底特律和世界各地的工程师正在努力设计混合型和燃料电池汽车,这两种汽车都需要很多嵌入式系统。这些系统向设计者提出了哪些挑战呢?在这些系统中,虽然其中有些系统依靠简单的微控制器并通过基础网络同其它系统通讯,但人们也在引入带有更大内存且更加复杂的微控制器。虽然许多控制算法及其所控制的子系统不是新的,但把所有这些子系统一起放在单独的产品中并保证它们满足汽车的许多苛刻要求却是一个挑战。在本文中,我们将讨论混合型和燃料电池型车辆嵌入式系统设计所固有的各种挑战。
混合型系统
与字面意义相同,混合型推进系统结合了至少两种不同的推进方法。在汽车应用中,典型的混合型系统包含一个内燃发动机(汽油或柴油)和一个或几个电池供电的电动机。这种系统的一个优点是可以把内燃机设计成一直以最高效率工作的设备而电动机用于在高需求期间提供基本或附加推力。
混合型系统的架构主要有并联和串联两种,它们的差别体现在机械方面。在并联混合型系统中,内燃机采用与提供电功率的电动机相并联的方式向车轮提供机械功率。在串联混合型系统中,内燃机必须首先产生电力,然后通过电动机转换成车轮功率。
每种混合型架构都有数十种具体的设计。图1显示了一种并联混合型系统的电气原理图。图2显示了一种串联混合型系统的电气原理图。两个图都显示了完整的电气系统以及各种嵌入式控制系统。
图1:并联混合型系统 |
Civic混合型发动机以三种方式来减少排放和降低燃料消耗。首先,把通常在汽车减速和刹车过程中被浪费的能量用于向电池再充电。第二,当汽车空闲时,通过关闭内燃机来节省能量。电动机的功率大到足以重新启动发动机并开始同步驱动汽车。最后,由于电动机可以在高需求(如快速加速)期间提供帮助,在这款轿车中使用了一种较小的发动机而不是标准的Civic发动机。
图2显示的串联混合系统在每个轮上使用了一个电动机。这种串联设计能以与并联设计相同的方式减少排放和降低燃料消耗,但除此之外还有其它几个优点。首先,牵引和能量回收可以在车轮之间切换,因而可以实现快速牵引控制和通过电动机实现防抱死刹车。这种串联架构也提供对所有车轮进行驱动的能力,而且无需昂贵的传输箱和微分齿轮。这个架构的第二个优点是具有自然地扩展到任何数目车轮的能力,这个优点对军事应用尤为重要。最后,当发动机/发电机用于提供外部功率时,把发动机同车轮的解耦可能具有更高的效率 (没有传输产生的残留负载)。
正如两个图中所示,要使混合型汽车良好工作需要使用许多嵌入式控制器。这些控制器都是相互连接的,通常采用高速的控制器局域网(CAN)总线来互连。这些控制器中的固件必须控制系统中各自的部分并同其它控制器实时协调。这要求设计和开发许多新的控制算法和软件,甚至对发动机、传输和防抱死刹车系统(ABS)等成熟的控制系统也是如此。
燃料电池型系统
燃料电池车是由电池和燃料电池提供动力的电力车辆。燃料电池把氢气和氧气转化成电能,它所产生的副产品只有水和热。车用燃料电池的基本结构如图3所示。除了内燃机用燃料电池组替换之外,这个结构与串联混合架构类似。
尽管燃料电池技术已经出现很长时间,但在汽车所处的不受控制的环境中它依然是一种新技术。在燃料电池车大量上市以前,耐久性、可靠性和成本等问题必须得到解决。
燃料电池本身是一个复杂系统。它需要准确控制进入电池的燃料(氢气)和空气的温度和湿度。例如,进入燃料电池的空气必须满足:与电池组中薄膜的温差在2℃之内,相对湿度在70-90%范围内。如果这些要求不能得到满足,电池组将会受到损害。控制燃料电池组的嵌入式系统必须到满足各种要求。
图2:串联混合型系统[page] |
没有嵌入式系统所提供的智能,就没有混合型和燃料电池型车辆。这些嵌入式系统目前有很多元件处于相互隔离状态。内燃机(汽油型和柴油型)和车辆传动目前都是由嵌入式系统控制的。电动机控制和电池充电管理也已经在其它行业中发展成熟。燃料电池在几十年以前就也已经被用于空间探测。混合型和燃料电池型汽车成功的关键是如何把各种嵌入式系统组合在单一车辆中。
在现有电动车辆系统的设计中所做的许多假设不适于混合架构和燃料电池架构。比如,许多车辆系统假定在执行任何任务之前内燃机必须已经在运行。如果发动机没有运行就没有能量,这种说法对吗?不对。只要电池有充足的电量,串联混合系统就可以在发动机关闭的情况下运行且性能不变。电子(包括硬件和软件) 部分的成本可能还不到最终推进系统总成本的25%,但为这些元件开发算法和软件所需要的工程付出可能超过总开发成本的75%。
要把新的电子元件加入到汽车或其它机动车中必须克服许多挑战。主要的挑战涉及成本、功耗、运行环境、可靠性和耐久性、安全性和符合法规等方面。这些众所周知的约束存在于所有的嵌入式系统项目中,但在混合型和燃料电池型车辆中它们表现在不同的方面。以下将讨论这些挑战并对如何应对这些挑战提出一些建议。
成本和功耗
汽车是成本敏感型产品,其价格压力一直延伸到各个部件的设计。因为混合型车辆包括传统的功率供给系统和电力系统(电动机和电池),消费者实际需要购买两个功率供给系统。尽管降低燃料消耗所带来的成本节省在某种程度上可以抵消这个高昂的附加费用,但市场将依然要求能保持较低的初始成本。
功率管理面临两个重大的挑战。传统汽车所面临的挑战依然没有改变:降低每个控制器的功耗并把过多的热量排放出去。由于需要驱动外部执行器,驱动器电路是有名的高功率部分,而且为避免损坏电子线路,必须把它所产生的热量散掉。此外,把电动机加到车辆中意味着有更多的能量必须被耗散。
这个新的挑战源于汽车的设计目标——提高燃料效率。车辆中的嵌入式系统必须具有非常高的效率且只需很少能量就可以运行。如果通过关闭发动机来节省的能量随后又在保持控制器或执行器运行的过程中被浪费掉(特别是在不需要执行器的情况),这样做就毫无意义了。
为提高电池的使用寿命,许多电池供电的嵌入式设备在处于空闲状态时使用各种算法进入低功率模式。在混合型或燃料电池型车辆中,即使这个少量的能量节省也不能放弃,尤其当处理器总数已经给定的时候。通过在软件等待任务时进入低功率状态,嵌入式控制系统可对提高整个系统的能量效率做出贡献。
图3:燃料电池供电系统 |
控制汽车的电子部分必须在高/低温和强震动的严酷环境中工作。传统汽车电子设备的供应商熟悉这个环境。如罩内(underhood)电子设备(包括基于微控制器的系统)的温度范围规定为-40到125°C。在许多情况下这个温度被错误地看成是罩内环境温度,实际电子元件的额定温度。在非常严酷的条件下完成的测试表明,实际的罩内最高温度只有110°C,但此温度依然足以让水沸腾。
震动也是一个关键条件。以混合方式和燃料电池提供能量的车辆将第一次把电动机、电池和燃料电池的供应商带到汽车工业。这些新的供应商将不得不设计满足在许多情况下甚至可以同航空工业的要求相近的震动指标。
可靠性和耐久性
汽车电子设备需要在各种条件下可靠地运行,一般汽车要求10年/10万英里,卡车要求15年/15万英里(这些是典型数值,不同OEM厂商之间稍有差别)。
一些控制器实际上从不关闭,它们在节能状态继续运行,甚至当汽车停止使用时也是如此。
安全性
许多原告和律师正在核查是否某个有缺陷的设计导致了事故的发生并希望能够起诉工程师的雇主以获得赔偿金。这种核查和法律诉讼的风险迫使汽车工程师度过了许多不眠之夜。为保证设计在所有条件下(甚至当某个部件失效时)都是安全的,他们必须花费数万工程小时进行故障模式/后果分析(FMEA)和故障树分析(FTA)。
另一个安全特性是车辆不执行驾驶员无意做出的任何动作。随着把司机同设备分离开来的“线控(by-wire)”系统的出现,安全性已经成为一个更受关注的课题。混合型和燃料电池型系统天生就是线控驱动、线控刹车和线控驾驶的系统。在许多情况下,这将需要容错系统设计和冗余设计。
设计工具
借助于UML、Matlab/Simulink和AscetSD等建模工具,你可以开发出具有功能强大的产品。特别值得一提的是,这种方法有一个重大优点:可以在工作站上对系统进行离线仿真。通过建模,我们可以通过在项目的早期进行可靠性、安全性分析来保证系统在所有条件下正常工作,而不必等到在进行最终产品测试时才发现缺陷。
为了在实际车辆上进行测试,许多已经公布的早期概念车设计已经使用了Matlab/Simulink并在快速原型系统上使用了自动代码生成。主要的障碍将是把这个知识产权全部转换成满足所有前述挑战的可生产代码(production-ready code)。
依靠预先在设计层所做的系统仿真,当各种部件到位后,我们就可以在多种环境和多种出错情况下测试系统的功能。当软件进入最终的汽车产品时,我们已经完成了广泛的测试和开发并可以使用该车辆来验证这个模型而不是开发控制系统。这并不意味着不需要进行车辆级验证,但这样做将可以降低风险并改善最终系统的质量。
因为仿真软件将直接在建模环境下运行很多次,因此仿真和建模可以很好协同工作。这里所面临的最大的挑战是建立确实代表所仿真的设备而且具有足够高的仿真效率的仿真模型,以至于可以在合理的时间内完成仿真。
当然,还需要察看混合型或燃料电池型汽车设计的所有挑战是否都可以在这些产品中得到满足,从而使得用户乐于拥有和驾驶这些产品。
上一篇:IGBT-汽车点火系统中的佼佼者
下一篇:智能大电流功率开关可有效降低汽车电子系统成本
推荐阅读最新更新时间:2024-05-02 23:16
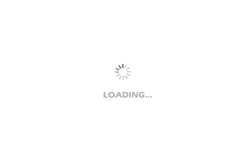
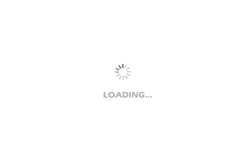
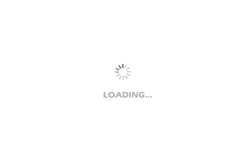
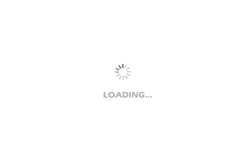
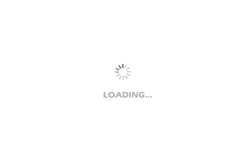
- 热门资源推荐
- 热门放大器推荐