1、引言
表面组装技术在减小电子产品体积、重量和提高可靠性等方面的突出优点,迎合了未来制造技术的要求。但是,要制定和选择适用于具体产品的表面组装工艺不是简单的事情,因为SMT技术是涉及了多项技术的复杂的系统工程,其中任何一项因素的改变均会影响电子产品的焊接质量。元器件焊点的焊接质量是直接影响印制电路组件(PWA)乃至整机质量的关键因素。它受许多参数的影响,如焊膏、基板、元器件可焊性、丝印、贴装精度以及焊接工艺等。我们在进行SMT工艺研究和生产中,深知合理的表面组装工艺技术在控制和提高SMT生产质量中起到至关重要的作用。本文就针对所遇到的几种典型焊接缺陷产生机理进行分析,并提出相应的解决方案。
2、几种典型焊接缺陷及解决措施
2.1 波峰焊和回流焊中的锡球
锡球的存在表明工艺不完全正确,而且电子产品存在短路的危险,因此需要排除。国际上对锡球存在认可标准是:印制电路组件在600范围内不能出现超过5个锡球。产生锡球的原因有多种,需要找到问题根源。
2.1.1 波峰焊中的锡球
波峰焊中常常出现锡球,主要原因有两方面:第一,焊接印制板时,印制板上通孔附近的水分因受热而变成蒸汽。如果孔壁金属镀层较薄或有空隙,水汽就会通过孔壁排除,如果孔内有焊料,当焊料凝固时水汽就会在焊料内产生空隙(针眼),或挤出焊料在印制板正面产生锡球。第二,在印制板反面(即接触波峰的一面)产生的锡球是由于波峰焊接中一些工艺参数设置不当而造成的。如果助焊剂涂覆量增加或预热温度设置过低,就可能影响焊剂内组成成分的蒸发,在印制板进入波峰时,多余的焊剂受高温蒸发,从锡槽中溅出来,在印制板面上产生不规则的焊料球。针对上述两个原因,我们采取以下相应的解决措施:第一,通孔内适当厚度的金属镀层是很关键的,孔壁上的铜镀层最小应为25um,而且无空隙。第二,使用喷雾或发泡式涂覆助焊剂。发泡方式中,在调节助焊剂的空气含量时,应保持尽可能产生最小的气泡,泡沫与PCB接触面相对减小。第三,波峰焊机预热区温度的设置应使线路板顶面的温度达到至少100°C。适当的预热温度不仅可消除焊料球,而且可以避免线路板受到热冲击而变形。
2.1.2 回流焊中的锡球
2.1.2.1 回流焊中锡球形成的机理
回流焊接中出的锡球,常常藏于矩形片式元件两端之间的侧面或细距引脚之间。在元件贴装过程中,焊膏被置于片式元件的引脚与焊盘之间,随着印制板穿过回流焊炉,焊膏熔化变成液体,如果与焊盘和器件引脚等润湿不良,液态焊锡会因收缩而使焊缝填充不充分,所有焊料颗粒不能聚合成一个焊点。部分液态焊锡会从焊缝流出,形成锡球。因此,焊锡与焊盘和器件引脚润湿性差是导致锡球形成的根本原因。
2.1.2.2 原因分析与控制方法
造成焊锡润湿性差的原因很多,以下主要分析与相关工艺有关的原因及解决措施:
a)回流温度曲线设置不当。焊膏的回流是温度与时间的函数,如果未到达足够的温度或时间,焊膏就不会回流。预热区温度上升速度过快,达到平顶温度的时间过短,使焊膏内部的水分、溶剂未完全挥发出来,到达回流焊温区时,引起水分、溶剂沸腾,溅出焊锡球。实践证明,将预热区温度的上升速度控制在1~4°C/s是较理想的。
b)如果总在同一位置上出现焊球,就有必要检查金属板设计结构。模板开口尺寸腐蚀精度达不到要求,对于焊盘大小偏大,以及表面材质较软(如铜模板),造成漏印焊膏的外形轮廓不清晰,互相桥连,这种情况多出现在对细间距器件的焊盘漏印时,回流焊后必然造成引脚间大量锡珠的产生。因此,应针对焊盘图形的不同形状和中心距,选择适宜的模板材料及模板制作工艺来保证焊膏印刷质量。
c)如果在贴片至回流焊的时间过长,则因焊膏中焊料粒子的氧化,焊剂变质、活性降低,会导致焊膏不回流,焊球则会产生。选用工作寿命长一些的焊膏(我们认为至少4小时),则会减轻这种影响。
d)另外,焊膏印错的印制板清洗不充分,使焊膏残留于印制板表面及通孔中。回流焊之前,被贴放的元器件重新对准、贴放,使漏印焊膏变形。这也是造成焊球的原因。
因此,应加强操作者和工艺人员在生产过程的责任心,严格遵照工艺要求和操作规程行生产,加强工艺过程的质量控制。
2。2 立片问题(曼哈顿现象)
矩形片式元件的一端焊接在焊盘上,而另一端则翘立,这种现象就称为曼哈顿现象。引起该种现象主要原因是元件两端受热不均匀,焊膏熔化有先后所致。在以下情况会造成元件两端热不均匀:
a)有缺陷的元件排列方向设计。我们设想在再流焊炉中有一条横跨炉子宽度的再流焊限线,一旦焊膏通过它就会立即熔化。片式矩形元件的一个端头先通过再流焊限线,焊膏先熔化,完全浸润元件的金属表面,具有液态表面张力;而另一端未达到183°C液相温度,焊膏未熔化,只有焊剂的粘接力,该力远小于再流焊焊膏的表面张力,因而,使未熔化端的元件端头向上直立。因此,保持元件两端同时进入再流焊限线,使两端焊盘上的焊膏同时熔化,形成均衡的液态表面张力,才能保持元件位置不变。
b)在进行汽相焊接时印制电路组件预热不充分。汽相焊是利用惰性液体蒸汽冷凝在元件引脚和PCB焊盘上时,释放出热量而熔化焊膏。汽相焊分平衡区和饱和蒸汽区,在饱和蒸汽区焊接温度高达217°C,在生产过程中我们发现,如果被焊组件预热不充分,经受一百多度的温差变化,汽相焊的汽化力容易将小于1206封装尺寸的片式元件浮起,从而产生立片现象。我们通过将被焊组件在高低箱内以145°C-150°C的温度预热1-2分钟,然后在汽相焊的平衡区内再预热1分钟左右,最后缓慢进入饱和蒸汽区焊接,最终消除了立片现象。
c)焊盘设计质量的影响。若片式元件的一对焊盘大小不同或不对称,也会引起漏印的焊膏量不一致。小焊盘对温度响应快,其上的焊膏易熔化,大焊盘则相反,所以,当小焊盘上的焊膏熔化后,在焊膏表面张力作用下,将元件拉直竖起。焊盘的宽度或间隙过大,也都可能出现立片现象。严格按标准规范进行焊盘设计是解决该缺陷的先决条件。
2.3 细间距引脚桥接问题
导致细间距元器件引脚桥接缺陷的主要因素有:a)漏印的焊膏成型不佳;b)印制板上有缺陷的细间距引线制作;c)不恰当的回流焊温度曲线设置等。因而,应从模板的制作、丝印工艺、回流焊工艺等关键工序的质量控制入手,尽可能避免桥接隐患。
2.3.1模板材料的选择
SMT工艺质量问题70%出自于印刷这道工序,而模板是必不可少的关键工装,直接影响印刷质量。通常我们使用的模板材料是铜板和不锈钢板。不锈钢板与铜板相比有较小的摩擦系数和较高的弹性,因此在其它条件一定的情况下,更有利于焊膏脱模和焊膏成型。通过0.5mm引脚中心距QFP208器件组装试验统计,因铜模板漏印不合格而造成的疵点数占器件总焊点数(208个)的20%左右;在其它条件一定的情况下,利用不锈钢模板漏印,造成的疵点率平均为3%。因此,对引脚中心距为0.635mm以下的细间距元器件的印刷,提出必须采用不锈钢板的要求,厚度优选0.15mm~0.2mm。
2.3.2丝印过程工艺控制
焊膏在进行回流焊之前,若出现坍塌,成型的焊膏图形边不清晰,在贴放元器件或进入回流焊预热区时,由于焊膏中的助焊剂软化,会造成引脚桥接。焊膏的坍塌是不合适的焊膏材料和不宜的环境条件所致,如较高的室温会造成焊膏坍塌。在丝印工序中,我们通过以下工艺的调整,小心地控制焊膏的流变特性,减少了坍塌。
a)丝印细间距引线,通常选用厚度较薄的模板。为避免漏印的焊膏量偏少,所需的焊膏黏度应较低,这样焊膏流动性好,易漏印,而且模板与PCB脱模时不易带走焊膏,保证焊膏涂覆量。但同时为了保持焊膏印刷图形的理想形态,又需要较高的焊膏黏度。我们解决这一矛盾的方法是选用45-75um的更小粒度和球形颗粒焊膏。另外,在丝印时保持适宜的环境温度,焊膏黏度与环境温度的关系式表示如下:
logu=A/T+B--(1)
式中:u-粘度系数;
A,B-常数;
T-绝对温度。
通过上式可看出,温度越高,粘度越小。因此,为获得较高的粘度,我们将环境温度控制20+3°C。
b)刮刀的速度和压力也影响焊膏的流变特性,因为他们决定了焊膏所受的剪切速率和剪切力大小。焊膏黏度与剪切速率的关系如图2所示。在焊膏类型和环境温度较合适的情况下,在刮刀压力一定的情况下,将印刷速度调慢,可以保持焊膏黏度基本不变,这样供给焊膏的时间加长,焊膏量就增多,而且有好的成型。另外,控制脱模速率的减慢和模板与PCB的最小间隙,也会在减少细间距引脚桥接方面起到良好的效果。根据我们使用的SP200型丝印机,我们认为印刷细间距线较理想的工艺参数是:印刷速度保持在10mm/s-25mm/s;脱模速率控制在2s左右;模板与PCB的最小间隙小于等于0.2mm。
2.3.3 回流过程工艺控制
细间距引线间的间距小、焊盘面积小、漏印的焊膏量较少,在焊接时,如果红外再流焊的预热区温度较高、时间较长,则会有较多的活化剂在达到回流焊峰值温度区域前就被耗尽。然而,只有当在峰值区域内有充足的活化剂释放被氧化的焊粒,使焊粒快速熔化,从而湿润金属引脚表面,才能形成良好的焊点。免清洗焊膏,活化程度比要清洗的焊膏低,所以如果预热温度和预热时间设置稍不恰当,便会出现焊接细间引线桥接现象。我们通过降低热温度和缩短预热时间来控制焊膏中活化剂的挥发,保证了免清冼焊膏在焊接温度区域的流动性和对金属引线表面的润湿性,减少了细间距线的桥接缺陷。针对细间距器件和阻容器件,我们采用的回流温度焊接曲线典型例图如图3所示。
3 、结束语
随着表面组装技术更广泛、更深入的应用于各个领域,SMT焊接质量问题引起人们高度重视。SMT焊接质量与整个组装工艺流程各个环节密切相关,为了减少或避免上述焊接缺陷的出现,不仅要提高工艺人员判断和解决这些问题的能力,还要注重提高工艺质量控制技术、完善工艺管理,制定出有效的控制方法。只有这样才能提高SMT焊接质量,保证电子产品的最终质量。
上一篇:低成本光电寻迹智能车设计与实现
下一篇:停产潮袭 光伏产业园“一地尴尬”
推荐阅读最新更新时间:2023-10-18 16:41
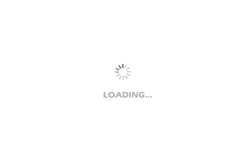
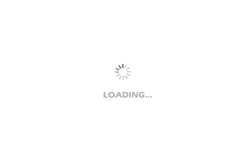
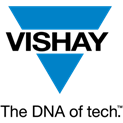
Vishay线上图书馆
- 选型-汽车级表面贴装和通孔超快整流器
- 你知道吗?DC-LINK电容在高湿条件下具有高度稳定性
- microBUCK和microBRICK直流/直流稳压器解决方案
- SOP-4小型封装光伏MOSFET驱动器VOMDA1271
- 使用薄膜、大功率、背接触式电阻的优势
- SQJQ140E车规级N沟道40V MOSFET

- Vishay推出适用于恶劣环境的紧凑型密封式SMD微调电阻器
- MathWorks 和 NXP 合作推出用于电池管理系统的 Model-Based Design Toolbox
- 意法半导体先进的电隔离栅极驱动器 STGAP3S为 IGBT 和 SiC MOSFET 提供灵活的保护功能
- 全新无隔膜固态锂电池技术问世:正负极距离小于0.000001米
- 东芝推出具有低导通电阻和高可靠性的适用于车载牵引逆变器的最新款1200 V SiC MOSFET
- 【“源”察秋毫系列】 下一代半导体氧化镓器件光电探测器应用与测试
- 采用自主设计封装,绝缘电阻显著提高!ROHM开发出更高电压xEV系统的SiC肖特基势垒二极管
- 艾迈斯欧司朗发布OSCONIQ® C 3030 LED:打造未来户外及体育场照明新标杆
- 氮化镓取代碳化硅?PI颠覆式1700V InnoMux2先来打个样
- Allegro MicroSystems 在 2024 年德国慕尼黑电子展上推出先进的磁性和电感式位置感测解决方案
- 左手车钥匙,右手活体检测雷达,UWB上车势在必行!
- 狂飙十年,国产CIS挤上牌桌
- 神盾短刀电池+雷神EM-i超级电混,吉利新能源甩出了两张“王炸”
- 浅谈功能安全之故障(fault),错误(error),失效(failure)
- 智能汽车2.0周期,这几大核心产业链迎来重大机会!
- 美日研发新型电池,宁德时代面临挑战?中国新能源电池产业如何应对?
- Rambus推出业界首款HBM 4控制器IP:背后有哪些技术细节?
- 村田推出高精度汽车用6轴惯性传感器
- 福特获得预充电报警专利 有助于节约成本和应对紧急情况