近日,许家印的造车梦又上热搜。只因恒大豪掷5亿元收购泰特机电70%股份,从而拿下轮毂电机领军企业荷兰e-Traction的控制权。
轮毂电机曾被认为是电动汽车驱动系统最理想的解决方案,全球汽车工程师为之不懈奋斗,然而,产业化之路道阻且长。如今,志在实践“造车梦”的许家印强势布局,能否加速推进轮毂电机产业化,迈入电驱动系统的“理想国”呢?
答案,可能不容乐观。
(泰特轮毂电机)
全球汽车产业向电动汽车转型已经成为大势所趋,电动汽车创新驱动技术层出不穷,呈现出百花齐放、前景却扑朔迷离的局面。
当前汽车市场上的纯电动汽车,仍然是中央电机驱动为主,而且多数为单电机+单级减速器(固定速比减速器)的构型。但是,随着电动汽车高时速行驶、长续驶里程的需求越来越高,单电机显得有些力不从心,单级减速器也开始承受越来越严苛的挑战。于是,双电机、多挡变速器的构型开始涌现,不同种类电机和减速器或变速器的集成式驱动结构也被开发出来,却尚未经过大规模市场的检验。与此同时,轮边电机、轮毂电机等分布式驱动的构型也开始装车路试,探索产业化的各种可能性。
一、驱动系统构型将呈现多元化竞争局面
就电机布局位置来看,纯电动汽车驱动系统可以分为中央电机驱动(即集中式驱动)和分布式驱动(即分散式驱动)。
目前在我国约有90%以上的整车企业选择中央电机驱动路线,中央电机驱动成熟度最高,使用最为广泛。集中式驱动技术虽然成熟度较高,但从细分驱动方案来看存在一定着缺陷。业内专家表示,这种直驱电机存在爬坡性能不足、中高速性能欠缺、重量较大、成本较高等问题。改进方向首先是进一步提高电机性能;其次是发展分布式驱动系统;第三是加入两挡或多挡变速器。
实际上,随着纯电动汽车技术研究逐渐深入,其驱动系统的布置结构已经开始由单一动力源的集中式驱动向多动力源的分布式驱动发展。
电机与减速器组合驱动型式是把布置在车架上的电机与单级减速器连接,并通过半轴直接驱动对应车轮,对底盘和空间要求较高,这种布局方式在特斯拉以及一些豪华品牌的电动超跑上有所应用;轮边驱动是将驱动电机布局在车轮旁边,通过减速机构直接驱动车轮行驶,轮边电动机虽然节省了发动机和传动轴,但是由于电机安装在车身,因此对整车的布局控件影响较大;轮毂电机的最大特点驱动电机安装在车轮内部,输出扭矩直接传输到车轮,舍弃了离合器、减速器、传动桥等机械传动部件,这使得汽车机械部分的结构大为简化,轮毂电机系统要比集中式驱动的效率高出13%~16%。
分布式驱动存在的技术难题也不容忽视。轮边电机、轮毂电机都会致使车辆簧下质量变大而影响整车的舒适性和操控性,高速转弯及路面颠簸造成的差速问题仍然没有一个较好的解决方案,另外由于系统部件相对集中,散热和电控系统也有很多问题待解决。同时高昂的成本有不利于轮边电机、轮毂电机的产业化发展。
两挡或多挡变速器也是提高纯电动汽车性能的技术方向。插电混动结构的宝马i8上就匹配了一台结构小巧的两档自动变速器,以提高车辆最高时速。当下,博世提出了将无级自动变速器CVT应用于电气化动力总成系统的新方案,用来提高系统能效、动力性能和降低成本。
多电机布局以及多挡变速器的方案已经开始走向市场,但是未来何种技术能够胜出,现在看来依然不够明朗。未来,新能源汽车企业将面临电机高转速带来的振动、噪声等问题;多挡变速器企业则将迎接平顺性等问题的挑战。一个最大的可能是,单挡与多挡,单电机与多电机,这些构型在一定时期内将会是并存局面。上海车展期间即将举行的第十一届国际汽车变速器及驱动技术研讨会(TMC 2019)电驱动构型进行具体讨论。
二、电机高转速、系统高功率密度带来挑战
纯电动汽车整车及零部件企业一直在不断优化零部件的设计和制造要求,以实现电机的高扭矩、高转速,驱动系统的高功率密度、高度轻量化,以及提高整车运转能效、提升驾驶安全性。
当前,汽车驱动电机的转速已经从过去6000 rpm~9000 rpm,提高到现在的12000 rpm~20000 rpm,这对电机及减速机的热管理、NVH、密封性能等带来了很大挑战。
随着驱动电机的转速和驱动系统集成度的提高,比较突出的是对润滑系统的要求,如何有效实现润滑油的电气兼容性、铜腐保护特性、热氧化稳定性和高速轴承齿轮保护需求、消泡性能等都是新的挑战。驱动系统的高功率密度、高度轻量化让新材料、新技术、新设计得以加速产业化。针对电机高速化、轻量化的要求,NSK开发了牵引驱动减速机构,该减速机构通过油膜传递动力,而非常规的齿轮或钢带,具有静音,高效等优点。针对减速器多挡化和实现电量消耗改善最大化,NSK还开发了扭矩控制、双电机驱动的无换挡冲击的变速机构。
另一方面,新轴承设计方案是有效减少电机和驱动系统摩擦损耗、提高效率的关键,持续优化现有的轴承设计、进一步降低摩擦系数、减少其对应用空间条件的限制成为了重要的突破方向。
三、高度集成化可能是电驱系统的核心方向
无论是制造企业还是研发机构都在探索、发掘、描绘电动汽车驱动系统的终极目标,而实现这一目标的思路就是不断将纯电动汽车驱动系统的高度集成化推向极致。有专家指出,为推动电气化尽快落地,降低成本,提高集成度是大势所趋。
当前,大量驱动电机企业开始向驱动系统供应商转型,产品也由单一的电机变成了电机、减速器、电控系统组成的“三合一”电驱动总成产品,这对变速器企业带来很大的挑战。
整车和零部件制造商的目标是能够以具有尽可能少的装配组件的集成化系统来满足市场的各种要求,这促使电驱动桥等高度集成化新品的出现。电驱动桥实现了驱动电机、功率控制器、变速器、差速器等部件的全面集成,成本更低、体积更小、效率更高,适用于不同平台的设计和应用,为车辆节省大量空间。
(ZF三合一电驱动桥)
目前,舍弗勒、GKN、ZF、博世、东风德纳、麦格纳、博格华纳等企业均已推出了高度集成的电驱动桥系统,他们中的大部分都将在TMC2019上演讲,具体介绍其最新的电驱动产品。ZF的三合一电驱动桥真正实现了高度集成,电机与减速器一体化,不仅是共用壳体,而且是同轴,不像有些企业的方案是分体的。这种集成,不仅能够有效减少体积、降低成本,还能优化NVH性能。GKN的电驱动桥就已经在沃尔沃、宝马等品牌的混动SUV、跑车上得到了成功应用,GKN新一代的电驱动桥在小型化的基础上开始支持扭矩矢量控制,来更好地提升新能源车型的运动性。国内有分析机构指出,到2020年,国内电驱动桥新增市场销量将突破200亿元,纯电动及混动车型都将得到更快速的普及和发展。
上一篇:“宝戴合”,这次为自动驾驶
下一篇:多家欧洲车企将为车辆配置C-ITS技术
推荐阅读最新更新时间:2024-07-25 20:24
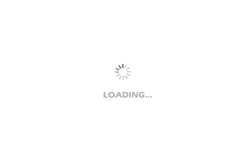
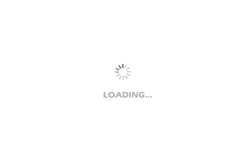
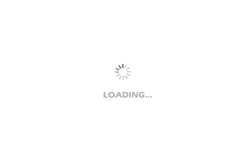
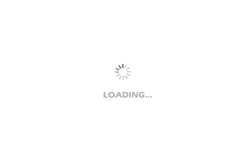

- ZDS2022示波器百集实操视频之87:测量之“真“与”伪”
- Silicon Labs全球率先推出安全Sub-GHz片上系统电池寿命超过10年
- Silicon Mitus为快充应用设计出效率极高的开关电容电荷泵
- Digi-Key与 Siemens 建立合作伙伴关系,分销其自动化和控制产品
- 双向功率转换器受益于 CoolSiCTM MOSFET
- ZDS2022示波器百集实操视频之86: 如何正确测量示波器的底噪
- ZDS2022示波器百集实操视频之85:如何正确测量电源纹波
- 日本半导体产业,为时已晚?
- ZDS2022示波器百集实操视频之84:示波器的带宽
- ZDS2022示波器百集实操视频之83:正占空比搜索