信子模块与主控电路之间应该采用CAN总线连接。
2)集中检测法
集中检测法(见图3)是用一套检测电路分时检测各个单体电池。检测技术比较直观,为了检测每只电池的电压,需要将每只电池的电压信号引入检测设备(如果蓄电池组由n节单体电池组成,需要引n+1条检测线),采用多通道切换的技术,即通过开关器件(继电器)把多节单体电池的电压信号切换到同一个差分放大器,经信号处理后用一只A/D转换器进行采样。 “开关切换”动态地改变了参考点,保证每次测量都是一个单体电池的端电压;而差分输入则保证了电池组与检测电路不共地,虽然没有做到全隔离,但比共地连接要安全。电池温度的检测一般可采用数字或模拟温度传感器,由于测温过程与电池组没有电连接且技术也比较成熟,所以本文不再赘述。另外,因电动汽车要求的电流较大(几十到几百安),所以对电池组充放电电流的检测,一般采用非接触式电流传感器或变送器实现。
这种方法主要缺点是信号线较多,增大了接线的难度和复杂度,影响测试精度,降低了可靠性。
3)集中/分布式检测法
为克服分布检测法和集中检测法的缺点,我们提出“局部集中”、“整体分布”的检测思路,即将全部电池分成若干个小组,每个小组用一个检测模块进行“集中式”检测,整个系统由若干个检测模块通过CAN总线连接而成。简言之,集中/分布式检测系统的实质就是检测单元部分模块化、本地化,数据靠总线传输。集中/分布式检测除了具有前两种方式的优点之外,还有以下主要优点:加强了组建系统的灵活性和扩充性;增加了系统的可靠性;具有较高的性价比。
对于铅酸电池,由于其单体电压较高、体积较大、数量较少,所以可给每2个或每4个电池配一个检测模块。而对于像锂电池这类单体电压较低、体积小但数量多的电池组,可将2~8个电池分为一组。图4是集中/分布式检测框图。
为了降低成本、缩小体积、简化电路,电池检测模块应由单片机完成。单片机选型的主要条件是:至少有4路10位精度以上的A/D转换器(因为一块电池至少需要电压和温度2路检测);带有CAN总线控制器。
我们选用微芯公司(MICROCHIP)的PICl8系列用于前端的检测模块。该系列的PICl8F248/258和PIC18F2585/2680都是28脚双列直插封装,PIC18F248/2587蒂有5路10位A/D转换器;PICl8585/26801带有8路10位A/D转换器,并具有纳瓦电源管理技术使芯片的功耗进一步降低。PICl8F2585/2680还具有在线串行编程技术,允许单片机在嵌置到电路板之后进行编程,为使用提供了极大的方便。
在我们的课题中采用了24节12V铅酸电池,分为三组摆放在车内,两边的行李箱位置各摆放6节电池,尾部行李箱位置摆放12节电池,2节电池共用一个检测模块,即一个检测模块集中检测2块电池的状态。最后需要说明的是,由于温度传感器与电池没有电接触,所以检测示意图中没有画出温度检测部分,但每个检测模块都有温度检测功能。
为了克服模块从电池上持续取电的问题,我们将所有模块统一供电,由一个总开关控制。这就牵涉到供电回路与电池的隔离问题。为解决该问题,我们采用“桥电容”技术。图5是模块内部框图。“桥电容”的工作原理是这样的:MCU首先将双刀单掷开关K1合上,则电池对电容C1充电,由于时间常数很小,电容端电压很快达到电池端电压;然后MCU断开K1合上K2,从A/D上就可采集到C1的端电压,也就是电池的端电压;最后MCU断开K2。从而完成一次采集任务。另外,当模块不加电时,两组开关是断开的,模块不会从电池取电。可见,这种方式不但解决了参考点问题,而且完全隔离了电池与检测电路,其主要缺点是每个模块增加了两组可控开关。可控开关选用光耦继电器AQW212。模块的成本在200元左右,非常适合电动车辆的使用。各检测模块将数据通过CAN总线上传给主控机。由主控机进行处理并显示出来,供驾驶员参考。
3 结束语
(1)采用集中/分布式检测方法对蓄电池组参数进行检测,较好地克服了集中式和分布式检测方法存在的问题,更适合电动汽车电池组的检测。
(2)利用“桥电容”技术传递所采集的蓄电池电压信号,可有效地解决蓄电池和检测电路间的隔离问题。
(3)通过在24块12V铅酸电池组上的试验,由12个检测模块和1个主控机构成的集中/分布式检测系统工作正常,电压、电流和温度的检测数据准确、可靠,表明集中/分布式检测方法切实可行,具有较高的应用价值。
上一篇:汽车应用中的IGBT功率模块
下一篇:一种汽车用金卤灯的快速点亮电路
推荐阅读最新更新时间:2023-10-18 16:04
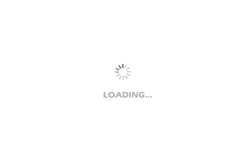
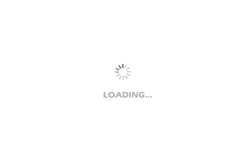
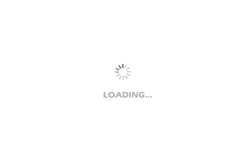
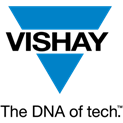
Vishay线上图书馆
- 选型-汽车级表面贴装和通孔超快整流器
- 你知道吗?DC-LINK电容在高湿条件下具有高度稳定性
- microBUCK和microBRICK直流/直流稳压器解决方案
- SOP-4小型封装光伏MOSFET驱动器VOMDA1271
- 使用薄膜、大功率、背接触式电阻的优势
- SQJQ140E车规级N沟道40V MOSFET

- 恩智浦发布首个超宽带无线电池管理系统解决方案
- 非常见问题解答第223期:如何在没有软启动方程的情况下测量和确定软启动时序?
- Vicor高性能电源模块助力低空航空电子设备和 EVTOL的发展
- Bourns 推出两款厚膜电阻系列,具备高功率耗散能力, 采用紧凑型 TO-220 和 DPAK 封装设计
- Bourns 全新高脉冲制动电阻系列问世,展现卓越能量消散能力
- Nexperia推出新款120 V/4 A半桥栅极驱动器,进一步提高工业和汽车应用的鲁棒性和效率
- 英飞凌推出高效率、高功率密度的新一代氮化镓功率分立器件
- Vishay 新款150 V MOSFET具备业界领先的功率损耗性能
- 强茂SGT MOSFET第一代系列:创新槽沟技术 车规级60 V N通道 突破车用电子的高效表现