前言
长久以来显示应用一直是led发光组件主要诉求,并不要求LED高散热性,因此LED大多直接封装于传统树脂系基板,然而2000年以后随着LED高辉度化与高效率化发展,尤其是蓝光LED组件的发光效率获得大幅改善,液晶、家电、汽车等业者也开始积极检讨LED的适用性。
在此同时数字家电与平面显示器急速普及化,加上LED单体成本持续下降,使得LED的应用范围,以及有意愿采用LED的产业范围不断扩大,其中又以液晶面板厂商面临欧盟颁布的危害性物质限制指导(RoHS: Restriction of Hazardous Substances Directive)规范,因此陆续提出未来必需将水银系冷阴极灯管(CCFL:Cold Cathode Fluor-escent Lamp)全面无水银化的发展方针,其结果造成高功率LED的需求更加急迫。
技术上高功率LED封装后的商品,使用时散热对策成为非常棘手问题,在此背景下具备高成本效益,类似金属系基板等高散热封装基板的发展动向,成为LED高效率化之后另一个备受嘱目的焦点。
接着本文要介绍LED封装用金属系基板的发展动向,与陶瓷系封装基板的散热设计技术。
发展历程
图1是有关LED的应用领域发展变迁预测,如图2所示使用高功率LED时,LED产生的热量透过封装基板与冷却风扇排放至空气中。
以往LED的输出功率较小,可以使用传统FR4等玻璃环氧树脂封装基板,然而照明用高功率LED的发光效率只有20~30% ,而且芯片面积非常小,虽然整体消费电力非常低,不过单位面积的发热量却很大。
如上所述汽车、照明与一般民生业者已经开始积极检讨LED的适用性(图3),一般民生业者对高功率LED期待的特性分别是省电、高辉度、长使用寿命、高色再现性,这意味着高散热性是高功率LED封装基板不可欠缺的条件。
一般树脂基板的散热极限只支持0.5W以下的LED,超过0.5W以上的LED封装大多改用金属系与陶瓷系高散热基板,主要原因是基板的散热性对LED的寿命与性能有直接影响,因此封装基板成为设计高辉度LED商品应用时非常重要的组件。
金属系高散热基板又分成硬质(rigid)与可挠曲(flexible)系基板两种(图4) ,硬质系基板属于传统金属基板,金属基材的厚度通常大于1mm,硬质系基板广泛应用在LED灯具模块与照明模块,技术上它是与铝质基板同等级高热传导化的延伸,未来可望应用在高功率LED的封装。
可挠曲系基板的出现是为了满足汽车导航仪等中型LCD背光模块薄形化,以及高功率LED三次元封装要求的前提下,透过铝质基板薄板化赋予封装基板可挠曲特性,进而形成同时兼具高热传导性与可挠曲特性的高功率LED封装基板。
硬质系基板的特性
图5是硬质金属系封装基板的基本结构,它是利用传统树脂基板或是陶瓷基板,赋予高热传导性、加工性、电磁波遮蔽性、耐热冲击性等金属特性,构成新世代高功率LED封装基板。
如图所示它是利用环氧树脂系接着剂将铜箔黏贴在金属基材的表面,透过金属基材与绝缘层材质的组合变化,可以制成各种用途的LED封装基板。
高散热性是高功率LED封装用基板不可或缺的基本特性,因此上述金属系LED封装基板使用为铝与铜等材料,绝缘层大多使用充填高热传导性无机填充物(Filler)的填充物环氧树脂。
铝质基板是应用铝的高热传导性与轻量化特性制成高密度封装基板,目前已经应用在冷气空调的转换器(Inverter)、通讯设备的电源基板等领域,铝质基板同样适用于高功率LED的封装。
图6是各种金属系封装基板的特性比较,一般而言金属封装基板的等价热传导率标准大约是2W/m‧K,为满足客户4~6W/m‧K高功率化的需要,业者已经推出等价热传导率超过8W/m‧K的金属系封装基板。
由于硬质金属系封装基板主要目的是支持高功率LED的封装,因此各封装基板厂商正积极开发可以提高热传导率的技术。
硬质金属系封装基板的主要特征是高散热性。图7与图8是仿真分析LED芯片发热量为1W时,2W/m ‧K一般封装基板与8W/m‧K超高热传导封装基板正常使用状态下的温度分布特性。
由图8可知使用高热传导性绝缘层封装基板,可以大幅降低LED芯片的温度。此外基板的散热设计,透过散热膜片与封装基板的组合,还可望延长LED芯片的使用寿命。
金属系封装基板的缺点是基材的金属热膨胀系数非常大,类似低热膨胀系数陶瓷系芯片组件焊接时,容易受到热循环冲击,如果高功率LED的封装使用氮化铝时,金属系封装基板可能会发生不协调问题,因此必需设法吸收LED模块的各材料热膨胀系数差异造成的热应力,藉此缓和热应力提高封装基板的可靠性。
可挠曲系基板的特性
可挠曲基板的主要用途大多集中在布线用基板,以往高功率晶体管与IC等高发热组件几乎不使用可挠曲基板,最近几年液晶显示器为满足高辉度化需求,强烈要求可挠曲基板可以高密度设置高功率LED,然而LED的发热造成LED使用寿命降低,却成为非常棘手的技术课题,虽然利用铝板质补强板可以提高散热性,不过却有成本与组装性的限制,无法根本解决问题。
图9是高热传导挠曲基板的断面结构,它是在绝缘层黏贴金属箔,虽然基本结构则与传统挠曲基板完全相同,不过绝缘层采用软质环氧树脂充填高热传导性无机填充物的材料,具有与硬质金属系封装基板同等级8W/m‧K的热传导性,同时还兼具柔软可挠曲、高热传导特性与高可靠性(表1),此外可挠曲基板还可以依照客户需求,将单面单层面板设计成单面双层、双面双层结构。
高热传导挠曲基板的主要特征是可以设置高发热组件,并作三次元组装,亦即它可以发挥自由弯曲特性,进而获得高组装空间利用率。
图10是高热传导挠曲基板与传统聚亚酰胺(Polyi-mide)挠曲基板,设置1W高功率LED时的散热实验结果,聚亚酰胺基板的厚度为25μm,基板的散热采用自然对流方式。
根据实验结果显示使用高热传导挠曲基板时,LED的温度大约降低100℃,这意味着温度造成LED使用寿命降低的问题可望获得改善。
事实上除了高功率LED之外,高热传导挠曲基板还可以设置其它高功率半导体组件,适用于局促空间或是高密度封装等要求高散热等领域。
有关类似照明用LED模块的散热特性,单靠封装基板往往无法满足实际需求,因此基板周边材料的配合变得非常重要,例如图11的端缘发光型LED背光模块的新结构,配合~3W/m‧K的热传导性膜片,可以有效提高LED模块的散热性与LED模块的组装作业性。
陶瓷系封装基板
如上所述白光LED的发热随着投入电力强度的增加持续上升,LED芯片的温升会造成光输出降低,因此LED的封装结构与使用材料的检讨非常重要。
以往LED使用低热传导率树脂封装,被视为是影响散热特性的原因之一,因此最近几年逐渐改用高热传导陶瓷,或是设有金属板的树脂封装结构。LED芯片高功率化常用手法分别是:
●LED芯片大型化
●改善LED芯片的发光效率
●采用高取光效率的封装
●大电流化
虽然提高电流发光量会呈比例增加,不过LED芯片的发热量也会随着上升。图12是LED投入电流与放射照度量测结果,由图可知在高输入领域放射照度呈现饱和与衰减现象,这种现象主要是LED芯片发热所造成,因此LED芯片高功率化时首先必需解决散热问题。
LED的封装除了保护内部LED芯片之外,还兼具LED芯片与外部作电气连接、散热等功能。
LED的封装要求LED芯片产生的光线可以高效率取至外部,因此封装必需具备高强度、高绝缘性、高热传导性与高反射性,令人感到意外的是陶瓷几乎网罗上述所有特性。
表2是陶瓷的主要材料物性一览,除此之外陶瓷耐热性与耐光线劣化性也比树脂优秀。
传统高散热封装是将LED芯片设置在金属基板上周围再包覆树脂,然而这种封装方式的金属热膨胀系数与LED芯片差异非常大,当温度变化非常大或是封装作业不当时极易产生热歪斜(thermal strain;热剪应力),进而引发芯片瑕疵或是发光效率降低。
未来LED芯片面临大型化发展时,热歪斜问题势必变成无法忽视的困扰,有关这点具备接近LED芯片的热膨胀系数的陶瓷,可说是热歪斜对策非常有利的材料。
图13是高功率LED陶瓷封装的外观;图14是高功率LED陶瓷封装的基本结构,图14(b)的反射罩电镀银膜。它可以提高光照射率,图14(c)的陶瓷反射罩则与陶瓷基板呈一体结构。
散热设计
图15表示LED内部理想性热流扩散模式,图15右图的实线表示封装内部P~Q之间高热流扩散分布非常平坦,由于热流扩散至封装整体均匀流至封装基板,其结果使得LED芯片正下方的温度大幅降低。
图16是以封装材的热传导率表示热扩散性的差异,亦即图15表示正常状态时的温度分布,与单位面积单位时间流动的热流束分布特性。
使用高热传导材时,封装内部的温差会变小,此时热流不会呈局部性集中,LED芯片整体产生的热流呈放射状流至封装内部各角落,换言之高热传导材料可以提高LED封装内部的热扩散性。
LED封装用陶瓷材料分成氧化铝与氮化铝,氧化铝的热传导率是环氧树脂的55倍,氮化铝则是环氧树脂的55倍400倍,因此目前高功率LED封装用基板大多使用热传导率为200W/mK的铝质,或是热传导率为400W/mK的铜质金属封装基板。
半导体IC芯片的接合剂分别使用环氧系接合剂、玻璃、焊锡、金共晶合金等材料。LED芯片用接合剂除了上述高热传导性之外,基于接合时降低热应力等观点,还要求低温接合与低杨氏系数等等,符合这些条件的接合剂分别是环氧系接合剂充填银的环氧树脂,与金共晶合金系的Au-20%Sn。
接合剂的包覆面积与LED芯片的面积几乎相同,因此无法期待水平方向的热扩散,只能寄望于垂直方向的高热传导性。
图17是热传导差异对封装内部的温度分布,与热流束特性的模拟分析结果,封装基板使用氮化铝。根据仿真分析结果显示LED接合部的温差,热传导性非常优秀的Au-Sn比低散热性银充填环氧树脂接合剂更优秀。
有关LED封装基板的散热设计,大致分成:
●LED芯片至框体的热传导
●框体至外部的热传达
两大部位。热传导的改善几乎完全仰赖材料的进化,一般认为随着LED芯片大型化、大电流化、高功率化的发展,未来会加速金属与陶瓷封装取代传统树脂封装方式 。此外LED芯片接合部是妨害散热的原因之一,因此薄接合技术成为今后改善的课题。
提高LED高热排放至外部的热传达特性,以往大多使用冷却风扇与热交换器,由于噪音与设置空间等诸多限制,实际上包含消费者、下游系统应用厂商在内,都不希望使用强制性散热组件,这意味着非强制散热设计必需大幅增加框体与外部接触的面积,同时提高封装基板与框体的散热性。
具体对策例如高热传导铜层表面涂布“利用远红外线促进热放射的挠曲散热薄膜”等等,根据实验结果证实使用该挠曲散热薄膜的发热体散热效果,几乎与面积接近散热薄膜的冷却风扇相同,如果将挠曲散热薄膜黏贴在封装基板、框体,或是将涂抹层直接涂布在封装基板、框体,理论上还可以提高散热性。
有关高功率LED的封装结构,要求能够支持LED芯片磊晶接合的微细布线技术;有关材质的发展,虽然氮化铝已经高热传导化,不过高热传导与反射率的互动关系却成为另一个棘手问题,一般认为未来若能提高热传导率低于氮化铝的氧化铝的反射率,对高功率LED的封装材料具有正面帮助。
结语
以上介绍LED封装用金属系基板的发展动向,与陶瓷系封装基板的散热设计技术。随着LED大型化、大电流化、高功率化的发展,事实上单靠封装基板单体并无法达成预期的散热效,必需配合封装基板周边的散热材料,以及LED封装结构才能进行有效的散热。因此未来必需持续开发周边相关技术,LED才能够实现次世代光源的终极目标。
上一篇: LED背光源特点介绍
下一篇:分析:高辉度4元系LED芯片技术与制作方法
推荐阅读最新更新时间:2023-10-18 16:00
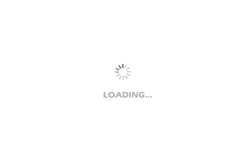
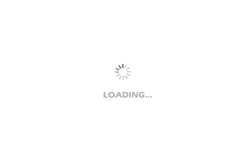
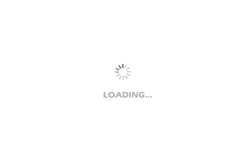
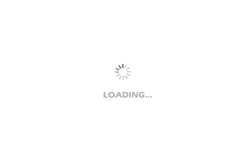
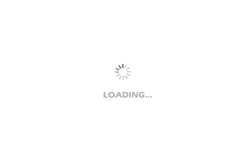
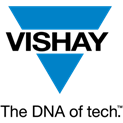
Vishay线上图书馆
- 选型-汽车级表面贴装和通孔超快整流器
- 你知道吗?DC-LINK电容在高湿条件下具有高度稳定性
- microBUCK和microBRICK直流/直流稳压器解决方案
- SOP-4小型封装光伏MOSFET驱动器VOMDA1271
- 使用薄膜、大功率、背接触式电阻的优势
- SQJQ140E车规级N沟道40V MOSFET

- 宁德时代巧克力换电生态大会将举行,什么是“巧克力换电”?1.5分钟换电能实现吗?
- 新型生物材料与高端医疗器械广东研究院、远诺技术转移中心加入面向初创企业的 MathWorks
- S5PV210 Linux字符驱动之PWM蜂鸣器驱动
- 尼得科机床新增可实现高效加工的高速主轴产品线
- Gartner发布2025年影响基础设施和运营的重要趋势
- 智谱清言英特尔酷睿Ultra专享版发布,离线模型玩转AIPC
- Bourns推出全新高效能、超紧凑型气体放电管 (GDT) 浪涌保护解决方案
- S5PV210之UBOOT-2011.06启动过程解析
- 六个理由告诉您为什么应该将模拟无线麦克风更换为数字无线麦克风
- S5PV210启动过程分析