0. 引言
随着国民经济的发展, 电网容量和用电负荷的日益增长, 电力系统对自动化和可靠性的要求越来越高。电力系统自动化对可靠性的需求, 使人们注意到“PLC” (可编程逻辑控制器) 这种高可靠性和强抗工业干扰的技术。90 年代以来, PLC 发展迅猛且应用的局域网技术日趋成熟, 产品不断向系列化、标准化发展, 在自动化控制领域中, 新一代的PLC改名为PCC 已逐渐跃居主导地位, 成为实现自动化控制的关键技术, 在电力系统也不例外。
PCC( Programmable Computer Controller) 是一种可编程计算机控制器, 它是专为在工业环境下应用而设计的工业计算机, 采用“面向用户的指令” , 因此编程方便;它直接应用于工业环境, 具有更强的抗干扰能力、更高的可靠性、广泛的适应能力和应用范围;大容量的存储能力、标准通信接口, 基于过程总线的系统互联、高级语言开发和运行环境,自诊断能力, 都使得PCC 在电力系统的应用具备了出色的友好“平台”。
1. PCC 系统CPU的特点
继承了PLC 与微机技术的PCC 技术形成第一代自动化软硬件平台结构, 采用32 位CISC 和RISC 的CPU, 多处理器结构。图1为本系统所用的CPU 模块结构。图中除了主CPU 外, I/ O – Processor 即I/ O 处理器主要负责独立于CPU的数据传输工作。DPR - Controller 即双向口控制器主要负责网络及系统的管理。一个模块上的3 个处理器,既相互独立, 又相互关联(通过DPR) , 从而使主CPU 的资源得到了合理使用, 同时又最大限度地提高了整个系统的速度。
图1 CPU模块结构
2. PCC 在发电厂监控中的应用
以某热电厂机组设备改造为例, 介绍应用PCC 实现的智能分布式数据采集与监控系统。该热电厂有大小机组7 台, 装机容量194 MW, 现准备对主要的4~5 号机及整个电气系统进行监控系统改造。
2.1 设计原则
系统按分布式结构设计, 采用开放系统、分层控制等先进的计算机设计思想, 将计算机技术、通信和网络技术、数据库技术、图形和图像技术、多媒体技术、数据采集和自动控制技术有机地结合在一起, 技术成熟, 运行经验丰富, 能够满足近期的功能要求和远期的发展需要。整个设计遵照国际90 年代IEC1000 系列标准, 满足ISO9001 国际标准。
(1) 整个系统分为5 个采集控制站, 计有4 号机组监控、5 号机组监控、35 kV 出线监控、同期控制、01/ 1~3 号机/ 6 kV 监控。两个操作员工作站。
(2) 通过计算机对励磁调节器( KFD) 、发电机有功进行遥调。在4、5 号机控制屏上设有手操有功调节和KFD 无功调节及与汽机联系指挥信号。
(3) 不含同期点的出线, 原控制回路取消, 采用计算机控制。含有同期点的出线, 应用成熟的计算机同期装置, 采用计算机控制。
(4) 事故音响, 预告信号原回路取消, 功能由计算机系统实现。
(5) 厂用电BZT功能由计算机实现, 对4、5号机强行励磁及主变风扇启动控制均由计算机来进行判别控制。
2.2 系统结构
系统的网络结构系统配置如图2 所示。
图2 系统配置框图
2.3 系统管理层
操作员工作站、工程师工作站和通讯服务器组成智能分布式系统结构的管理层。
管理层通过PROFIBUS 网络与5 个PCC 采集控制单元相连, 各工作站和服务器分别相当于PROFIBUS 网上的一个独立的结点。
管理层采用多机及双网络方式运行, 各工作站及通讯服务器之间还组成一个小的局域以太网,实现数据的传输与共享, 互为备用, 提高了系统的可靠性; 软件平台采用32 位多任务、多进程设计, 可支持Windows95/ 98/ NT操作系统软件, 配有多种应用软件接口, 并支持OEM开发, 为用户提供了二次开发平台; 硬件平台可采用小型机、微型机或工作站等设备。
通讯服务器完成与地调、模拟盘、GPS 天文时钟接收装置以及电厂已有的几台RTU 设备的通信;还通过HUB 与该厂的MIS 网相连, 实时监控系统与管理信息系统结合在一起, 实现了实时信息的管理。
若用户具备与Internet 连接的条件, 管理层还可以提供PVI 浏览器方案, 实现远方读取数据。[page]
2.4 系统控制层
PROFIBUS 网上的各采集控制单元组成智能分布式系统结构的控制层。控制层按照机组或线路等监控对象的不同分别组屏, 可以使各单元组合置于过程对象附近, 减少电缆投资。各监控单元分别完成相应监控对象的模拟量、数字量采集以及数字量的输出控制。模拟量采集采用交流采样。
系统具有可扩充的模块化结构, 电源、CPU、网络板、I/ O 板、模拟量输入板、通讯板等都是独立的模板以总线方式连接在底板上, 它取代了标准的框架装配的局限性, 可在标准的DIN 轨道上任意拆装、组合。
每个单元都有一电源模块。系统电源是系统可靠性与完整性的第一保证, PCC 的输入电压有AC、DC两种, 可实现交/ 直流切换。
系统配有当地调试通信口, 便于对不同的数据采集与控制设备进行跟踪与调试, 方便了参数设置及运行监视的维护。带电插拔采集板件使得现场维护变得简单方便。
在软件支撑环境方面, PCC 采用高级语言编程, 为用户提供透明的服务接口, 同时, 也支持直流采样, 使得功能实现、系统增容都十分方便灵活。
操作系统为实时多任务系统, 在操作系统中一个任务的循环周期可根据任务的优先级确定。操作系统主要分三层:
(2) PCC 软件包。包括: 系统管理、系统任务、功能库、一般任务、高速任务级、通讯软件。
(3) 应用程序。包括:循环任务、非循环任务。操作系统为保证系统的高可靠性提供了监视和安全的功能, 包括: 模块检测、系统结构检测、栈溢出检测、I/ O 数据传输检测、循环周期检测、硬件看门狗等。
由于PCC 的CPU 采用68000 + RISC 的32 位微处理器, 具有极强的运算处理能力, 可使大量运算、控制功能、保护功能分散在各智能单元, 大大提高了站内通信网的利用率, 使整个系统效率达到最高。另外, 系统软硬件方面良好的自诊断功能,可把故障范围减至最小。
2.5 现场层
智能分布式系统结构的外围层为现场层, 包括采集层使用的传感器、二次控制回路等。
现场层根据现场总线网络传输速率快( ≥500kbps) , 软硬件实现简单的特点, 可以用CANBUS
(或RS485) 来连接厂内的其他自动化装置如保护单元、故障录波、无功补偿设备等的主干网, 并通过现场总线网络连接到采集层, 与上一层进行必要的数据通讯。
2.6 网络通信
采用的PROFIBUS( Process Field Bus) 网络是一种高速数据链路, 是具有标准通讯能力的开放式现场总线, 用于PCC 与PCC 之间, 或与其它接到本网络上的智能设备(如显示单元、上位机等) 间传送数据和系统状态。PROFIBUS 网络作为传输速度最快的现场工业总线(500 kbit/ s~10 Mbit/ s) , 物理连接方式简单, 既可以用双芯屏蔽通讯电缆, 也可以用光纤等;多主多从的“Peer To Peer”方式, 采用Token Ring 结构, 网上最多可连入多达128 个结点, 最大传输距离达4800 m; 与第三方系统通讯方便, 兼容性能;可任意的增加和删除网络结点,而对其他结点和整个网络没有影响, 可靠性高。PROFIBUS 网络协议符合德国国家标准DIN19245。
系统的CPU 模块、专用的网络模块和通讯模块( 本系统未使用) 提供了多种标准通信接口( TTY, RS422 , RS232 , RS485 等) , 使得CPU 的局部I/ O 总线扩展、远程扩展I/ O(通过RS485 电缆)以及CPU 间的现场总线组网非常灵活, 从而方便地实现系统纵向或横向集成。
3. 系统改造后效果
应用PCC 实现的电厂机组设备改造, 充分发挥了可编程编辑控制器( PLC) 的标准控制功能和工业计算机的分时多任务操作系统的集成优势, 不仅方便地实现了各机组、厂变、出线及同期控制单元的开关量和模拟量的采集, 而且其双网络结构的管理层、具有大型机分析运算能力的PCC 模块组成的控制层均为实现发电机有功调节、同期控制、强行励磁、备自投等回路的自动控制提供了可靠的保证, 从而使该电厂的自动化管理水平登上一个新的台阶, 为建立全厂信息监控和管理系统打下良好的基础, 为电厂节能增效、提高供电质量开辟了更广阔的空间。
4. 结束语
总之, 开放式系统平台是当今电力系统自动化发展的方向。现代的PCC 与微机的发展相互渗透, 它已是一种可提供诸多功能、成熟的用户应用控制系统, 而不是一种简单的逻辑控制器, 它已被开发出更多的接口与其它控制设备进行通信, 生成报告, 多任务调度, 可诊断自身故障及机器故障。基于现场总线的智能分布式的新型控制思想, 基于标准化的开放性和兼容性, 通用性和高度专业化的融合, 这些优势使PCC 可以实现电厂的各种运行、分析与控制功能, 能够满足当今的电厂实现生产、管理自动化的需要, 而且具有很高的性能价格比。PCC 应用为电厂全面提高管理水平和经济效益提供了广阔的前景, 是一种值得推广的可行性方案。
上一篇:UPS电源智能监控系统的设计
下一篇:扎堆传感器设计,垂直整合成趋势
推荐阅读最新更新时间:2024-05-02 23:18
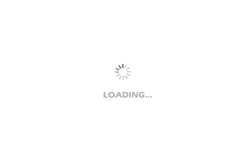
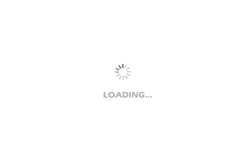