1 引言
量热计是目前最准确的功率测量方法,在量热计的设计中,整体结构温度稳定度是实现准确测试的充要条件,但在40GHz以下的频率范围之内,由于波导的体积较大,造成量热计整体的体积增大,热容增高。为了保证波导传输线的传输以及隔热效果,采用了与桶盖连接热分布均匀的热容传输线和保证热量不向外扩散的隔热传输线的多波导连接方式,提高了结构的复杂程度,为温度控制的准确性造成了一定的难度。本文在解决量热计量热体以及整体热力学结构设计与仿真的基础上,采用模糊PID控温技术,实现了控温精度达到5%摄氏度的技术指标,具有一定的实际意义。
2 量热计的组成及原理:
作为功率标准的量热计通常采用双负载结构。如图5所示,在双负载量热计中,将两个热学条件完全相同的量热体A和B置于隔热容器中。其中,量热体A用来加被测得高频功率或直流替代功率,另一个量热体B不加任何功率,仅仅作为量热体A的温度参考。当量热体A加上恒定的功率时,量热体A和B之间将产生一个恒定的温差。装在量热体A和B之间的热电堆将检测出温差电动势。假定高频功率和直流功率在同一个量热体上有相同的热效应,则可以用高频-直流替代的方法测量高频功率。
图1 量热计模型
3 负载的结构设计以及热力学仿真
3.1 负载的理论分析
低功率波导式匹配负载由一段终端短路的波导和安装在波导中的吸收体组成的。为了获得较大的衰减,要求吸收材料具有低的电导率和高的磁导率,在热学特性方面,由于吸收体材料多由绝缘材料组成,其热传递特性远远小于金属材料,吸收体的体积,表面积,材料加工的粗糙程度都会影响到微波能量的吸收以及吸收体与波导壁之间的热传递,所以量热计负载的设计对负载吸收体的形状、材料、表面粗糙度、加工精度,都有很高的要求。
由上一节量热计的工作原理可知,波导负载在量热计中主要起到了量热体的作用,即要求其在吸收大部分微波功率的情况下,整个负载的温升与直流加热下的负载温升有一定量的关系,并要求波导负载的微波—直流功率替代效率尽可能的高,所以在设计中,不仅要考虑负载的微波特性,更要考虑负载的热学特性。
根据量热计的基本工作原理,我们可知,在微波负载上存在的热传递过程是:
1)吸收功率过程中,热传递过程为:
图2 吸收微波功率热传递过程
2)加热电阻工作过程中,热传递过程为:
图3 吸收直流功率热传递过程
根据以上热传递过程分析,在整个过程中,主要存在的热交换为传导换热和辐射换热,在重力引起的空气对流情况下,总热流通量等于传导热流通量和辐射热流通量之和。
3.2 片式吸收体负载设计及热力学仿真
此种结构为波导外壁尖劈状,内部单面贴覆碳化硅吸收片,该结构热学性能高于第一种,因为吸收体材料用料较第一种形式少,整体厚度小,其吸收的微波能量在很短时间内就将传输到波导外壁,其平衡时间缩短,并且直流加热源与吸收材料贴敷波导宽壁同侧,其直流源与微波源加热效率非常高,在查阅的技术文献资料中提到可达到90%以上,但是此种结构负载对加工精度要求很高,对吸收体材料也有很高的硬度以及强度要求。
下面为针对这种思路的负载结构和电磁场和热学仿真结果:
(1)电磁场仿真分析
负载结构如图4所示:
图4 8mm波导负载设计图
仿真驻波结果如图5所示:
图5 8mm负载驻波仿真图
(2)波导负载热学仿真如下:
仿真环境为吸收体圆锥均匀分布10mW功率,稳定状态下整个8mm波导负载的温度分布情况,可以看出:其温度最高位置比不加入功率相应位置温度升高0.14摄氏度左右.
环境温度35摄氏度,负载不加入任何功率情况下表面的温度分布如图6:
图6 恒温条件下负载温度分布
环境温度35摄氏度,负载表面均匀分布10mW功率,负载表面温度分布如图7:
图7 加热条件下负载温度分布
3.3 片式吸收体负载测试结果
图8、9为负载加工图以及驻波测试图,其驻波均在1.12以下,高频部分驻波优于低频部分,其微波特性满足使用要求。加热功率在10mW情况下温升在0.1K左右,其直流与微波替代效率可达到80%以上,负载设计满足量热计整体需求。
图8 8mm负载实际加工图
图9 8mm负载实测驻波结果图
4 量热计的结构设计以及热力学仿真
4.1 量热计的结构设计
由于量热计法测量微波功率是建立在直流功率通过在负载上的热效应来替代微波功率,所以这种测量方法就对量热计整体结构的温度稳定性提出了非常高的要求。在量热计结构的初步设计中,我们采用了双负载量热计结构。在控温精度要求方面整体结构采用了三层桶的结构,外层为薄壁铝制圆筒,中间为大质量大热容铜制控温筒,内层为铜制内桶,铜制控温桶表面贴敷加热电阻膜,并通过贴敷在该桶表面的测温电阻温度的变化量由控温设备控制加热功率的大小以实现其表面温度稳定度达到0.05摄氏度以内。薄壁外层铝桶与外层铜制控温桶之间的变化量由控温设备控制加热功率的大小, 填充泡沫塑料,用以减小整体与外界的热交换。
功率输入端口采用不锈钢制薄壁波导,该设计得主要目的是减少整段波导传输线的热量损耗。内外铜桶之间采用塑料质地的隔热波导段,其波导连接表面与波导腔内壁镀金,采用原因是因为热容传输线质量较大,而不锈钢薄壁波导其承载荷较低,容易发生损坏。在负载与内桶盖热容传输线与外桶盖热容传输线间采用不锈钢薄壁波导隔热传输线,保证内桶的热量交换不受环境的影响和准确测温的要求。
微波传输通道结构如图10所示。
图10 微波信号传输通道示意图
4.2 量热计结构的热力学分析。
量热计内外铜桶的热力学结构仿真结果如图11所示:
图11 控温桶热学仿真图
该热力学仿真所处的仿真环境为:铜制外桶表面温度35摄氏度衡定,由热力学分布图可知其内桶内部温度比较稳定,在热容传输线与非金属隔热波导段之间略有温度损耗,但对整体的温度稳定性影响并不是很大,所以从仿真结构来看量热计热力学结构设计基本符合要求。
4.3 量热计的控温技术研究。
在设计中,考虑到自身的控温要求与环境以及成本,我们确定了采用外层填充泡沫塑料,多层桶结构,外表面控温的基本方案。并在控温技术中采用了模糊PID控制技术。
(1)模糊PID控温技术简介
在量热计控温系统中,我们采用了模糊PID控制系统,控制系统结构如图12所示:
图12 控温系统结构图
PID温度控制器的控制规律为:
由于系统中模糊控制器是实施运行的,所以要求解模糊器的计算要相对简单,不在此处进行讨论。
(2)实际控温实验结果
控温数据采集时间设定为10个小时,从初始加热开始采集,目标控温温度为22.000摄氏度,图13、14为控温数据图,由图可以看出,升温开始到温度基本稳定需要5-6个小时,而温度变化量小于千分之五摄氏度则需要8小时左右,由图13、14数据,控温指标基本达标,满足系统进行进一步定标实验的要求。
图13 控温数据图(整个控温过程10小时)
图14 控温数据图(温度基本稳定)
5 结论
由以上分析,文中所设计的量热计用负载以及整体恒温结构基本满足项目要求,但是量热计的设计是一个复杂而反复的过程,通过数值计算及软件仿真所得到的结论经实验验证之后,需要进一步的优化设计用以得到更加精确的试验数据以满足量热计对实验结果的准确要求。
上一篇:三种电源控制拓扑的优劣
下一篇:225MHz~512MHz 50W功率放大器研制
推荐阅读最新更新时间:2023-10-12 22:43
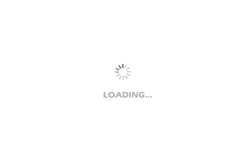
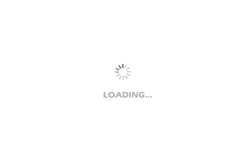
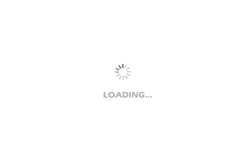
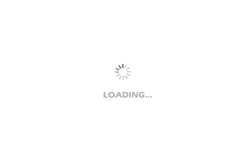
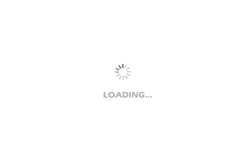
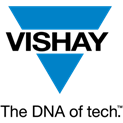
Vishay线上图书馆
- 选型-汽车级表面贴装和通孔超快整流器
- 你知道吗?DC-LINK电容在高湿条件下具有高度稳定性
- microBUCK和microBRICK直流/直流稳压器解决方案
- SOP-4小型封装光伏MOSFET驱动器VOMDA1271
- 使用薄膜、大功率、背接触式电阻的优势
- SQJQ140E车规级N沟道40V MOSFET

- Bourns 推出两款厚膜电阻系列,具备高功率耗散能力, 采用紧凑型 TO-220 和 DPAK 封装设计
- Bourns 全新高脉冲制动电阻系列问世,展现卓越能量消散能力
- Nexperia推出新款120 V/4 A半桥栅极驱动器,进一步提高工业和汽车应用的鲁棒性和效率
- 英飞凌推出高效率、高功率密度的新一代氮化镓功率分立器件
- Vishay 新款150 V MOSFET具备业界领先的功率损耗性能
- 强茂SGT MOSFET第一代系列:创新槽沟技术 车规级60 V N通道 突破车用电子的高效表现
- 面向车载应用的 DC/DC 电源
- Vishay推出适用于恶劣环境的紧凑型密封式SMD微调电阻器
- MathWorks 和 NXP 合作推出用于电池管理系统的 Model-Based Design Toolbox