升压电源常用于将低压输入转换成较高电压。不过,随着这些电源的功率需求不断增加,单个功率级可能变得缺乏吸引力。本文将介绍一种交错式升压技术,无论从分析还是从实际应用经验上来说,该技术在效率、尺寸及成本方面均优于单升压转换器(single-boost converter)。本文对250W单相电源与交错式升压电源的测试结果进行了对比。尽管复杂性有所增加,不过交错式升压却表现出具有卓越的性能。
前言
本文将以输入电压为12 V、输出为7 A、37 V的喷墨打印机电磁线圈驱动器为例介绍电源结构的选择。该电源的输入电流超过20 A.最初我们并不清楚单相功率级合理,还是多相功率级合理。与采用降压稳压器一样,我们可以获得足够高的电流,从而采用双功率级来降低应力并进行散热。在此情况下,我们考虑采用了单相与双相升压结构(two-phase boost topology)。
表1说明了相应的电源需求。这个电源必须能够承受电磁线圈启动和关闭时出现的大电流突波,并将所需输出电压保持在可以接受的范围内。另外,转换效率对于最小化功率耗损和维持正常温升同样至关重要。37V和
7A代表超过250W的负载功率。就算转换效率达到91%,电源仍然会浪费25W的功率,因此需要安装多个散热片。此外,尽管本文并未特别说明,但是电源的大小与成本也相当重要。
图1显示了两种电源的对比。上面的电源是采用单输入电感的单相设计,而下面的电路是双相设计。单相设计(上面部分)需要的PWB面积大约为18平方英寸,而交错式设计(下面部分)需要14平方英寸。两种方案之间最大的面积差异在于电感、输出电容和散热片。交错式电感的最大高度低于单相设计的最大高度。
单相与双相对比
图2显示了单相升压转换器和交错式升压转换器的示意图。在单相设计中,闸极电压会施加在FET Q1,以下拉漏极至接地电位。这样可以在电感L1上施加输入电压,使电流上升。其间,输出电容C2必须单独提供负载所需电流。在Q1停止导通时,L1为了维持电流,其两端的电压极性会立刻反转。使得切换点的电压高于输入电压,此时二极管D1进入正向偏置状态,为输出电容C2充电并提供输出负载电流。电感的伏特-微秒乘积在这两种开关状态下必须保持平衡,即d / fs×Vin = (1 - d) / fs×(Vout - Vin),得出关系式Vout = Vin / (1-d)。该公式只适用于连续导通模式(CCM),该模式的定义为电感电流始终保持正极。
图2所示的交错式升压电路中,每个相的工作方式都与上述单相升压相似。两个功率级会以反相180.的方式运行,使得输入和输出电容的纹波电流互相抵消。交错式升压设计会强迫两个功率级共同提供输出电流,使得电源输出由它们平均分担;如果工程师不采用这种设计,其中一个功率级的电流输出就会远大于另一个功率级,使得原有的纹波消除优点化为乌有。
设计分析
图3说明了交错式技术提供的输入电容纹波电流消除优势。可以看出,两个以180.相位差工作的功率级可以消除一半峰/峰纹波电流。由于交错式升压设计的组合输入纹波电流等于单相输入纹波电流,因此双相设计的单相纹波电流可以达到单相设计的两倍。单独交错式功率级以与单相设计相同的频率工作,即100KHz.但是,由于纹波消除作用,它的有效输入与输出纹波变为200KHz.因此在计算交错式设计的电感时,适用的频率虽和单相设计完全相同,但能允许的纹波电流却会增加一倍,使得设计所需的电感值得以减少一半。值得注意的是:在双相设计中,输入电容的有效纹波电流与单相设计相同,因此这两种设计会采用相同数量的输入电容。纹波消除作用能够使工程师有选择性地减少组件,从而使设计受益。另外,如果采用的两个电感与单相设计采用的电感值相同,输入电容需求可以降低50%。在升压设计中,电感需求一般比输入电容需求更重要。
就像输入电容一样,交错式设计的输入电容也能享受同样的好处。图4说明的是单相设计的输出电容纹波电流。图3中电流波形的均方值约为Ipp×√(d×(1-d)),在本设计中等于10Arm.电感的斜率可以从波形顶部看出,但是它并不显著增加总的RMS电流。在FET导通时,该电容提供所有的输出电流。不过,当FET截止时,会有相当于Iout×d/(1-d)或+14A的电流流入电容,并对它重新充电。在采用铝电解输出电容的情况下,电容纹波电流额定值决定所需要的电容数量。
图5是交错式升压设计中,个别输出电容的电流值及它们的总和。在不考虑电感斜率的情况下,相位A与相位B的峰/峰电流幅值是单相设计的一半。这是因为流入输出电容的电流的占空比是单相设计的两倍。在图5中,综合电流或总电流的均方根值是5Arm,因此设计只需采用一半输出电容,即可让纹波电压达到与单相设计相同的纹波电压。
图6是不同占空比下的纹波电流消除。垂直线表示工作占空比,从中可以看出在此占空比下,交错式升压设计的RMS电流等于单相位设计的一半。值得注意的是,50%的占空比可以提供完全消除的效果。
图7与图8说明单相与交错式升压转换器的完整设计。在单相设计中,在电压模式下工作的UCC38C43驱动一对MOSFET.由于在升压转换器短路情况下无法限制输出电流,因此采用了带有过电流保护电路的TPS2490热插拔器件。在测试过程中发现,在过电流故障情况下它可以提供一种“中止”电流流动的方法。
图8说明采用UCC38220控制器的交错式设计。利用Q5与Q7漏极引线中的小型低成本电流互感器感测FET电流。UCC28220迫使相位之间实现相等的电流共享。降低整流器的电流可以消除对散热片的需求并且降低组装成本。
试验结果
这两种设计在效率、输入与输出纹波电压以及瞬态负载方面的对比结果显示,在大部分情况下,双相设计的性能都优于单相设计。
图9对比两种方法的效率。它们都能够满足91%的目标效率。不过,双相设计在满负载情况下的效率高两个百分点。虽然这看起来可能并不明显,但是若比较两种电源的损耗差异,就会发现其中差别很大。单相设计消耗23 W,而双相设计仅消耗16 W.这相当于热损耗降低30%,因而必将对散热片的选择与热功耗设计产生一定影响。
单相曲线很快达到最高值,然后开始迅速下降。这是传导损耗较高的设计的特性。两种设计的明显差异体现在电感、升压二极管、输出电容与PWB的损耗。表2对比了电感需求与设计性能。如前所述,双相方法采用的电感比单相设计低得多,而且每个电感仅承载一半的电流。电感的体积取决于蓄能需求与温度的升幅。蓄能大小由(1/2×L×I2)决定,而表2说明单相设计的蓄能是双相设计的5倍。这意味着,如果我们要使电感的温度升幅保持相同,则单相设计的电感应当大5倍。我们认为与其保持相等的能量密度,不如允许较大的温度升幅。我们在单相设计中使用损耗较大的电感因而牺牲了部分效率。结果,单相设计的损耗高出了近5 W.在这两种设计的功耗差异中,输出电容大约占1 W.每个输出电容的纹波电流造成大约100 mW的损耗,而且单相设计需要的电容比双相设计多出6个。双相设计的功率级必须采用两个二极管,每个二极管承担总电流的一半。这样它们具有较低的压降,可使总功耗降低大约1W.
小结
与降压稳压器一样,交错式升压设计的性能也优于单相设计。从表3中完整的单相升压设计与交错式升压设计的对比即可看出。交错式升压设计体积更小,效率更高。这是因为它能减少输出纹波电流,使得输出电容数量显著降低,从而降低了成本与功耗;它还能减少电感的蓄能要求,这表示电感磁线圈的体积、高度与热损耗都会降低。多相方法可使总功耗降低 30%,同时将热量分散至较大电路板面积,从而实现更完美的热管理。多相设计必须测量与平衡每个相位的电流大小,因此它确实会增加电路的复杂性,这从可控制组件的数量就能看出。
上一篇:高频小信号LC 谐振放大器的设计
下一篇:模拟前端(AFE)原理及选型指南
推荐阅读最新更新时间:2023-10-12 22:23
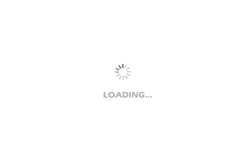
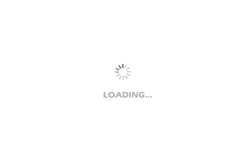
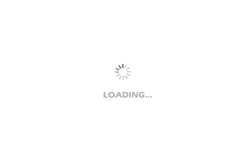
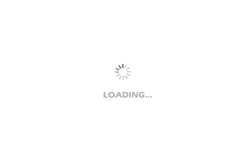
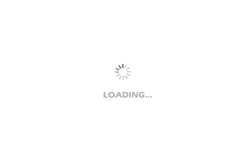
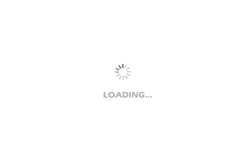
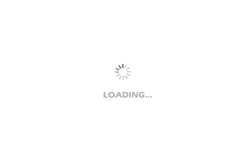
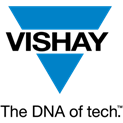
Vishay线上图书馆
- 选型-汽车级表面贴装和通孔超快整流器
- 你知道吗?DC-LINK电容在高湿条件下具有高度稳定性
- microBUCK和microBRICK直流/直流稳压器解决方案
- SOP-4小型封装光伏MOSFET驱动器VOMDA1271
- 使用薄膜、大功率、背接触式电阻的优势
- SQJQ140E车规级N沟道40V MOSFET

- 英飞凌推出符合ASIL-D标准的新型汽车制动系统和电动助力转向系统三相栅极驱动器 IC
- 南芯科技推出80V升降压转换器,持续深耕工业储能市场
- 法雷奥与罗姆联合开发新一代功率电子领域
- 贸泽电子开售能为电动汽车牵引逆变器提供可扩展性能的 英飞凌HybridPACK Drive G2模块
- Vishay推出采用eSMP®系列SMF(DO-219AB)封装的全新1 A和2 A Gen 7 1200 V FRED Pt®超快恢复整流器
- Littelfuse推出高性能超级结X4-Class 200V功率MOSFET
- 恩智浦发布首个超宽带无线电池管理系统解决方案
- 非常见问题解答第223期:如何在没有软启动方程的情况下测量和确定软启动时序?
- Vicor高性能电源模块助力低空航空电子设备和 EVTOL的发展