This article discusses important considerations when designing a DC-DC power supply. Topics include choosing the right DC-DC converter for the application; MOSFET gate capacitance; high switching frequencies and component size; equations and calculations; selecting peripheral components; component placement and trade-offs; grounding; load and line regulation; temperature sensitivity.
Also see:
There are few comprehensive sources of DC-DC design information. Engineering textbooks discuss control theory, loop compensation, and other highly detailed analytical methods. Data sheets for DC-DC converters give specific formulas and some layout information. Less information is available to guide the overall design of integrated-circuit-based DC-DC converters from start to finish.
This article fills in information gaps for a first DC-DC power supply design. It is the result of the author's failures and successes with scores of power-supply circuits.
Note that a boost DC-DC converter output will rise with input voltage when the input exceeds what has been set for the output voltage. Similarly, a buck converter cannot provide the desired output when the input voltage is less than that output. It is said to be "in dropout" when that happens.
Many DC-DC load requirements can be met by DC-DC converter ICs that include integral power switches. Most such ICs include MOSFETs, but some employ bipolar transistors. The load current capability of newer internal MOSFET DC-DC ICs can handle up to 25A (e.g., the MAX8655 andMAX8686). An internal-switch device, if available, is usually preferred, both for overall simplicity and (often) for lower total cost.
High-power or high-voltage applications that exceed the abilities of internal-MOSFET devices will need external MOSFET switches. DC-DC converters designed for driving external power switches are usually called "controllers." These ICs include drivers for quickly charging and discharging an external MOSFETs' gate capacitance. The ability to quickly charge and discharge a MOSFET gate is critical in achieving high-efficiency conversion. The switch wants to spend as little time as possible in transition between its on and off states because that is when power loss is greatest. Most DC-DC controllers specify a maximum gate capacitance that they can drive. (See the section, MOSFET gate capacitance below.)
In addition to topology, voltage, and current considerations, there are likely to be other application characteristics that direct the choice of DC-DC IC. For example, in most automotive applications a DC-DC converter should be able to tolerate cold-crank and load-dump conditions as well as a -40°C to +125°C temperature range. Maxim's on-line parametric search tool helps choose among converter features and specifications.
In circuits where the source voltage does change during switching, the more useful dynamic parameter is reverse transfer capacitance (CRSS). CRSS is used in calculating switching loss in a high-side n-Channel MOSFET of a buck converter in accordance with the following equation:
The next most common control scheme is pulse-frequency modulation (PFM), where the converter supplies switching pulses only when required by the load. PFM converters excel in applications that require low quiescent current and high efficiency at very small loads. Some converters ICs employ both schemes to combine good idle-mode efficiency with low noise.
The switching frequencies of IC DC-DC converters and controllers range from 65kHz to over 4MHz. In general, it is probably best to avoid devices that operate below 100kHz, as such frequencies are typical of old devices with poor efficiency. Higher switching frequency allows smaller external components along with lower peak currents and I²R losses, but core losses, gate-charge currents, and switching losses increase. (See the section on High-switching frequency reduces component size.) If the application demands the smallest possible size, then look for converters with switching frequencies at 1MHz and above. Otherwise, simply choose a device that meets the power criteria and verify that its switching frequency does not interfere with other components in the system.
Higher switching frequency also reduces the size of the output capacitor. In the example above, the capacitance required is 67µF at 500kHz, but only 33µF at 1MHz. The ripple-current specification remains unchanged.
After choosing a particular device type (buck, boost, etc.), make the final selection by consulting DC-DC converter manufacturers' websites. Always check the manufacturer's website for the latest data sheet. While there, look for application notes that apply to the device that you are considering. They serve as a guide and often include circuits that can be used with little or no modification. (See: Power Supply Cookbook, Maxim's power supply application notes, and the power and battery-management products.)From application notes and data sheets you can obtain the equations that govern the design for your device.
As an example, consider the MAX1742, an internal-switch buck converter. The data sheet's Design Procedure section gives necessary information and the order for calculations. We assume a constant 5V input, a 3.3V output with maximum load current of 500mA, and a 500kHz operating frequency.
Use the defined variable names whenever possible. As you enter more equations, define the results of those calculations with more names. Choose the names so you can easily remember what they mean when you check the calculations later.
First, across the top of a new worksheet, enter names for all predetermined values (Figure 1). These names might include VINMIN, VINMAX, VOUT, IOUT, FREQ (frequency), and other terms associated with the converter. In the cells immediately beneath the cells containing those names, define cell names to match the names typed above.

Figure 1. Using cell names in spreadsheets.
To define a cell name: select the cell to be named, go to the Insert menu and select Name, then Define on the submenu. In Excel, a dialog box pops up to suggest (as a default name) the text immediately above the selected cell. To name the cell, click OK on this dialog box. Proceed across the row until all these fields have been named. This naming procedure allows you to refer to VINMAX in your calculations instead of cell A2. Note that the selected cell in Figure 1 is A2, with a value of 5. The cell's name is indicated just above the row labeled A. Next, scan through the design procedure and pick all the required component values (Table 1). Note that original spreadsheet values have been converted to SI units for clarity.
Table 1. Initial component calculations
First calculate RTOFF.
Choose the value for LIR, then calculate L and IPEAK.
Next the output capacitor parameters are calculated.
Soft-start calculations
The inductor is selected primarily based on inductance value, DC resistance (DCR), and the peak-current requirement. Also make sure that the inductor is designed to operate at the desired switching frequency. If that data is not provided, choose another inductor for which the data is available. Inductors are available in surface-mount and through-hole versions, but in general surface-mount types offer better performance, particularly at high switching frequencies. In our example we have a close match with a Coiltronics® Thin-Pac TP1-150, a 15µH inductor with 0.73A saturation current.
The input capacitor reduces both peak current drawn from the input supply, and radiated noise to other elements of the system. Most data sheets either suggest specific values or give equations for calculating the input capacitor value. Make sure that the capacitor is specified with a ripple-current rating near the selected switching frequency. For our 500kHz example, the capacitor could be an organic electrolyte, organic polymer, ceramic, or tantalum type.
Tantalum capacitors can respond violently to large instantaneous voltage steps and high current surges so do not use tantalum for input bypassing where input power will be connected through a mechanical switch. Our circuit input is from a regulated supply, so we need not worry about that limitation. We therefore select a capacitor that meets the ripple-current rating and voltage requirements, such as an AVX® TPS series 100µF capacitor in the C size case and rated for 10V and 742mA ripple current. The input-capacitor ripple current in a step-down converter can be approximated as:
The soft-start capacitor and the tOFF resistor have no special requirements; select them from the closest available standard values. To complete component selection, choose the remaining values from a typical application circuit or the evaluation (EV) kit schematic.
Table 2. Checking actual component values
The most critical node in most cases is the common ground between the input and output capacitors and the ground pin of the IC. These three grounds must be very close, usually within 10mm of each other (Figures 2a and 2b). During the charge cycle (Figure 2a), current flows from the input capacitor through the high-side switch, inductor, output capacitor, across the ground plane, and back into the input capacitor. During the discharge cycle (Figure 2b) current continues to flow through the inductor, output capacitor, across the ground plane, back through the IC's ground pin, through the low-side switch, and back into the inductor.

Figure 2. These diagrams illustrate current paths during step-down DC-DC converter's charge (a) and discharge (b) cycles.
Because this circulating current can interfere with other circuits, its path length must be kept short (Short paths also contribute to stable operation and efficiency). Too long a path length in the ground portion (during either cycle) can compromise the circuit's reference for other circuit elements. That condition can also lead to poor regulation, excessive output ripple, and even instability. Placing the input capacitor ground, output capacitor ground, and IC ground adjacent to each other minimizes those unwanted effects.
Another important consideration for the ground connections of current-carrying components is to use multiple parallel PCB vias if the ground plane is on another PCB layer. This is especially important for input and output filter capacitors. A single via often adds resistance and inductance in series with the capacitor, reducing its effectiveness.
The local ground plane is a solid copper polygon best tied to the power ground plane at one point only, typically the pin titled PGND. Local ground planes prevent switching currents from polluting the low-noise local ground plane. Those switching currents often exceed 10A.
When routing nonpower traces on circuit boards, consider the DC and AC components of the signal. Remember that every trace is a resistor and an inductor, and may also capacitively couple to other traces. Each signal's use in the circuit determines the optimal trace width and length. High-speed and high-current signals demand short, wide traces. Longer, thinner traces are acceptable for less critical signals such as low-speed logic. Route high-speed switching nodes away from sensitive analog areas like the compensation network and feedback node. Also keep the compensation and feedback networks as small as possible to prevent noise pickup. When provided, refer to the layout and grounding guidelines on the PCB layout of the EV kit for more help.
In laptops, efficiency is important over a wide range of operating conditions. Examples include low battery, full battery, and battery charging under both standby and operating states. In other applications, the efficiency-critical points depend on how the device is used. Light-load efficiency and quiescent operating current can be most important in small handheld device like a personal glucose meter, while full-load efficiency and heat generation are most critical in network hardware.
The best way to evaluate a system over temperature is to use an environmental chamber. The chamber lets you conduct computer-controlled experiments over a broad range of temperatures and with an accuracy of 1°C or better. In cases where a chamber is not possible, you can still get an idea of overtemperature performance with less sophisticated equipment. Common heat guns and even hairdryers are useful in heating a circuit while under test. To cool a circuit well below ambient temperature, spray it with a compressed inert gas cold spray (offered in many technical catalogs). When cooling components, avoid condensation. If condensation does occur, understand that a circuit fluctuation might be due to moisture on the circuit board and not circuit sensitivity to temperature.
Maxim offers EV kits for most of its DC-DC converters. Maxim's free EE-Sim simulation tool can also be used for more reliable power supply designs, and is available for a growing number of power supply devices.
关键字:DC-DC power
编辑:神话 引用地址:Building a DC-DC power supply
Also see:
- Application note 2031, "DC-DC Converter Tutorial"
- Power Supply Cookbook
Introduction
A designer's first DC-DC converter circuit generally has one thing in common with first attempts in any other field: it has a slim chance of working satisfactorily when first powered. That may sound like a gloomy assessment, but it nevertheless reflects the realities of switch-mode power-supply design. DC-DC converters are complex systems. Even when simplified by highly integrated ICs, they still require extensive component calculations and thoughtful selection of the controller IC. In addition, they are sensitive to board layout and component parasitics (i.e., the characteristics of a component that are not ideal, such as resistance in a capacitor or capacitance in a MOSFET switch).There are few comprehensive sources of DC-DC design information. Engineering textbooks discuss control theory, loop compensation, and other highly detailed analytical methods. Data sheets for DC-DC converters give specific formulas and some layout information. Less information is available to guide the overall design of integrated-circuit-based DC-DC converters from start to finish.
This article fills in information gaps for a first DC-DC power supply design. It is the result of the author's failures and successes with scores of power-supply circuits.
Device selection
Once the initial specs of a DC-DC design are selected (e.g., input voltage range, output voltage, output current), the first step is to select a converter IC. The desired DC-DC topology will narrow this choice. If the input voltage is greater than the output voltage, choose a buck (i.e., step-down) topology. If the input voltage is less than the output voltage, choose a boost (i.e., step-up) configuration. If the input voltage ranges above and below the output voltage, a buck-boost converter or a SEPIC converter is needed. Lastly, if the output voltage is negative, an inverting topology is used.Note that a boost DC-DC converter output will rise with input voltage when the input exceeds what has been set for the output voltage. Similarly, a buck converter cannot provide the desired output when the input voltage is less than that output. It is said to be "in dropout" when that happens.
Many DC-DC load requirements can be met by DC-DC converter ICs that include integral power switches. Most such ICs include MOSFETs, but some employ bipolar transistors. The load current capability of newer internal MOSFET DC-DC ICs can handle up to 25A (e.g., the MAX8655 andMAX8686). An internal-switch device, if available, is usually preferred, both for overall simplicity and (often) for lower total cost.
High-power or high-voltage applications that exceed the abilities of internal-MOSFET devices will need external MOSFET switches. DC-DC converters designed for driving external power switches are usually called "controllers." These ICs include drivers for quickly charging and discharging an external MOSFETs' gate capacitance. The ability to quickly charge and discharge a MOSFET gate is critical in achieving high-efficiency conversion. The switch wants to spend as little time as possible in transition between its on and off states because that is when power loss is greatest. Most DC-DC controllers specify a maximum gate capacitance that they can drive. (See the section, MOSFET gate capacitance below.)
In addition to topology, voltage, and current considerations, there are likely to be other application characteristics that direct the choice of DC-DC IC. For example, in most automotive applications a DC-DC converter should be able to tolerate cold-crank and load-dump conditions as well as a -40°C to +125°C temperature range. Maxim's on-line parametric search tool helps choose among converter features and specifications.
MOSFET gate capacitance
Power MOSFET manufacturers provide various dynamic and switching parameters on their data sheets in addition to DC specs like on-resistance. In most cases, when using external MOSFETs with DC-DC converters, total gate charge (QG) is of primary interest. Choose MOSFETs for which the QG is within the range recommended by the manufacturer of the DC-DC converter. Using the MOSFET's typical QG value is fine for most cases. The maximum number is usually overly conservative. The QG spec is used when driving an "open-drain" low-side n-channel or high-side p-channel MOSFET, or in other words, when the MOSFET source does not change voltage during switching.In circuits where the source voltage does change during switching, the more useful dynamic parameter is reverse transfer capacitance (CRSS). CRSS is used in calculating switching loss in a high-side n-Channel MOSFET of a buck converter in accordance with the following equation:
PD(switching) = (CRSS × VIN(MAX)² × fSW × ILOAD)/IGATEWhere IGATE is the peak gate source and sink current, and fSW is the switching frequency.
PWM and other control schemes
The most popular DC-DC converter control scheme is pulse-width modulation (PWM). PWM converters maintain a constant switching frequency over a broad range of loads. That behavior can be important when switching noise might interfere with other processes in a system. Confining the noise to a known band often mitigates interference.The next most common control scheme is pulse-frequency modulation (PFM), where the converter supplies switching pulses only when required by the load. PFM converters excel in applications that require low quiescent current and high efficiency at very small loads. Some converters ICs employ both schemes to combine good idle-mode efficiency with low noise.
The switching frequencies of IC DC-DC converters and controllers range from 65kHz to over 4MHz. In general, it is probably best to avoid devices that operate below 100kHz, as such frequencies are typical of old devices with poor efficiency. Higher switching frequency allows smaller external components along with lower peak currents and I²R losses, but core losses, gate-charge currents, and switching losses increase. (See the section on High-switching frequency reduces component size.) If the application demands the smallest possible size, then look for converters with switching frequencies at 1MHz and above. Otherwise, simply choose a device that meets the power criteria and verify that its switching frequency does not interfere with other components in the system.
High-switching frequency reduces component size
A continuous trend in DC-DC converters is to higher switching frequencies in order to achieve smaller component sizes. When more switching cycles occur per second, the energy per switching cycle (and the size of the components that store that energy) can be smaller. Inductor values, for instance, can be lower. Inductor behavior is governed by the following equations:VL = L × (di/dt)For example, consider a buck converter operating at 500kHz with a 10µH inductor. Changing the frequency to 1MHz allows exactly one-half the inductance, or 5µH, to be used to achieve the same power transfer. Although the inductance value decreases by one-half, the current requirement remains the same. The second equation shows that we just reduced the inductor's required energy storage by half as well. Since inductance is proportional to the square of the number of turns, reducing inductance by half means the turns count is reduced to 70.7% of the original number. Reducing the turns also proportionally lowers the DC resistance (DCR), so the resulting inductor is smaller and has lower DCR.
WL = (L × i²)/2
Higher switching frequency also reduces the size of the output capacitor. In the example above, the capacitance required is 67µF at 500kHz, but only 33µF at 1MHz. The ripple-current specification remains unchanged.
After choosing a particular device type (buck, boost, etc.), make the final selection by consulting DC-DC converter manufacturers' websites. Always check the manufacturer's website for the latest data sheet. While there, look for application notes that apply to the device that you are considering. They serve as a guide and often include circuits that can be used with little or no modification. (See: Power Supply Cookbook, Maxim's power supply application notes, and the power and battery-management products.)From application notes and data sheets you can obtain the equations that govern the design for your device.
Design equations
DC-DC converter data sheets should contain equations helpful for designing your circuit. Macro models or spreadsheet files for calculating component values may also be available on the product webpage. Be sure to read the IC data sheet carefully to ensure that you select the proper equations for the required performance and operating mode. Once the major design parameters are known and you have the right equations, the best tool for evaluating the equations is a spreadsheet such as Excel® or an engineering-math program such as MathCAD. Maxim's EE-Sim® tool generates an interactive schematic that features a highly efficient simulation engine. If the selected device has an EE-Sim model, use that to calculate the appropriate components for your design.Spreadsheet calculations
Spreadsheets are an effective basic design tool for DC-DC converters. They can even serve as crude circuit simulators, and their "Solve" feature can help optimize component values. When used with DC-DC converter equations, a spreadsheet allows an iterative approach that aids component selection by quickly indicating cause-and-effect relationships.As an example, consider the MAX1742, an internal-switch buck converter. The data sheet's Design Procedure section gives necessary information and the order for calculations. We assume a constant 5V input, a 3.3V output with maximum load current of 500mA, and a 500kHz operating frequency.
Use the defined variable names whenever possible. As you enter more equations, define the results of those calculations with more names. Choose the names so you can easily remember what they mean when you check the calculations later.
First, across the top of a new worksheet, enter names for all predetermined values (Figure 1). These names might include VINMIN, VINMAX, VOUT, IOUT, FREQ (frequency), and other terms associated with the converter. In the cells immediately beneath the cells containing those names, define cell names to match the names typed above.

Figure 1. Using cell names in spreadsheets.
To define a cell name: select the cell to be named, go to the Insert menu and select Name, then Define on the submenu. In Excel, a dialog box pops up to suggest (as a default name) the text immediately above the selected cell. To name the cell, click OK on this dialog box. Proceed across the row until all these fields have been named. This naming procedure allows you to refer to VINMAX in your calculations instead of cell A2. Note that the selected cell in Figure 1 is A2, with a value of 5. The cell's name is indicated just above the row labeled A. Next, scan through the design procedure and pick all the required component values (Table 1). Note that original spreadsheet values have been converted to SI units for clarity.
Table 1. Initial component calculations
VINMAX | VINMIN | VOUT | IOUT | Frequency |
5 | 5 | 3.3 | 0.5 | 500kHz |
First calculate RTOFF.
VPMOS | VNMOS | tOFF | RTOFF |
45mV | 35mV | 673ns | 66.3kΩ |
Choose the value for LIR, then calculate L and IPEAK.
LIR_INIT | L | IPEAK |
30% | 14.8µH | 575mA |
Next the output capacitor parameters are calculated.
IRIPPLE | ESR_MIN | COUT_MIN |
529.6mA | 0.22Ω | 6.73µF |
Soft-start calculations
tSS | CSS |
100ms | 0.22µF |
Component selection
Using values from Table 1, select the DC-DC converter's peripheral components. Check the data sheet recommendations to ensure each component's suitability for the task. If the calculated inductor value is not available, choose the next smaller standard value. If a calculated capacitor value is not available, choose the next larger standard size.The inductor is selected primarily based on inductance value, DC resistance (DCR), and the peak-current requirement. Also make sure that the inductor is designed to operate at the desired switching frequency. If that data is not provided, choose another inductor for which the data is available. Inductors are available in surface-mount and through-hole versions, but in general surface-mount types offer better performance, particularly at high switching frequencies. In our example we have a close match with a Coiltronics® Thin-Pac TP1-150, a 15µH inductor with 0.73A saturation current.
The input capacitor reduces both peak current drawn from the input supply, and radiated noise to other elements of the system. Most data sheets either suggest specific values or give equations for calculating the input capacitor value. Make sure that the capacitor is specified with a ripple-current rating near the selected switching frequency. For our 500kHz example, the capacitor could be an organic electrolyte, organic polymer, ceramic, or tantalum type.
Tantalum capacitors can respond violently to large instantaneous voltage steps and high current surges so do not use tantalum for input bypassing where input power will be connected through a mechanical switch. Our circuit input is from a regulated supply, so we need not worry about that limitation. We therefore select a capacitor that meets the ripple-current rating and voltage requirements, such as an AVX® TPS series 100µF capacitor in the C size case and rated for 10V and 742mA ripple current. The input-capacitor ripple current in a step-down converter can be approximated as:
IRIPPLE_CIN (RMS) = [IOUT/VIN][VOUT (VIN - VOUT)]-1/2As a starting point, choose a capacitor that meets the recommended minimum value of 22µF and verify that it meets the required voltage rating. For our example, the AVX TPS series 33µF capacitor in the C size case is rated for 10V operation. Its maximum ESR is 0.375Ω, which is close to the target.
The soft-start capacitor and the tOFF resistor have no special requirements; select them from the closest available standard values. To complete component selection, choose the remaining values from a typical application circuit or the evaluation (EV) kit schematic.
Spreadsheet revisited
Because capacitors and inductors come in a finite number of standard values, the closest available value can differ from the calculated value by more than 20%. In that case, the spreadsheet should be recalculated with actual values to verify that the circuit still meets its design objectives. As shown in Table 2, further corrections are not necessary because our RTOFFand inductor choices have a minimal impact on the circuit's operating point.Table 2. Checking actual component values
Calculate tOFF and frequency using selected RTOFF value. | ||
RTOFF | tOFF | Frequency |
68kΩ | 688ns | 488.8kHz |
Calculate LIR and IPEAK using selected L value. | ||
L | LIR | IPEAK |
15µH | 30.3% | 576mA |
Component placement
When laying out the PCB for this example, you should first place the DC-DC converter IC (e.g., the MAX1742), the inductor, and the input and output capacitors. Then, move those components so the input capacitor is close to the MAX1742's input pins; the inductor is close to the IC's LX pin; and the output capacitor is close to the inductor and the IC's ground pins. Optimizing all of these component positions may require compromises, depending on the IC pin locations. In Maxim's DC-DC converter ICs, pin locations are carefully selected for circuit performance and ease of PCB layout.The most critical node in most cases is the common ground between the input and output capacitors and the ground pin of the IC. These three grounds must be very close, usually within 10mm of each other (Figures 2a and 2b). During the charge cycle (Figure 2a), current flows from the input capacitor through the high-side switch, inductor, output capacitor, across the ground plane, and back into the input capacitor. During the discharge cycle (Figure 2b) current continues to flow through the inductor, output capacitor, across the ground plane, back through the IC's ground pin, through the low-side switch, and back into the inductor.

Figure 2. These diagrams illustrate current paths during step-down DC-DC converter's charge (a) and discharge (b) cycles.
Because this circulating current can interfere with other circuits, its path length must be kept short (Short paths also contribute to stable operation and efficiency). Too long a path length in the ground portion (during either cycle) can compromise the circuit's reference for other circuit elements. That condition can also lead to poor regulation, excessive output ripple, and even instability. Placing the input capacitor ground, output capacitor ground, and IC ground adjacent to each other minimizes those unwanted effects.
Another important consideration for the ground connections of current-carrying components is to use multiple parallel PCB vias if the ground plane is on another PCB layer. This is especially important for input and output filter capacitors. A single via often adds resistance and inductance in series with the capacitor, reducing its effectiveness.
Power ground
After placing components according to the criteria above, the common ground is connected either with wide traces or with a polygon of solid copper. Use as much copper as possible to create a low-impedance path between the elements.Local ground
The typical application circuit for many DC-DC converter ICs indicates multiple symbols for ground—this is an excellent hint on how to accomplish a successful circuit layout. One of the different symbols often indicates a local ground plane and is typically titled SGND or AGND. Elements that connect to the local ground plane can include reference-bypass capacitors, resistor-dividers, and resistors that set operating points (such as resistor RTOFF in the example), but should not include high-current grounds such as those from switch MOSFETs.The local ground plane is a solid copper polygon best tied to the power ground plane at one point only, typically the pin titled PGND. Local ground planes prevent switching currents from polluting the low-noise local ground plane. Those switching currents often exceed 10A.
Ground plane
Because many systems rely on a separate ground plane for all components on the PCB, it is often tempting to use the ground plane of the DC-DC converter section for that purpose. That temptation should be avoided. The switching currents mentioned above can cause ground glitches across the board, produce excessive EMI, cause invalid logic states, raise the noise level, and cause instability. The proper interface between DC-DC converter circuitry and the ground plane is a single via (or a small grouping of multiple vias), leading from the poured copper power ground to the buried ground plane.Signal routing
After completing the initial ground layout, make the required connections for the first four critical components and then place and route the remaining components. A useful approach is to take all noncritical signals to the backside of the PCB with small vias while reserving the top side of the board for the routing of critical high-current traces.When routing nonpower traces on circuit boards, consider the DC and AC components of the signal. Remember that every trace is a resistor and an inductor, and may also capacitively couple to other traces. Each signal's use in the circuit determines the optimal trace width and length. High-speed and high-current signals demand short, wide traces. Longer, thinner traces are acceptable for less critical signals such as low-speed logic. Route high-speed switching nodes away from sensitive analog areas like the compensation network and feedback node. Also keep the compensation and feedback networks as small as possible to prevent noise pickup. When provided, refer to the layout and grounding guidelines on the PCB layout of the EV kit for more help.
Verification
After the converter is completed, and prototype boards assembled, the overall design should be verified for performance to the original criteria. If the design was implemented diligently with regard to the issues discussed, chances for initial success are good. But even conscientious designs may still require "tweaking." When making changes, verify with calculations or models to be sure that some other important characteristic is not being compromised. For example, you may determine that output ripple is acceptable with smaller output filter capacitance, but such a change might also impact stability.Efficiency
Efficiency is often a key DC-DC converter performance parameter, particularly for devices operating from a battery, and especially so for power supplies in laptop computers and small handheld equipment. Laptop power-supply efficiency directly affects battery life, but it also impacts power dissipation; it should be coordinated with the heat-removal limitations. Note that a DC-DC converter supplying 50W at 85% efficiency still dissipates 8.8W of heat inside the case.In laptops, efficiency is important over a wide range of operating conditions. Examples include low battery, full battery, and battery charging under both standby and operating states. In other applications, the efficiency-critical points depend on how the device is used. Light-load efficiency and quiescent operating current can be most important in small handheld device like a personal glucose meter, while full-load efficiency and heat generation are most critical in network hardware.
Load regulation
A converter's ability to stay within the specified output-voltage tolerance, regardless of load, is called load regulation. It applies at DC, but it also includes fast transients such as those encountered with high-speed CPUs. You should verify that the output voltage stays within specification when loaded with currents ranging from zero to the maximum. Ensure that the output voltage does not undershoot its minimum value when the load changes quickly from minimum to maximum. Ensure that it does not exceed its maximum value when the load current drops from maximum to minimum. Note that the line- and load-regulation specs quoted in most data-sheet electrical characteristics tables are measured at DC, while transient performance is usually shown in the typical operating curves. For more information, see application notes 752, "Creating a fast load transient," and 3453, "Testing a power supply for line and load transients."Line regulation
A power supply's ability to maintain output-voltage regulation with a varying input voltage is called line regulation. Again, it should be examined both at DC and with a fast AC transient. A transient is encountered when a laptop computer switches from its AC adapter supply to its internal battery and back. In some systems, the voltage change can be as large as 10V. Verify that the output voltage stays within specification when the input voltage changes from minimum to maximum. Make sure that step changes in the input voltage do not cause peaks or valleys in the output voltage that exceed the output-voltage specifications.Temperature sensitivity
It may be convenient to evaluate a system on a lab bench and judge it ready for the application, but one more critical condition needs examination: performance over the worst-case operating-temperature range. Performance to the electrical criteria above should be measured at the highest and lowest temperatures that the system will encounter during operation. Watch for parameters that change drastically and those that approach upper or lower limits over temperature.The best way to evaluate a system over temperature is to use an environmental chamber. The chamber lets you conduct computer-controlled experiments over a broad range of temperatures and with an accuracy of 1°C or better. In cases where a chamber is not possible, you can still get an idea of overtemperature performance with less sophisticated equipment. Common heat guns and even hairdryers are useful in heating a circuit while under test. To cool a circuit well below ambient temperature, spray it with a compressed inert gas cold spray (offered in many technical catalogs). When cooling components, avoid condensation. If condensation does occur, understand that a circuit fluctuation might be due to moisture on the circuit board and not circuit sensitivity to temperature.
Conclusion
DC-DC power-supply design is neither rocket science nor common knowledge. The list of characteristics that need to be addressed in a successful design may seem daunting, but a methodical approach can result in a working circuit with minimal iteration. By applying the principles in this article, you can eliminate most of the typical first-design missteps.Maxim offers EV kits for most of its DC-DC converters. Maxim's free EE-Sim simulation tool can also be used for more reliable power supply designs, and is available for a growing number of power supply devices.
上一篇:集成电路热插拔电路基础知识
下一篇:SMB20x设计的DC-DC电源转换方案
推荐阅读最新更新时间:2023-10-13 10:55
实现功率因数校正的电源和适配器方案
半导体是实现高能效电子产品的重要环节,可以提供满足全球市场相关规范的解决方案。安森美半导体是其中的代表企业,其所提供的电源和适配器可实现高工作电源能效、低待机能耗及功率因数校正。
丰富的电源及电源适配器参考设计
安森美半导体的电源解决方案涵盖了AC-DC电源及适配器和DC-DC电源,并提供了各种参考设计。最典型的是为内部和外部电源提供的GreenPoint?参考设计。这些开放式参考设计为高效电源设计提供了开发路线图,借助原理图、物料单、Gerber文件、设计说明、测试结果等文档,客户可快速进入市场。该参考设计符合所有相关全球能效标准,提供了用一个设计进入全球市场的机遇。
以下一些参考设计和实例电路从多方
[电源管理]
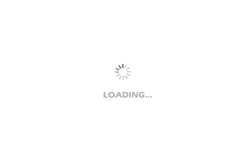
LDO及DC-DC的对比
应当可以这样理解:DC-DC的意思是直流变(到)直流(不同直流电源值的转换),只要符合这个定义都可以叫DC-DC转换器,包括LDO。但是一般的说法是把直流变(到)直流由开关方式实现的器件叫DC-DC。
1 什么是LDO
LDO是低压降的意思,这有一段说明:低压降(LDO)线性稳压器的成本低,噪音低,静态电流小,这些是它的突出优点。它需要的外接元件也很少,通常只需要一两个旁路电容。新的LDO线性稳压器可达到以下指标:输出噪声30μV,PSRR为60dB,静态电流6μA,电压降只有100mV。LDO线性稳压器的性能之所以能够达到这个水平,主要原因在于其中的调整管是用P沟道MOSFET,而普通的线性稳压器是使用P
[电源管理]
Moto One Power曝光:刘海屏+双摄
进入2018年,刘海屏开始流行起来。OPPO、vivo、华为、小米、一加、诺基亚等厂商都推出了刘海屏手机,现在摩托罗拉也加入了刘海屏阵营。 6月1日,知名爆料人士Slashleaks放出了摩托罗拉首款刘海屏手机Moto One Power的真机谍照,如图所示,One Power和常见的安卓刘海屏一样,保留了下巴。 至于背部设计,根据此前曝光的渲染图,Moto One Power配备了双摄像头,而且两颗摄像头呈竖形排布。 Phone Arena透露,Moto One Power可能是Moto X4的续作,所以其配置可能是中端水平,而且这款机型是Android One手机,所以它会预装原生安卓系统,在系统更新方面会比较及
[手机便携]
Silicon Labs推出支持环保型Zigbee Green Power IoT设备
-Silicon Labs宣布推出一系列安全、超低功耗的Zigbee®片上系统(SoC)新产品。这些SoC专为网状网络中的环保型IoT产品而设计。EFR32MG22(MG22)系列产品是专为Zigbee Green Power(绿色能源)应用而优化的最小、最低功耗的SoC,扩展了Silicon Labs的Zigbee产品组合。MG22 SoC基于Silicon Labs的Wireless Gecko Series 2平台,是使用纽扣电池或通过能量收集供电的Zigbee设备的理想选择,其目标应用包括智能家居传感器、照明控制以及楼宇和工业自动化等。 节能的Zigbee Green Power技术通过逐步减少住宅、商业和工业能
[嵌入式]
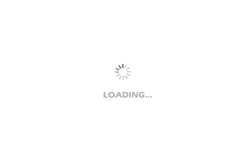
Vishay推出采用先进Power DFN系列DFN3820A封装的额定电流高达4 A的标准稳压器
Vishay推出采用先进Power DFN系列DFN3820A封装的额定电流高达4 A的标准稳压器 汽车级200 V、400 V和 600 V器件厚度仅为0.88 mm,采用可润湿侧翼封装,改善热性能并提高效率 美国 宾夕法尼亚 MALVERN、中国 上海 — 2023年3月3日 — 日前, Vishay Intertechnology, Inc. 宣布,推出三款新系列汽车级表面贴装标准整流器---2 A SE20Nx、3 A SE30Nx和4 A SE40Nx,皆为业内先进的薄型可润湿侧翼DFN3820A封装器件。 SE20Nx、SE30Nx和SE40Nx反向电压分别为200 V、400 V和600 V,可为商业、
[电源管理]
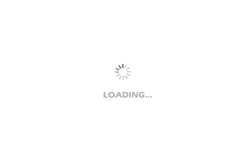
DC-DC电机伺服驱动专用电源设计
该设计采用多重滤波措施和双绞线输出方式,有效降低输出电压纹波,提高电源输出质量;具备完善的自保护功能和监控检测功能,提高了电源的安全性和可靠性。设计以DC-DC变换器为核心,实现220V市电至+60V/20A的电源转换。电源设计中采用功率因数校正技术,提高了有功功率;特别是电源设计了微机控制接口,与随动系统同步工作,并实现了上电时序控制,确保+60V电压相对低压输出滞后上电。
电源设计
系统结构
220V交流电压经整流和滤波后得到320V左右的直流电压,加至电源模块输入端。单DC-DC模块的最高输出电压一般为+48V,要得到+60V的直流输出电压,必须采用模块串联的方法得到。设计采用两块PH600S280-28
[嵌入式]
Power Integrations推出LYTSwitch-2隔离式LED驱动器IC
美国加利福尼亚州圣何塞,2014年5月20日讯 – 高效率、高可靠性LED驱动器IC领域的世界领导者Power Integrations公司(纳斯达克股票代号:POWI)今日推出LYTSwitch™-2系列隔离式LED驱动器IC。新的IC产品系列能够提供最大12 W的精确控制输出功率,并大幅减少元件数,从而实现更简单、更小巧、更可靠的LED照明设计。
LYTSwitch-2 LED驱动器IC采用初级侧控制,因此只需使用元件数较少、极具成本效益的单面PCB。此外,驱动器隔离允许LED直接连接到金属散热片,避免额外添加电气隔离的外壳,而这是非隔离驱动器通常所需要的。在不同温度下均具有精确的恒流(CC)输出容差(在低压和高压输入下
[电源管理]
Power Integrations与SnapMagic携手推进电源设计自动化
使用PI Expert and SnapMagic可在数分钟内完成从电源规格到PCB布局的整个过程 美国加州圣何塞和旧金山 – 2023年10月5日讯 – 深耕于高压集成电路(IC)高能效功率变换领域的知名公司Power Integrations 和致力于通过简化设计流程重新定义电子产品设计方式的公司SnapMagic今日宣布, Power Integrations强大的在线设计工具PI Expert™现在已具备电路原理图和网络表导出功能,这一改进得益于SnapMagic全新的电路原理图导出技术。 根据用户输入的规格参数,PI Expert可采用Power Integrations的功率变换IC自动生成完整的电源原理
[电源管理]
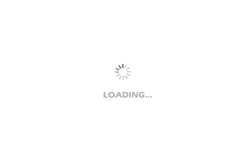