将制造车间的数控设备与计算机联网构成DNC(DistributedNumericalContro1)系统,已成为实现CAD/CAM一体化及计算机辅助生产管理集成化迫切需要解决的核心技术之一。而通信网络的实现又是构建集成DNC系统的最关键的技术,它一般包括两个层次,上层是DNC主机与CAD/CAM/CAPP、 MRPII系统币睥间服务器的通信,下层是DNC主机与车间各种数控设备的通信数控机床联网的方法很多引,如串行通信方法口、MAP通信技术、现场总线、以太网等。这些通信方法虽然在一定程度上实现了数控机床的联网,但在应用中它们或多或少地存在一些不足。为了提高数控机床联网控制系统的可集成性和满足实时调度功能,笔者提出了基于工业以太网的数控机床联网控制系统。
1 系统结构
系统的结构主要根据实际需要而选定,需要考虑的因素主要有车间的环境、工厂的自动化程度与管理层的信息集成等。系统采用工业以太网作为网络平台,工业以太网的抗干扰设计保证了在车间恶劣劣环境下的通信畅通及实时性,且易于与管理层集成。系统采用总线+星型的拓扑结构。主干网采用总线结构,易于组成冗余环网。局部采用星型结构,避免了某一台设备的故障影响其他设备。系统的拓扑结构如图1如示。
实现数控机床和工业以太网连接的协议转换器实质就是工业以太网数据包与RS232数据包的转换器。它向上接人工业以太网,采用工业级RJ45接口形式,向下连接带有RS232串口的数控机床。协议转换器可以作为数控机床的一个部件安装在机床上。
2 系统功能
2.1 通讯功能
(1)NC程序的双向传输所有数控设备实施联网集中管理,利用网络进行NC程序(包括机床参数,刀补文件,宏程序等)的双向传输,从而实现NC程序的海量存储、集成化管理。将每台数控机床定义为客户端设备,利用数控系统自身的通讯端口(一般为RS一232)、通讯功能,操作工可在数控机床端进行数据的双向传输以及访问管理服务器端数据的全部操作,服务器端对数控端的操作请求自动进行相关处理而无需人为干预。保证所有入网数控设备可在同一时刻进行并发式的通讯传输。
(2)在线加工需要数控系统本身支持在线加工功能,可实现断点续传、子程序调用等功能。
(3)数据共享让操作工在本地数控设备访问其他数控设备或虚拟机床信息,方便零件转移加工。
2.2 控制功能
在该模块中DNC服务器与CNC进行通讯,可以实时采集数控机床的加工状态、联网状态、刀具信息、操作履历,以及对刀具寿命进行管理。并且通过一定的权限确认,可以在线修改各种设备参数和运行参数,从而实现底层设备的完全监控。通过对采集到的工况数据进行处理,可以及时获取加工业绩、机床利用率等生产管理所需要的数据。由于生产状况的千变万化,生产过程中会出现很多随机的情况,因此不同地点、不同部门的专业人员要对同一设备进行工作,就需要有一个自由交流的平台,通过网络实现信息交互、经验交流,最终实现设备的远程监控。远程监控模块是利用计算机技术和网络技术,提供广域范围内共享资源的平台,并为实时监测监控、故障诊断提供支持。用户可以随时通过网络查询设备运行状态以及设备现场的工况,对生产过程进行实时的远程监控。
2.3 NC程序管理
NC程序作为加工过程中非常重要的一部分资源,对其进行高效的数据化管理已经成为DNC系统不可缺少的一部分。NC程序的管理根据管理目标对象的不同又可分为对程序进行生命周期内的管理和NC程序内部信息管理。
对NC程序的内部属性进行管理主要包括程序号、程序注释、零件图号、所加工的零件号、加工工序号、加工范围、机床、用户信息等进行管理。在该系统中可对程序根据图号、零件名称、工序、机床等进行多种条件的复合查寻,同时对加工程序编辑历程、所用刀具清单、工艺卡片等进行管理。数控程序员编写的加工程序有时不可能一次就达到加工要求,根据加工过程,将程序分为4个状态:①编辑——程序分处各编程软件指定的文件夹中,由程序员加载至程序库时关联信息包括:程序号,程序名,程序文本,零件号,零件名称,工艺文件名称,工序号,工步号,编写者,编写日期,刀具表,零件图片。②试切——处在试切验证阶段的程序。③锁定——试切无误从机床回传到计算机中的程序。④定型——审核定型归档的程序。[page]
程序管理流程为:编程人员(有编辑修改的权限)编好的程序在完成修改、仿真校验等工作后加载人相应数据库试切验证区,同时填表完成NC程序关联信息的输入,此时程序处于编辑状态,经编程主管(有解锁的权限)审核同意后,将程序改成调试状态,此后可发送到机床试切,也可以从机床的控制面板上远程调用程序;试切验证和调试无错误的程序经程序主管的同意后发回到数据库的锁定区,此时程序状态为锁定;经过技术主管(有批准的权限)审核无误后,正式进入数据库定型归档,程序变成只读属性,以后不能再修改了(只有个别有权限的人可改)。整个管理流程如图2。
3 系统关键部件——转换器设计
工业以太网协议与RS232串口协议转换器的工作原理是,把来自串口设备的任何信息透明地传输到工业以太网上的任何一台计算机,也可以把来自上层的任何控制信息透明地传输给数控设备。通过为协议转换器配置IP地址,数控机床成为网中的一个节点,从而达到集中管理数控机床的功能,如文件传输、状态监控等。协议转换器的结构如图3所示。
协议转换器就是一种嵌入式系统。采用PHILIPS公司生产的 ARM(AdvancedRISCMachines)芯片作为处理器,在ARM公司的集成开发环境ADS1.2(ARMDeveloperSuit) [中,通过在芯片上移植实时操作系统C/OS-Ⅱ及TCP/IP协议,开发基于C/OS-Ⅱ的串口监控软件,实现了串17数据到工业以太网数据包的转换。其工作过程如下:串口监控软件一旦发现串17有数据到达,触发一个中断,系统调用协议转换中断服务程序,将数据转换为工业以太网数据包,然后通过智能交换机发给管理层计算机。整个工作过程如图4所示。
4 结语
工业以太网通信可以满足车间数控机床网络控制的通信要求,基于工业以太网的DNC系统使车间乃至整个企业的信息网与DNC通信网络得以统一。达到全车间信息的完整性、通透性、一致性,而且可以直接将数控机床接人 [nternet,实现远程信息的传输,适应了网络制造的需要。由T-T.,_IIeVAX~已经成为工业现场控制发展的趋势,以此技术实现的数控机床网络控制系统性能可靠,易于在企业中推广莉应用,具有广阔的应用前景.
上一篇:以太网在继电器可靠性检测系统中的应用
下一篇:工业以太网交换机扎根电力应用
推荐阅读最新更新时间:2024-05-02 23:27
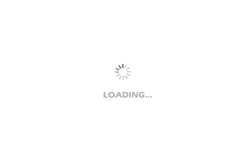
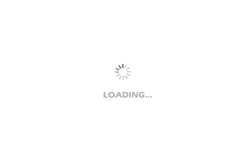
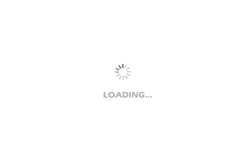
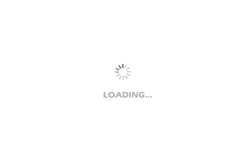
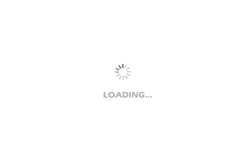
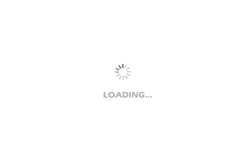