投资规模越来越大,工艺要求越来越高,产品可靠性越来越受重视,现代电子组装业正发生着巨大的变化。在此基础上,对于生产检测设备的要求也越来越高。
自动X射线检测无疑是一个重要的检测技术发展方向,能满足高品质、高密度、小型化、高效率和大批量的电子产品生产要求。
目前,国内自主研发的微焦斑X射线检测设备,能满足多种复杂工艺的检测要求和图像处理需求,且设备性能高、成本低。针对不同应用设计不同的检测方案,AXI为电子制造企业达到提高“一次通过率”和“零缺陷”的目标,提供了一种有效的检测手段。
图为日联科技检测设备生产车间
新兴检测技术兴起
AXI是对ICT、AOI检测能力不足的有力补充,不仅可对不可见焊点进行检测,还可对检测结果定性、定量分析,以便及早发现故障。
随着电子技术的飞速发展,封装的小
型化、组装的高密度化以及各种新型封装技术不断涌现,电子组装对质量的要求也越来越高,基于此,对于生产检测技术也提出了更高的要求。为满足这一要求,新的检测技术不断出现,其中,自动X射线检测技术是目前新兴检测技术中的典型代表。
AXI是对ICT、AOI检测能力不足的有力补充,具有不可替代性,它不仅可对不可见焊点进行检测,还可对检测结果定性、定量分析,以便及早发现故障。通过使用AXI,可以使电子产品的检测能力得到较高的提升。
可以说,AXI为达到提高“一次通过率”和“零缺陷”的目标提供了一种有效的检测手段。”
AXI检测原理是在组装好的线路板(PCBA)沿导轨进入机器内部后,位于线路板上方的X射线发射管发射出的X射线穿过线路板,被置于下方的探测器接收,由于焊点中含有可以大量吸收X射线的铅,因此与穿过玻璃纤维、铜、硅等其他材料的X射线相比,照射在焊点上的X射线会被大量吸收,在输出图像中显示黑点,从而实现自动可靠的焊点缺陷检测。
目前X射线无损检测技术大致可以分为三大类:基于2D图像的X射线检测分析技术;基于2D图像,具有最高放大倍数的倾斜视图的X射线检测分析技术;3DX射线检测分析技术。前两种属于直射式光学检测技术,后一种属于断层刨面X光检测技术。
目前看来,相比其他类型的检测技术,AXI检测技术具备以下特点:
一是对工艺缺陷的覆盖率高达97%。可检测的缺陷包括虚焊、桥连、立碑、焊料不足、气孔、器件漏装、平整度等,尤其是X射线对BGA、CSP等焊点隐藏器件也可以进行检查;
二是较高的测试覆盖度,可以对肉眼和在线检测不到的地方进行检测。比如PCBA被判断故障时,怀疑是PCB内层走线断裂,X射线可以很快地进行检查;
三是检测的准备时间大大缩短;
四是能观察到其他测试手段无法可靠探测到的缺陷,比如虚焊、空气孔和成像不良等;
五是对双面板和多层板只需一次检测(带分层功能);
六是提供相关测量信息,如焊膏厚度、焊点下的焊锡量等,这些信息可用来对生产工艺过程进行评估。
据悉,目前AXI检测技术已被广泛应用于锂电池、半导体、太阳能光伏、集成电路、电子制造业、PCB、LED、压铸件等行业的产品检测。
国产检测设备发力
集成电路的三维封装非常复杂,相关检测问题让众多厂商头疼不已,国内自主研发的X射线检测设备解决了这一难题。
由于集成电路的三维封装非常复杂,在器件组装、测试和随后安装到印刷电路板的过程中,对封装的检验和质量控制工艺的鉴定提出了独特的挑战,这也成为了众多国内检测设备厂商最为头疼的问题之一。
目前,由日联科技联合华南理工大学、中科院等一线科研院所研发的X射线3D封装缺陷离线检测设备克服了二维X射线成像技术的局限性。据了解,X-射线3D封装缺陷离线检测设备采用小于1μ以下开放式纳米级X射线管,结合全方位3D扫描断层图像,重构极大规模集成电路芯片,形成3D图像处理软件。
根据3D图像和工艺要求,综合应用光学、控制、信息等多学科知识,解决了约束空间的光路设计、自适应光源控制、图像处理专用软件算法、高速图像处理机研制等技术难题,将视觉检测算法和技术应用于BGA、CSP等高端芯片焊点隐藏器件的虚焊、桥连、立碑、焊料不足、气孔等缺陷检测,可满足不同产品检测的要求。
同时,通过采用基于视觉伺服物像点追踪技术、基于电机驱动性能最大化的运动规划、补偿控制及振动控制算法以及可靠性技术,日联科技研发出具有高速、高精度、高可靠性的运动控制平台,可解决3D检测设备中物像点追踪、高速高精运动控制平台等难点问题。
相关设备专家表示,日联科技的X射线检测设备设计思路先进、结构紧凑,自主研发的控制软件与多功能图像处理软件符合人机工程学特点,控制软件操作简单、保护安全可靠,拥有自主知识产权,填补了国内电子制造领域同类检测设备的研制空白。
该设备填补国内空白,源于日联科技多年来的积累。成立10多年来,日联科技一直致力于自动化电子制造高端设备的研发、制造、销售与服务,通过紧密跟踪电子行业发展动向,抓住电子制造服务业的发展机遇,不断研制推出新产品,适应市场发展需要。
随着公司在技术上取得巨大突破,产品的应用领域也从原来单一的电子制造业领域扩展到现有的锂电池行业、LED行业、太阳能光伏行业、半导体封装、汽车零配件等多个行业,能实时和离线有效检测出电路板组件的桥连、空洞、虚焊及少锡等问题,完成LED和半导体封装焊接的气泡测试,查看电池/电容的电芯绕卷情况和电池极片极耳的平整度等常见缺陷状况。
据了解,下一步,日联科技将继续加强与知名高等院校研究所的合作研究,响应产业发展的需求,进一步致力于精密X射线核心部件的基础研发,填补国内在微焦斑成像技术中的空白。
同时,将加紧微焦斑国家标准、行业标准的制定以及自有知识产权的保护工作,力争在该领域形成自有品牌。
市场应用前景看好
只有通过对生产过程中工业可靠性和结构性缺陷的检测,使产品规范地进入市场,才能有效推动产业的健康、有序发展。
在电子制造业领域,微聚焦X光成像技术是EMS行业中不可或缺的技术之一,几乎每家从事PCBA电子制造和半导体封装相关产业的电子公司都要用到微聚焦的X光成像技术,来帮助企业做好来料质量控制、制程分析、产品可靠性判定,同时可应用于企业内部技术研发方面。
在向中国转移的过程中,电子制造产业得到了飞速发展,囊括个人消费电子产品、计算机行业、通信行业以及诸多新兴产业,几乎涵盖到电子类产品的整个市场领域。在国家对个人电子消费品、通信、LED、太阳能光伏等产业的强力政策推动下。
我国电子信息制造业抓住国家经济社会发展和国际产业转移的重大机遇,积极推进结构调整,着力加强自主创新,实现了产业的稳步增长,对经济社会发展的支撑引领作用日益凸显。
随着电子制造产业的发展,目前我国已有将近20000家SMT企业活跃于该产业,但是由
于X射线设备昂贵且不是生产设备,只有约1/3的工厂使用X射线检测设备,其中跨国公司基本都使用价格非常昂贵的国际品牌。
随着现在电子产品便携式及小型化的发展趋势,元器件越来越小,线路板组装的密集程度也越来越高,生产加工的难度更是越来越大,因此品质保障就显得更为重要,各生产厂商也纷纷加大了购置检测设备的资金投入力度。相关数据显示,2013~2015年,每年将至少有2000~5000台的国内市场份额。
PCB产业的产品检测问题也日益凸显。目前,全球PCB产业产值占电子元件产业总产值的四分之一以上,是各个电子元件细分产业中比重最大的产业,在中国成为电子产品制造大国的同时,全球PCB产能也在向中国转移。
不仅内资PCB制造企业加速扩大产能,外资企业也同时加速向中国转移、新增产能,国内PCB行业投资始终火热。
据了解,从2006年开始,中国就超过日本成为全球第一大PCB制造基地。2012年,全球PCB产业销售额约603亿美元,中国占41%。预计到2015年,中国大陆PCB总产能可达到309亿美元,占全球比例上升至44.3%。目前,中国大陆地区逐渐形成了珠三角地区、长三角地区为核心区域PCB产业聚集带。
但是,一个不可忽视的事实是,中国虽然已成为全球PCB产业毋庸置疑的大国,却由于未形成完整的产业链条,造成了中国PCB产业大而不强的困境。中国PCB产量产值全球第一,企业数量也全球最多,但是生产所需的设备、仪器和原辅材料等关键配套产业均发展不足。
虽然中低档设备已经可以替代进口,但是高端设备、检测仪器,一直为国外垄断,自给率较低。大力发展PCB配套行业,将成为未来中国PCB产业发展的重点。
对于锂电池、半导体、LED照明等战略性新兴产业来说,巨大的市场机会也有待检测设备的支撑。
“十二五”期间,国家明确将新材料作为高技术产业工程重大专项。国务院发布的《关于加快培育和发展战略性新兴产业的决定》中,明确提出大力发展锂电池、LED照明材料等战略性新兴材料产业。
据悉,锂电池包括小型锂电池和动力锂电池,主要应用于笔记本电脑、手机、电动自行车、电动汽车、备用电源、航空航天、军事、医疗等。随着技术的不断进步,锂电池更是已经在人们的生活中得到了广泛的应用,如便携式电子产品、新能源交通工具及储能等领域。
据IDC预测,笔记本电脑2013年的全球出货量将从2009年的1.652亿台增长到3.125亿台。
在动力锂电池方面,电动汽车将是未来的发展方向。全球电动汽车规模将在2015年扩大至120万辆。到2020年,国内纯电动汽车保有量将达到400万辆,混合动力汽车将达到1800万辆。
以新能源汽车带动锂电池需求应用来分析,从2010年开始,汽车制造商开始大幅提高锂电池作为动力源的比例,2010~2013年是锂电池动力汽车的快速成长期,预计2013年内将达到226万辆,2013年以后将进入稳步发展阶段,2015年达到近371万辆。新能源汽车的快速发展带动了锂电池需求的快速增长,其占比将由2009年的1.88%快速跃升至2015年的58.74%。
作为半导体产业的两大分支之一,分立器件是电子工业的支撑产业,是电子工业发展的基础。随着产业的不断发展,一些新技术、新工艺、新产品不断涌现,推动着分立器件市场的蓬勃发展。
随着近年来国际半导体制造业向中国大陆的快速转移,中国已成为全球最具发展潜力的半导体制造基地和繁荣的销售市场,其中手机、笔记本和数码相机已经占据全球50%以上的份额。
目前看来,分立半导体器件的发展趋势是:
首先,新型半导体分立器件将不断呈现,在替代原有市场应用的同时,还将开拓出新的应用领域;
其次,为了使现有半导体分立器件能适应市场需求的快速变化,将采用新技术,不断改进材料、结构设计、制造工艺和封装等,提高器件的性能;
最后,电子信息系统的小型化甚至微型化,必然要求其包括半导体分立器件在内的各部分尽可能小型化、微型化、多功能模块化、集成化。
国务院《“十二五”节能环保产业发展规划》中提出,提高产业集中度,实现LED照明技术与装备产业化,建成一批产业链完善、创新能力强、特色鲜明的LED照明新兴产业集聚区。到2015年,LED产业产值达到4500亿元,形成具有国际竞争力的LED产业。
未来5年将是LED照明从研发和示范阶段向完全市场化阶段过渡的关键时期,LED产业必将成为推动我国经济发展的绿色经济产业。到2015年,LED芯片国产化率将达70%,产业规模达到5000亿元,相关企业面临着巨大商机,中国LED照明即将迎来市场的蓬勃发展期。
面对锂电池、半导体、LED照明产业巨大的市场潜能,目前国际、国内相关生产检测手段却仍不完善甚至缺失,这严重影响着市场的规范和企业的发展。
当下,对生产过程中工艺可靠性不足以及结构性缺陷的检测愈发重要,对产品的标准化、安全性以及循环使用的要求更是直接决定了产品的质量。业内认为,只有通过对生产过程中工业可靠性和结构性缺陷的检测,使产品规范地进入市场,才能有效推动产业的健康、有序发展。
微焦斑X射线检测技术为生产检测手段带来了新的变革,可以说它是目前渴望进一步提高生产工艺水平和生产质量,并及时发现设备故障的生产厂家的解决生产检测问题的极佳选择。
以锂电池为例,微焦斑X射线可以有效对各类电池内部电极结合部位的联结状况进行实时检查,查看电池正负极绕片对齐状况以及电芯组装内部情况等,规范其整个工艺过程。
上一篇:LED照明助力绿色机场起航
下一篇:高功率DurisS LED系列多晶片处于“温床期”
推荐阅读最新更新时间:2023-10-12 22:26
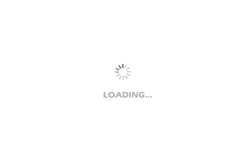
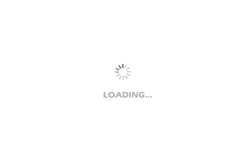
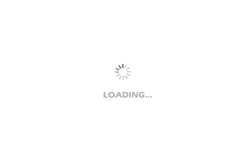
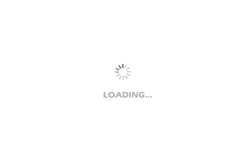
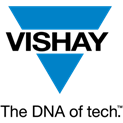
Vishay线上图书馆
- 选型-汽车级表面贴装和通孔超快整流器
- 你知道吗?DC-LINK电容在高湿条件下具有高度稳定性
- microBUCK和microBRICK直流/直流稳压器解决方案
- SOP-4小型封装光伏MOSFET驱动器VOMDA1271
- 使用薄膜、大功率、背接触式电阻的优势
- SQJQ140E车规级N沟道40V MOSFET

- 英飞凌推出符合ASIL-D标准的新型汽车制动系统和电动助力转向系统三相栅极驱动器 IC
- 南芯科技推出80V升降压转换器,持续深耕工业储能市场
- 法雷奥与罗姆联合开发新一代功率电子领域
- 贸泽电子开售能为电动汽车牵引逆变器提供可扩展性能的 英飞凌HybridPACK Drive G2模块
- Vishay推出采用eSMP®系列SMF(DO-219AB)封装的全新1 A和2 A Gen 7 1200 V FRED Pt®超快恢复整流器
- Littelfuse推出高性能超级结X4-Class 200V功率MOSFET
- 恩智浦发布首个超宽带无线电池管理系统解决方案
- 非常见问题解答第223期:如何在没有软启动方程的情况下测量和确定软启动时序?
- Vicor高性能电源模块助力低空航空电子设备和 EVTOL的发展