根据模型参考自适应控制(MRAC)思想,建立了数控机床切削加工过程MRAC模型,然后对模型进行动力学过程仿真。同时,分别对加工过程的反馈闭环控制和开环控制进行仿真,并将这3种仿真结果进行比较,从仿真结果可以看出,MRAC的机床切削加工性能指标最好。
1 数控机床MRAC的工作原理
数控机床的MRAC是以机床、刀具、工件系统所完成的切削过程作为调节对象。该控制系统的原理结构如图1所示。它除了一般数控机床的位置和速度控制回路以外,还增加了MRAC反馈回路。当系统受到各种随机因素的干扰后,切削过程的状态参数立刻发生变化,通过传感器随时检测这些参数的数值并经转换,在MRAC控制单元中与给定的评价指标或约束条件(即期望的性能指标)进行判别和比较,得到性能指标偏差,然后给主机CNC输出校正信号,对系统的输人参数进行修正,从而使切削过程向预定的指标和条件转变,以达到最佳状态。
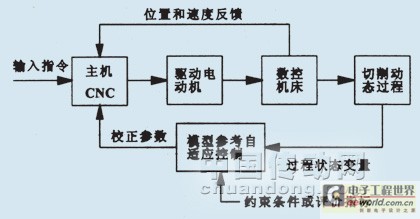
图1 数控机床MRAC系统结构
2 机床切削加工MRAC模型的建立
机床切削加工过程MRAC模型如图2所示,由伺服机构、切削过程、参考模型调节机构、前馈装置和反馈装置等环节组成。
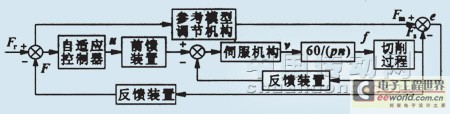
图2 切削加工过程MRAC模型框图
伺服环节可用一个二节系统表示:
(1)
式中:s为拉氏变换的算子;u为伺服输入(V);Kn为伺服增益(mm/(V·s));ωn为伺服系统的自然频率(rad/s);v为进给速度(mm/s);ξ为阻尼系数;f为进给量(mm/r),可表示为:
(2)
式中:n为主轴转速(r/min);户为铣削时刀具的齿数,车削时p=1。
考虑到参考模型调节机构是作为理想的性能指标,因此,该环节依然和伺服机构的环节一样,即
切削加工过程的静态切削力Fs可表示为:
(3)
式中:Ks为切削比力(N/mm2),m为指数(一般m<1),Ks、m都取决于工件材料和刀具形状;a为背吃刀量(mm)。
根据不同加工过程特性,Fs动态过程也可由式(3)表示。假设m=1,其动态过程可用一个一阶系统来表示:
(4)
式中:τ为时间常数。
模型中的前馈装置和反馈装置都是比例环节,比例系数为K。
因此,根据以上各个系统环节的组成,可以得到如图3所示的切削加工过程MRAC的数学控制模型。
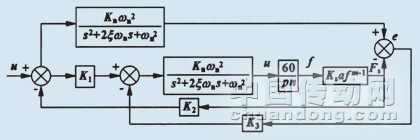
图3 切削加工过程MRAC数学模型
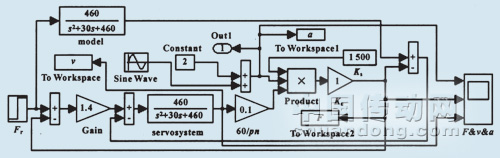
图4 MRAC仿真图
3 机床加工过程MRAC的切削性能
在机床加工过程中,切削性能的好坏不仅对零件的质量会有很大的影响,而且还很容易损坏刀具。而机床、刀具、工件系统的切削过程是个不稳定的过程,它经常受外界很多不确定因素干扰,导致切削过程中的状态参数随时发生变化。如果不及时调整,切削性能就会大大下降。通过MRAC调节,可以使切削性能的参数一直处于稳定状态。现以机床加工过程中切削力恒定在设定值为例来说明随外界因素(以背吃刀量的变化为例)干扰时MRAC能及时调整切削力,使之一直处于期望的切削力。根据实验,已知加工模型中参数Ks=1500N/mm2,n=600r/min,Kn=0.95mm/(V·s),ξ=0.68,p=1,m=1,ωn=22rad/s,背吃刀量从1~3mm按正弦曲线变化,设定切削力的期望值为1000N。将以上参数代人图3的数学控制模型中,利用MATLAB/SIMULINK工具可得到如图4所示的仿真图,其仿真结果如图5所示。
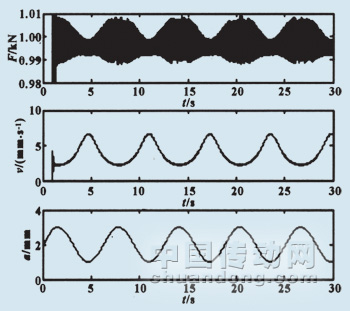
图5 仿真结果
从图5中的仿真结果可以看到,背吃刀量的变化与进给速度的变化刚好相反,也就是说,如果背吃刀量增加,进给速度就降低,以保持切削力恒定在1000N上,反之亦然。所以,MRAC系统通过自动并准确调节加工过程的进给速度,来实现加工过程的恒力控制。
4 MRAC和传统闭环及开环控制的切削性能比较
4.1 传统闭环及开环控制系统的切削性能仿真
参照MRAC仿真图4可分别建立闭环和开环仿真图(开环仿真图无反馈,其它同闭环仿真,可参照闭环图,本文已略),如图6所示,其仿真结果如图7和8所示。从仿真结果可以看到闭环控制的切削力基本也能使其恒定在1000N左右,而开环控制的切削力就远远偏离了1000N。
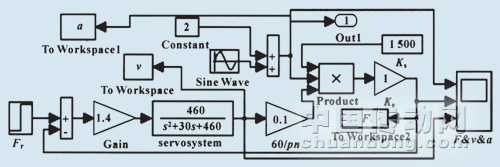
图6 闭环控制仿真图
图7 闭环控制仿真结果
图8 开环控制仿真结果
4.2 3种控制系统之间的切削性能误差分析
从以上3种控制的仿真结果图可以大致对它们的加工切削性能误差进行分析。首先,MRAC系统的误差可大致求得:
闭环控制系统的误差可求得:
开环控制系统的误差可求得:
式中:E(X)和E(S)分别表示误差的上下偏差。
通过比较,可以发现MRAC系统误差最小,所以MRAC比传统闭环和开环系统更能使车床在加工中保持良好的切削性能。
5 结束语
通过MATLAB/SIMULINK仿真和实验证明,MRAC能够使数控机床切削加工性能一直处于良好的稳定状态,鉴于此,也可以让MRAC应用于其它自动化设备。需要注意的是常规的MRAC只能适用于最小相位系统,而加工过程在一定采样条件下可能是非最小相位系统,具有不稳定逆零点,此时需要采用修正的MRAC方案。
上一篇:智能视频监控应用系统设计攻略
下一篇:基于S3C44B0X的移动机器人的应用研究
- 柔灵科技陈涵:将小型、柔性的脑机接口睡眠设备,做到千家万户
- 微灵医疗李骁健:脑机接口技术正在开启意识与AI融合的新纪元
- USB Type-C® 和 USB Power Delivery:专为扩展功率范围和电池供电型系统而设计
- 景昱医疗耿东:脑机接口DBS治疗技术已实现国产替代
- 首都医科大学王长明:针对癫痫的数字疗法已进入使用阶段
- 非常见问题解答第223期:如何在没有软启动方程的情况下测量和确定软启动时序?
- 兆易创新GD25/55全系列车规级SPI NOR Flash荣获ISO 26262 ASIL D功能安全认证证书
- 新型IsoVu™ 隔离电流探头:为电流测量带来全新维度
- 英飞凌推出简化电机控制开发的ModusToolbox™电机套件
- 意法半导体IO-Link执行器电路板为工业监控和设备厂商带来一站式参考设计