随着信息、通讯与自动化技术的发展,种类繁多的自动控制装置逐渐进进了人们的日常生活。网络通讯技术不仅为人们提供了方便的通讯手段,实际上也为各式各样的电子裝置提供了简易可靠的通讯渠道,借助于新式的网络通讯技术与计算功能强大的数字信号处理器芯片(DSP),可以开展出多种具有基本智能的信息家电设备(smart information appliance),例如可以帮助清洁工作的机器人、可供娱乐的电子机械宠物等等。这些结合机械、电子、通讯、控制、信息技术融合装置的核心部分就是具有网络界面的伺服系统控制器(network servo controller)。伺服技术已广泛的应用于我们的日常生活,例如光碟机光学读取头的伺服控制、远控飞机的机翼控制、数字相机的自动对焦控制、具有影像追踪功能的网络摄像监控系统、汽车自动驾驶等等,伺服系统涉及范围涵盖广泛,多学科交叉色彩浓厚。
伺服控制系统的应用
伺服控制系统最初用于船舶的自动驾驶、火炮控制和指挥仪中,后来逐渐推广到很多领域,特别是自动车床、天线位置控制、导弹和飞船的制导等。
采用伺服系统主要是为了达到下面几个目的:
① 以小功率指令信号去控制大功率负载。火炮控制和船舵控制就是典型的例子。
② 在没有机械连接的情况下,由输入轴控制位于远处的输出轴,实现远距同步传动。
③ 使输出机械位移精确地跟踪电信号,如记录和指示仪表等。
伺服系统的发展和应用常识
伺服系统的发展
伺服系统在机电设备中具有重要的地位,下面简单谈谈其发展历程:
(1) 直流伺服系统
伺服系统的发展经历了由液压到电气的过程。电气伺服系统根据所驱动的电机类型分为直流(DC)伺服系统和交流(AC)伺服系统。50年代,无刷电机和直流电机实现了产品化,并在计算机外围设备和机械设备上获得了广泛的应用。70年代则是直流伺服电机的应用最为广泛的时代。
(2)交流伺服系统
从70年代后期到80年代初期,随着微处理器技术、大功率高性能半导体功率器件技术和电机永磁材料制造工艺的发展及其性能价格比的日益提高,交流伺服技术—交流伺服电机和交流伺服控制系统逐渐成为主导产品。交流伺服驱动技术已经成为工业领域实现自动化的基础技术之一,并将逐渐取代直流伺服系统。
交流伺服系统按其采用的驱动电动机的类型来分,主要有两大类:永磁同步(SM型)电动机交流伺服系统和感应式异步(IM型)电动机交流伺服系统。其中,永磁同步电动机交流伺服系统在技术上已趋于完全成熟,具备了十分优良的低速性能,并可实现弱磁高速控制,拓宽了系统的调速范围,适应了高性能伺服驱动的要求。并且随着永磁材料性能的大幅度提高和价格的降低,其在工业生产自动化领域中的应用将越来越广泛,目前已成为交流伺服系统的主流。感应式异步电动机交流伺服系统由于感应式异步电动机结构坚固,制造容易,价格低廉,因而具有很好的发展前景,代表了将来伺服技术的方向。但由于该系统采用矢量变换控制,相对永磁同步电动机伺服系统来说控制比较复杂,而且电机低速运行时还存在着效率低,发热严重等有待克服的技术问题,目前并未得到普遍应用。
系统的执行元件一般为普通三相鼠笼型异步电动机,功率变换器件通常采用智能功率模块IPM。为进一步提高系统的动态和静态性能,可采用位置和速度闭环控制。三相交流电流的跟随控制能有效地提高逆变器的电流响应速度,并且能限制暂态电流,从而有利于IPM的安全工作。速度环和位置环可使用单片机控制,以使控制策略获得更高的控制性能。电流调节器若为比例形式,三个交流电流环都用足够大的比例调节器进行控制,其比例系数应该在保证系统不产生振荡的前提下尽量选大些,使被控异步电动机三相交流电流的幅值、相位和频率紧随给定值快速变化,从而实现电压型逆变器的快速电流控制。电流用比例调节,具有结构简单、电流跟随性能好以及限制电动机起制动电流快速可靠等诸多优点。
(3)交直流伺服系统的比较
直流伺服驱动技术受电机本身缺陷的影响,其发展受到了限制。直流伺服电机存在机械结构复杂、维护工作量大等缺点,在运行过程中转子容易发热,影响了与其连接的其他机械设备的精度,难以应用到高速及大容量的场合,机械换向器则成为直流伺服驱动技术发展的瓶颈。
交流伺服电机克服了直流伺服电机存在的电刷、换向器等机械部件所带来的各种缺点,特别是交流伺服电机的过负荷特性和低惯性更体现出交流伺服系统的优越性。所以交流伺服系统在工厂自动化(FA)等各个领域得到了广泛的应用。
从伺服驱动产品当前的应用来看,直流伺服产品正逐渐减少,交流伺服产品则日渐增加,市场占有率逐步扩大。在实际应用中,精度更高、速度更快、使用更方便的交流伺服产品已经成为主流产品。
(4)伺服系统的发展趋势
从前面的讨论可以看出,数字化交流伺服系统的应用越来越广,用户对伺服驱动技术的要求越来越高。总的来说,伺服系统的发展趋势可以概括为以下几个方面:
1. 交流化
伺服技术将继续迅速地由DC伺服系统转向AC伺服系统。从目前国际市场的情况看,几乎所有的新产品都是AC伺服系统。在工业发达国家,AC伺服电机的 市场占有率已经超过80%。在国内生产AC伺服电机的厂家也越来越多,正在逐步地超过生产DC伺服电机的厂家。可以预见,在不远的将来,除了在某些微型电机领域之外,AC伺服电机将完全取代DC伺服电机。
2. 全数字化
采用新型高速微处理器和专用数字信号处理机(DSP)的伺服控制单元将全面代替以模拟电子器件为主的伺服控制单元,从而实现完全数字化的伺服系统。全数字化的实现,将原有的硬件伺服控制变成了软件伺服控制,从而使在伺服系统中应用现代控制理论的先进算法(如:最优控制、人工智能、模糊控制、神经元网络等)成为可能。
3. 采用新型电力电子半导体器件
目前,伺服控制系统的输出器件越来越多地采用开关频率很高的新型功率半导体器件,主要有大功率晶体管(GTR)、功率场效应管(MOSFET)和绝缘门极晶体管(IGBT)等。这些先进器件的应用显著地降低了伺服单元输出回路的功耗,提高了系统的响应速度,降低了运行噪声。尤其值得一提的是,最新型的伺服控制系统已经开始使用一种把控制电路功能和大功率电子开关器件集成在一起的新型模块,称为智能控制功率模块(Intelligent Power Modules,简称IPM)。这种器件将输入隔离、能耗制动、过温、过压、过流保护及故障诊断等功能全部集成于一个不大的模块之中。其输入逻辑电平与TTL信号完全兼容,与微处理器的输出可以直接接口。它的应用显著地简化了伺服单元的设计,并实现了伺服系统的小型化和微型化。
4. 高度集成化
新的伺服系统产品改变了将伺服系统划分为速度伺服单元与位置伺服单元两个模块的做法,代之以单一的、高度集成化、多功能的控制单元。同一个控制单元,只要通过软件设置系统参数,就可以改变其性能,既可以使用电机本身配置的传感器构成半闭环调节系统,又可以通过接口与外部的位置或速度或力矩传感器构成高精度的全闭环调节系统。高度的集成化还显著地缩小了整个控制系统的体积,使得伺服系统的安装与调试工作都得到了简化。
5. 智能化
智能化是当前一切工业控制设备的流行趋势,伺服驱动系统作为一种高级的工业控制装置当然也不例外。最新数字化的伺服控制单元通常都设计为智能型产品,它们的智能化特点表现在以下几个方面:首先他们都具有参数记忆功能,系统的所有运行参数都可以通过人机对话的方式由软件来设置,保存在伺服单元内部,通过通信接口,这些参数甚至可以在运行途中由上位计算机加以修改,应用起来十分方便;其次它们都具有故障自诊断与分析功能,无论什么时候,只要系统出现故障,就会将故障的类型以及可能引起故障的原因通过用户界面清楚地显示出来,这就简化了维修与调试的复杂性;除以上特点之外,有的伺服系统还具有参数自整定的功能。众所周知,闭环调节系统的参数整定是保证系统性能指标的重要环节,也是需要耗费较多时间与精力的工作。带有自整定功能的伺服单元可以通过几次试运行,自动将系统的参数整定出来,并自动实现其最优化。对于使用伺服单元的用户来说,这是新型伺服系统最具吸引力的特点之一。
6. 模块化和网络化
在国外,以工业局域网技术为基础的工厂自动化(Factory AutomaTIon 简称FA)工程技术在最近十年来得到了长足的发展,并显示出良好的发展势头。为适应这一发展趋势,最新的伺服系统都配置了标准的串行通信接口(如RS-232C或RS-422接口等)和专用的局域网接口。这些接口的设置,显著地增强了伺服单元与其它控制设备间的互联能力,从而与CNC系统间的连接也由此变得十分简单,只需要一根电缆或光缆,就可以将数台,甚至数十台伺服单元与上位计算机连接成为整个数控系统。也可以通过串行接口,与可编程控制器(PLC)的数控模块相连。
综上所述,伺服系统将向两个方向发展。一个是满足一般工业应用要求,对性能指标要求不高的应用场合,追求低成本、少维护、使用简单等特点的驱动产品,如变频电机、变频器等。另一个就是代表着伺服系统发展水平的主导产品—伺服电机、伺服控制器,追求高性能、高速度、数字化、智能型、网络化的驱动控制,以满足用户较高的应用要求。
上一篇:伺服系统调试步骤
下一篇:伺服控制系统的主要指标与技术要求
推荐阅读最新更新时间:2024-11-17 06:51
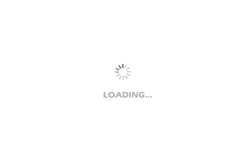
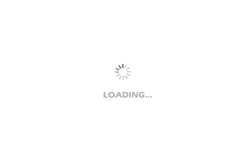
- 电源技术专辑第2期:从零开始 DIY 双向高效 DC-DC!
- 安森美半导体重磅推出超低功耗蓝牙芯片 RSL10 — 观视频答题送样片 更有丰富礼品等你拿!
- PI LYTSwitch™-6系列IC 让你了解不知道的秘密看专题赢好礼!
- 免费试用eZ430-RF2500开发套件!
- 夏末秋初,玩转EE芯积分,边赚边花+礼品兑换剧透
- 【新年活动】2023,兔 do list!
- 有奖直播报名:TI DLP®技术在汽车行业的创新应用——增强型抬头显示
- TI 邀您填问卷赢好礼|私人定制专属你的 2019 工业应用方案
- 报名Keysight感恩月,天天抽示波器、直流电源、万用表……
- 夏末狂欢,观看TI 课程有好礼!