0 引言
为了满足加工精度、加工速度等要求。当今的机床加工设备都装备了大量的电子设备,因此加工设备之间的通信成为加工自动化的基础,这就对通信网络的实时性、稳定性、安全性等都提出了较高的要求。目前加工设备之间常用的信息传送方式有RS-232、RS-422等,但这些都已无法满足加工自动化的需要。CAN作为一种现场总线.具有突出的可靠性、实时性和灵活性等特点,可完成现场自动化设备之间的多点数字通信,实现底层设备与外界的信息交换,是机械加工设备理想的通信手段。本文基于CAN总线控制系统的研究。介绍了CAN总线控制系统在机床加工中的应用,设计了一种基于CAN总线的机床加工控制系统,具有自动化程度高、实时性强、加工精度高等特点。
1 CAN总线特点概述
在20世纪80年代初期。德国Bosch公司为了解决汽车中众多的控制与测量设备之间的数据交换,开发了一种串行数据通信总线,这是最初的CAN(Controller Area Network)总线。CAN总线是一种有效支持分布式控制系统或实时控制的串行通信网络,通过该网络来实现远距离实时数据的可靠传输。
CAN总线为多主方式工作,支持热插拔。增加了通信的灵活性,网络上的节点均可实时地、并行地、主动地向网络上其他节点发送信息;采用非破坏性的总线仲裁,当多节点同时向总线发送信息报文时,优先级低的节点主动停止数据发送,而优先级高的节点可以不受影响地继续发送数据;具有点对点、一点对多点以及全局广播传送数据的功能;通信距离远,可达10km.通信速度高,可达1Mb/s;具有较高的性价比,
结构简单。器件容易购置,每个节点的价格较低:通信介质可为双绞线、同轴电缆或光纤。选择灵活;将业务数据打包成报文发送,每一个信息报文的有效字节数为8个,这种方式传输时间短、实时性高、抗干扰性强,能减少重发信息报文的机率;采用位校验、填充位校验、循环冗余校验(CRC)和数据帧格式校验.数据出错概率在10叫5以下,同时如果CAN节点出错次数大于一定数量时,可自动退出总线,使错误节点对总线的干扰降到最低。
综上所述,CAN总线具有众多的卓越特性,通过CAN总线将现场加工设备连接起来具有其他通信方式所无法比拟的优点。使得机床加工自动化程度大大提高。
2 CAN控制系统组成及原理设计
系统通信网络拓扑结构采用总线式结构(见图1),多节点共用一条传输线,整个系统可以分为上、下两层。上层是控制计算机和CAN适配卡,下层由若干个控制单元组成。
上层的控制计算机是一台高性能的PC,其主要功能为向用户提供人机交互界面、存储现场数据、控制加工过程等。控制计算机可以远程监视和控制每个现场控制单元.并且将数据实时地上报给用户。CAN适配卡一端与总线相连。另一端与控制计算机相连。它将控制计算机的操作信号和控制参数传送给指定的现场控制单元,同时,将控制单元的数据传输给控制计算机做进一步的处理。
下层的现场控制单元是由带有CAN接口的嵌入式模块组成。按功能主要分为:数据采集模块、控制模块,传输模块、输入/输出模块等。其主要功能如下:
(1)数据传输:现场控制单元负责向控制计算机实时传送进给速度、切削深度等加工过程的参数,以及向下级设备传送控制计算机的加工指令。
(2)监控管理:完成对机床的基本数据处理、故障诊断和报警、参数设置、时钟校对等监控和管理工作。
加工控制过程为:控制计算机根据用户设定的相关参数选择控制方式和执行机构。现场控制单元将采集到的数据通过CAN总线实时地发送给控制计算机。控制计算机的决策软件根据上报数据和用户设定的参数进行运算,随即向下层传输控制量,指示相关机构执行动作。整个过程无需人工干预,实现了高精度和智能化。
3 CAN控制系统硬件设计
由图1系统结构可知,系统硬件主要包括:控制计算机、CAN适配卡、CAN总线和现场控制单元。控制计算机采用高性能工业控制计算机。负责系统的初始化、通信管理、加工控制等。CAN适配卡的选用应利于与工控机的连接。利于接口设计,目前市场上有多家公司的产品可供选购。如三兴达公司。它通过软、硬件设置可以将双口RAM映射成PC机的物理内存。使收发数据相当于直接向内存读写数据,从而提高了数据交换的速率。
控制单元是实时数据、加工指令等任务的物理载体。它主要由嵌入式处理单元、CAN控制器、CAN收发器、光电隔离电路、存储单元、I/O等构成。图2为控制单元硬件结构图。
嵌入式处理单元一般选取其内部具有4 kB以上程序存储能力的单片机。存储单元存放初始化参数、用户自定义的数据、一些简单的加工程序,以及微处理器在运算、测量、控制时的有关数据。
CAN总线主要有两大类:独立的CAN控制器与微控制器结合使用和带有CAN控制器的微处理器。针对系统的要求和开发环境,CAN控制器应能够完成CAN协议所规定的物理层和数据链路层的所有功能,具有完成高性能通信协议所要求的全部特性。光电隔离电路可增强控制节点的抗干扰能力,防止线路间串扰。使总线上各个CAN节点之问实现隔离,以保护CAN控制器。另外。总线两端要接上120Q的匹配电阻,以提高整个系统通信的可靠性和抗干扰能力;系统中的单片机时钟与CAN控制器时钟应同步。I/O设备采用小数字键盘和液晶数码管实现。接口电路实现与各种数据采集设备、传感器的连接。[page]
4 软件设计
4.1 控制计算机软件设计
使用CAN适配卡提供的接口函数编程即可开发控制计算机软件,其程序流程见图3。首先进行CAN总线的初始化。主要包括工作方式设置、基本参数设置、接收屏蔽寄存器和接收掩码寄存器的设置等。其次与下层控制单元进行联系,建立传输通路,用户选择加工程序,向下层控制单元传送信号,控制汁算机接收数据,生成加工指令传向下端执行。最后当加工完成后。向控制单元发送结束信号,程序结束。整个加工过程完全由程序控制,自动完成。
4.2 控制单元软件设计
下层的控制单元完成数据传输和对下层设备的监控管理工作。其基本流程见图4。
4.3 硬件的初始化和收、发程序的实现
4.3.1 初始化程序
初始化程序主要包括工作模式的没置、接收滤波方式的设置、接收屏蔽寄存器和接收代码寄存器的设置、波特率参数的设置和中断允许寄存器的设置等。在完成硬件的初始化设置以后,就可以回到工作状态,进行正常的通信任务。
4.3.2收、发程序的实现
初始化工作结束以后就可以向CAN总线进行读写操作。对于数据的收和发,可以采取查询和中断两种方式实现。其中断处理原理为:当接收缓冲器满时,向CPU发出中断请求,通知CPU取走数据;而当写入缓冲区的数据发送完之后,同样通过中断方式告知CPU数据已经发送完成,发送缓冲器已空,可以写人其他的数据。CPU通过中断服务程序对CAN控制器的中断请求做出响应。
5 结束语
CAN总线具有众多的卓越特性,通过CAN总线将现场加工设备连接起来具有其他通信方式所无法比拟的优点,使得机床加工自动化程度大大提高。本文是CAN总线在机械制造领域的一个应用。显示了CAN总线在机械制造领域中的优势。随着人们对CAN总线研究的不断深入,CAN总线控制系统必将在机械制造领域得到更广泛的应用。
上一篇:利用CAN总线的智能监控系统人机交互设计
下一篇:51上移植ucosii的心得
推荐阅读最新更新时间:2024-03-16 13:48
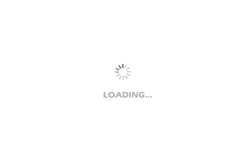
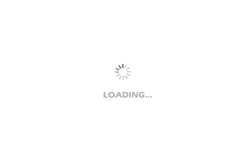
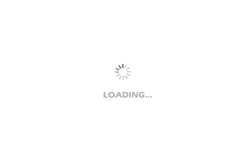