目前,国内多数船舶的机舱服务设备仍采用大量的继电器、接触器、时间继电器组成,实现各种控制功能,它们的共同特点是线路复杂、可靠性差、有时容易出现误动作,特别是触头氧化及铁芯与衔铁弄脏后的吸力不足,机械运动部件运动不灵活而出现被卡烧坏线圈等故障,给维护过程带来极大不便,甚至会影响正常营运工作,而且,这种设备体积大、重量重、价格贵。因此采用先进的设计思想对船用控制系统进行全新设计尤为必要。
1 单片机智能辅助锅炉控制系统原理
基于单片机的船舶辅助锅炉控制系统的工作原理如图1—1所示。系统的被控对象是锅炉,执行机构是锅炉的风、油门驱动电器,被控参数为锅炉内的压力,本系统利用压力传感器检测锅炉内的压力,传感器输出的电信号经信号变换后送至单片机智能控制器,控制器根据此信号的大小,利用智能控制算法计算出输出控制信号,经放大器放大后以调节风、油门的大小,从而控制锅炉内的压力。
2 智能控制器的设计
众所周知,二阶系统是工程上最常见而又最重要的一类系统,这一系统的形式代表了许许多多控制系统的动力学特征。正因为如此,经典控制理论将二阶系统作为典型系统,并通过对二阶系统阶跃响应的过渡过程分析,定义了表示系统控制质量的一些特征量,其中以调节时间、最大超调量和稳态误差3个特征量作为性能指标。但是,控制系统的动态过程是不断变化的,以常规PID控制器控制,难以解决稳定性和准确性之间的矛盾,原因在于这种控制方式以不变的统一模式之间的矛盾,原因在于这种控制方式以不变的统一模式来处理变化多端的动态过程。
为了有效地模拟人的智能控制行为,并采用微机实现智能控制,在模糊控制中通常采用误差e和误差变化率Δe作为描述控制系统动态特征的输入变量。根据船舶辅助锅炉控制系统的特点,从误差e和误差变化率Δe这两个基本的模糊控制变量出发,引出两个特征变量e·Δe和Δe/e,利用这些信息设计智能控制器。
[page]
2.1 利用e·Δe取值量是否大于0,可以描述系统动态过程误差变化的趋势
对于图2—1所示典型二阶系统阶跃响应动态曲线可知,当e·Δe<0时,如BC段和DE段,表明系统的动态过程正向着误差减小的方向变化。当e·Δe>0时,在AB段和CD段,表明系统的动态过程正向着误差增大的方向变化。
在控制过程中,微机很容易识别en·Δen的符号,从而掌握系统动态过程的行为特征,以便更好地制订下一步控制策略。
2.2 利用Δe/e描述系统动态过程中误差变化的姿态
如图2—1中A、C、E点的|Δe/e|较大,说明该点处的某一段,动态过程呈现误差小而误差变化率大,B、D点的|Δe/e|较小,说明该点处的某一段,动态过程呈现误差大而误差变化率小。将Δe/e和e·Δe联合使用,可对动态过程作进一步的划分。
2.2.1 如图2—1 OA段,e>0,e·Δe<0,实际值正不断地接近设定值,若Δe>a,(a为根据需要而确定的常数)表明实际值趋向设定值的强度较大,为防止过冲,应减小控制器的输出。此时控制器的输出U(k)为:
k1、k2为大于0的系数。在OA段e (k)>0,Δe/e<0,而且在A点处|Δe/e|值最大,0点处|Δe/e|值最小,说明,输入从0点上升到A点的过程中,U(k)先是增加,但越接近A点U(k)值增加越少,在靠近A点的某一段U(k)值开始逐渐减小,这样可以防止被控系统动态过程由于惯性而产生较大的超调,适当选择k1和k2的值,既有利于减小超调而又不致于影响上升时间。k2的作用在A点处最强。
2.2.2 如图2—1 AB段,e<0,e·Δe>0,实际值正不断地远离设定值,在A点处|Δe/e|最大,在B点处|Δe/e|最小,为了使系统尽快地进入稳定状态,此时应减少控制器输出:
式中:k3>0;k4<0;故k4的作用在A点处最强。
2.2.3 如图2—1 BC段,e<0,e·Δe<0,实际值正不断地接近设定值,由于系统的惯性,输出值经C点后并没有进入稳态,而是到达D点,故在C点附近应加大U(k):
式中:k5>0;k6<0;故k6的作用在C点处最强;
2.2.4 如图2—1 CD段,e·Δe>0,e>0,应增加控制器的输出。
U(k)=U(k-1)+k7e(k)+k8·Δe/e(2—4)
式中:k7>0;k8>0;故k8的作用在C点处最强;
上述各参数的在线整定很重要,直接影响控制性能,根据控制趋势,应有k1>k3>k5>k7≥0,k2>|k4|>|k6|>k8≥0,若k2、k4、k6、k8为0,则没有该项的控制作用。
2.2.5 当|e|≥emax,偏差过大,采用砰—砰控制,输出控制量最大(或最小),尽快减小偏差,即
因为本控制系统的执行机构为电动阀门,所以Umax对应的状态为阀门全开,Umin对应的状态为阀门全关。
2.2.6 当|e|<emin时,偏差已达到允许范围,控制量不变,维持原状,即
智能控制算法流程图如图2—2所示。
3 智能控制器在8032单片机上的实现
3.1 硬件设计
整个系统硬件电路由CPU及外围芯片组成,其结构框图如图3—1所示,完成数据采集、声光报警、输出控制、键盘输入及显示、监控定时等功能。
3.1.1 数据采集部分由压力传感器、变送器、精密电阻、A/D转换器等组成。变送器将来自压力传感器的压力信号转换成4~20 mA的电流信号通过精密电阻再将其转换成1~5 V的电压信号,此信号经ADC0809送入CPU。
[page]
3.1.2 本系统CPU采用8032单片机,在此基础上进行以下扩展:以一片16K×8 位CMOS静态E-PROM27128作为程序存贮器,以一片8K×8位CMOS静态RAM6264作为数据存贮器,附加一片DS1216多功能日历时钟,DS1216器件内部包含振荡电路和后备锂电池,它的上面附带有一个28脚插座,插入RAM6264后可以保持RAM中的数据在停电时也不丢失。以一片8155作为扩展I/O口,其中PA口作为检测信号输入口,PB口作为声光报警输出口。
3.1.3 输出控制部分由信号输出,信号驱动及驱动电机组成,控制信号由CPU经DAC0832数模转换后送出,经驱动电路放大后送给驱动电机控制锅炉风门及喷油电磁阀的开度,进而控制锅炉内压力的大小。
3.1.4 键盘显示部分采用专用键盘显示芯片8279,该芯片具有自动对键盘显示器扫描并识别键盘上闭合键号的功能,不仅可以大大节省CPU对键盘显示器的操作时间,从而减轻CPU的负担,而且显示稳定、程序简单,不会出现误操作。键盘部分主要用于输入智能控制算法的一些初始值及参数,显示器采用8 位LED显示器。
3.1.5 监控定时部分,为防止由于外界电源、电磁辐射等引起的干扰使程序偏离正常的控制流程,进入死循环,造成系统故障,本系统利用定时器及分频器,由硬件构成Watchdog,实现监视定时器定时复位功能。
3.2 软件设计
软件设计主要包括:水位控制,燃烧程序控制,压力智能控制,安全保护等模块。
3.2.1 工作原理
为了使锅炉安全运行,控制锅炉启动有一定的程序,当锅炉水位正常,即水位处于高水位与低水位之间(P1.1=0,P1.2=0),蒸气压力低于最大允许点火压力(PA.1=1)时,风机将自动启动(置P1.4=1),先进行40 s的预扫气,此时风门最大(直接置DAC0832输出为FFH),以排除残存在炉膛内的油汽,防止点火时发生冷爆,预扫气快结束时,接通点火变压器(置P1.6=1),启动燃油泵(置P1.5=1),把风门及喷油电磁阀开度调小(直接置DAC0832输出为一个较小的值),以利于点火成功。这时炉膛内风、油、火齐全,如点火成功,光敏电阻阻值下降(PA.0=0),点火变压器停止点火(置P1.6=0),这样燃油经电磁阀继续喷到已点着的火焰上,在风机的助燃下正常燃烧,进入压力智能控制程序,如果点火失败,光敏电阻阻值很大(PA.0=1),则系统发出点火失败声光报警(置PB.1=1),并自动进行第二次循环,关闭风门及喷油电磁阀(置DAC0832输出为00H),从40 s预扫气开始循环,若第二次循环仍未点火成功,系统停止工作(置P1.7=1)且声光报警。
当正常燃烧突然熄火(PA.0=1),系统发出中途熄火声光报警(置PB.2=1),同理,程序控制系统自动从头开始,等待炉内压力下降至PA.1=1,然后进入40 s预扫气,重新点火启动。
当锅炉正常燃烧后,本系统按照智能控制算法控制风门及油门驱动电机以控制风、油门大小,使炉内压力维护在一个稳定的范围内。
本系统的水位控制由直接放在主程序之前及之后的高低水位判断指令来决定是否启停给水泵,若检测到高水位信号(P1.2=1),说明之前启动过给水泵,此时应停止给水泵工作(置P1.3=0)反之,若检测到低水位信号(P1.1=1),则置P1.3=1,此时应启动给水泵工作。
安全保护中的压力危险(PA.2=1),水位危险(P1.0=1),中途熄火(PA.0=1)等保护也由接在主程序之后的判断指令来完成的,若PA.2=1或P1.0=1,则停止系统工作(置P1.7=1)并且声光报警,若PA.0=1,中途熄火,则关闭风油门(置0832输出为OOH),停止风机及燃油泵工作(置P1.4=0,P1.5=0),并作中途熄火声光报警,程序自动重新开始。
3.2.2 主程序流程图
船舶辅助锅炉微机控制系统的主程序包括系统初始化、锅炉水位控制、燃烧程序控制、锅炉蒸汽压力自动控制、安全保护等模块。其流程图如图3—2所示。
4 结束语
经样机实验证明本系统由于采用了基于8032单片机的智能控制方式,与全部采用继电——接触器或PLC的辅助锅炉自动控制系统相比,具有硬件电路简单、价格低廉、无触点等优点,同时系统动静态特性得到很大改善,系统的水位控制、燃烧程序控制、蒸汽压力控制、安全保护、故障检测等功能均由8032单片机完成,充分体现了单片机组成的系统的优越性。
[参考文献]
[2] 李朝青.单片机原理及接口技术[M].北京航空航天大学出版社.
[3] 涂时亮.单片微机控制技术[M].复旦大学出版社.
[4]冒天诚.船舶电力拖动自动控制系统[M].人民交通出版社.
[5] 李士勇.模糊控制、神经控制和智能控制论[M].哈尔滨:哈尔滨工业大学出版社,1993.
上一篇:利用微处理器监控电路提高单片机系统与掉电保护电路的可靠性
下一篇:基于单片机的Internet连接技术与方法
推荐阅读最新更新时间:2024-03-16 12:52
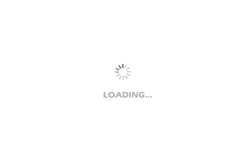
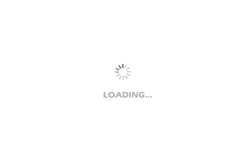
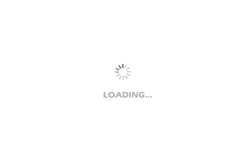
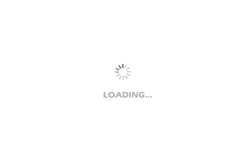