2017年中国平板显示已经成为世界第一,占了全球市场超过22%,产业规模超过3000亿元。据预测,中国将在2019年左右成为全球最大的TFT- LCD+AMOLED平板显示生产基地。虽然产业规模做到了全球第一,然而第一的背后是大而不强,国内平板显示产业长期只具备系统集成能力,缺乏核心技术,70%以上的材料依靠进口。
近一年多来,OLED已经成为产业关注的焦点,特别是iPhone x智能手机采用OLED屏将更进一步推动OLED技术产业化应用。随着更先进的制造设备和材料工程技术的发展,可弯曲、可折叠以及曲面显示在电子产品中的应用日益丰富,为电子产品制造商带来了丰厚的获利机会。当前,以智能手机为代表的移动终端的交互体验不断在提升,同时产品外形也发生着变化,而柔性OLED的出现,为产品设计带来了更多的想象空间。在柔性显示时代,中国OLED产业与技术挑战与机遇在哪里?能否弯道超车? 12月17日,2017首届中国柔性显示技术(材料)国际论坛在深圳五洲宾馆隆重举行。本次论坛由中国光学光电子协会液晶分会、中国电子材料行业协会、中国通信工业协会、中国电子视像行业协会以及广东省触控及应用产业协会联合深圳市国际贸易促进委员会、深圳市新纶科技股份有限公司共同主办,深圳市新纶科技股份有限公司承办,深圳市金之路文化传播有限公司协办,聚焦柔性显示技术和材料,邀请显示行业国际知名专家、产业链上下游企业、教育与研发机构、社会资本、新闻媒体等共同参与,旨在共同探讨世界柔性显示行业发展趋势与发展机遇;加深各界对柔性显示产业的认知与了解;搭建产、学、研、用各界融合的平台;推动国际间的交流与合作;促进柔性显示及上下游产业链快速、健康发展;实现创新驱动、携手合作、互惠共赢。 本次论坛邀请到了著名华裔科学家、美国工程院院士程正迪教授,中国科学院院士、中国科学院物理研究所欧阳钟灿教授,美国APS公司主席哈理斯教授,中国科学院院士、华南理工大学材料科学与工程学院曹镛教授。同时还有中国大陆、美国、日本、台湾等地区著名专家学者、企业家同赴盛会,分享柔性显示技术与材料领域最前沿的技术发展动向,分析与探讨全球柔性显示产业发展趋势,推动产业链深度交流与合作,实现国际合作、互助共赢。
中国平板显示全球第一,2019年将成全球最大AMOLED显示基地
根据中国科学院院士、中国科学院物理研究所欧阳钟灿教授的介绍,2017年中国平板显示已经成为世界第一,占了全球市场超过22%,产业规模超过3000亿元。这得益于手机、电视领域中国系统厂商的崛起,中国的六大电视品牌在2012年的产量就已经占了世界的30%,市场规模达到将近1000亿美元。2015年,全球81%的手机、90%的台式机、95%的电视都是在中国生产。目前中国有5条以上10代线,京东方10.5代线将在合肥发布。被鸿海收购的夏普也要在广州建第二条10代线,而深圳也有一条11代线。这也是为什么中国显示产业可以后来居上,超过日本、台湾,预计在2018年会超越韩国。 据欧阳钟灿教授预测,中国将在2019年左右成为全球最大的TFT- LCD+AMOLED平板显示生产基地。欧阳钟灿教授表示,国内液晶和AMOLED的产值在2017年要达到1亿平方米,到2022年要达到2亿平方米。目前全球可以量产OLED的企业并不多,世界上第一条柔性显示生产线是三星的,基本上控制了手机OLED屏90%以上的产量。但是中国厂商近两年奋起直追,今年京东方在成都的6代线宣布运行后下一条在绵阳的6代线也要运行,实现量产后可以和三星抗衡。此外,目前所有的柔性生产都采用低温多晶硅,而新视界尽管只有一条2代线,但由于采用的工艺是氧化物,因此可以规避日本专利。
中国显示产业大而不强,做大做强关键在材料
美国工程院院士程正迪教授
虽然中国显示面板产业规模做到了全球第一,然而第一的背后是大而不强,国内平板显示产业长期只具备系统集成能力,而缺乏核心技术,70%以上的材料依靠进口。美国工程院院士程正迪教授认为,新型显示技术的突破点主要在材料,而其中很重要的一个材料就是光学膜。 “很多人认为光学膜在光学显示器里是非常小的部分,实际上液晶显示器的光学膜占到它的20%到30%的产值,而真正的液晶材料和OLED材料只占到15%到20%的比例。” 程正迪教授表示,液晶显示面板主要由六种原材料组成,包括混合液晶材料,驱动IC,偏光片,背光模组,玻璃基板,彩色滤光片。 据了解,偏光片的两大核心原材料PAC膜和TAC膜,占偏光片物料成本75%左右,目前还是依赖日本进口,其中TAC 膜全球主要由日企厂商供应,富士写真和柯尼卡美能达两家日企全球市占率分别为70%和20%,两者占据全球TAC膜市场约90%的份额,韩国国、台湾厂商包括国内的乐凯也在做TAC膜,但出货量很少。 而日企KUARARY(可乐丽)则占据了全球PVA膜市场65%。另外在偏光片的其它原材料膜层方面,日本也居于垄断地位,例如,90%以上的AG膜(防眩层)市场由日本电工和大日本印刷占据。 不管是LCD还是OLED都需要用到光学膜,但是光学膜存在的问题很多。程正迪教授表示,对于设计光学薄膜的材料来说,具有各向异性的光学性能是业内普遍的难题。此外,光学薄膜的结构还面临加工问题,比如做偏光片时会有精密涂布的过程。其中面临的挑战很多,比如是精准的分子设计、精准的结构和形态的调控、精密加工技术等。 程正迪教授表示,真正的挑战是如何实现分子单元光学协同放大。从技术研究的角度和逻辑来看,程正迪教授认为要从基础的高分子材料、到光学膜结构调控理论,再到光学膜制造、材料和成套技术工艺包。“对我们来讲真正要做到工业化生产,一定要走到这一步,也是最困难的一步。” 程正迪教授认为,只有将材料化学、材料物理、生物材料、材料工程实现跨学科合作,才能从理论和实践上来解决二维转化材料的问题。
基础研究走在前面,国内柔性显示材料取得突破
中国科学院院士、中国科学院物理研究所欧阳钟灿院士
欧阳钟灿院士则回顾了平板显示技术的发展历程,他表示液晶显示技术刚出现的时候相比CRT技术有很多缺陷。真正让液晶显示技术获得突破是从笔记本电脑开始。2005年,液晶显示概念获得了京都奖,此外液晶显示也获得了美国工程院的最高奖,被称为工程诺贝尔奖。2014年诺贝尔物理奖给了蓝光LED的发明者,2015年工程诺贝尔又给了做背光源的专家。 “液晶显示开始的时候跟等离子是进行亮度比赛,后来发明了蓝光二极管就把等离子打倒了。OLED现在提出来,它和液晶显示相比,OLED的亮度比较高,达到110%,液晶只有70%,但现在液晶加了量子点,它也达到了120%,所以你们做OLED的,在亮度方面要跟量子点比较,这是一个新的过程。”欧阳钟灿院士认为,液晶显示作为一个成功的技术案例,应该给柔性显示产业一点启发,那就是基础研究必须走在前面。欧阳钟灿院士认为,中国的显示材料大而不强,很多材料依靠进口。“我们的发光材料都是进口的,液晶材料已经比较好了。” 欧阳钟灿院士认为,柔性显示领域的材料将收到国家新的三年计划的照顾。
华南理工大学高分子光电材料与器件研究所曹镛院士
华南理工大学高分子光电材料与器件研究所曹镛院士以“华南理工大学光电所团队全印刷、柔性显示研究进展”为主题分享印刷OLED、柔性显示科技创新成果。目前华南理工大学光电所的研究工作包括:全印刷的PLED发光显示屏,基于金属氧化物的TFT驱动背板的柔性全色OLED显示屏,新型的用电化学聚合图案化实现OLED全色显示屏的新途径。 以柔性全色OLED显示屏为例,目前三星生产的OLED屏可以实现弯曲,再下一步就是要做到可卷,最后是做到可对折。曹镛院士认为,只有能做到对折才能算是真正的柔性屏。 目前类似于IphoneX的做法是在一个玻璃衬底的基础上贴在上面,从而实现弯曲。华南理工的做法则是把玻璃衬底换成金属氧化物,这样不仅面积更大,而且成本较低。可以量产相关金属氧化物的企业目前只有两家,就是夏普和LG。目前华南理工与国内的新视界公司合作,采用稀土金属来取代原来的氧化锌,与LG、夏普的量产产品相比,用稀土掺杂的金属材料可以得到比较高的迁移率。
新纶科技联合阿克伦成立聚纶,引入高端薄膜材料
这种尝试正在开始,12月11日新纶科技与阿克伦公司拟设立立合资公司聚纶材料科技(深圳)有限公司。据介绍,阿克伦公司将投入“用于液晶显示器的负性双折射聚芳醚酰亚胺薄膜技术。聚纶将作为一家以实现“资源整合”、“引智”和“育人”三大目标的高分子材料产业技术研发、孵化的功能性平台企业,以合资公司为开展技术研发合作的平台和载体,并且通过公司与高等院校开展共建联合实验室进行技术合作、自主开发、委托第三方开发或双方协商一致的其他形式的技术研发活动,获取高科技成果,并推动和实现科技成果的产业化和市场化。
美国APS公司主席哈里斯教授
对于显示材料的发展,哈里斯教授以“聚酰亚胺薄膜及其在柔性显示器中的应用”为主题分享聚酰亚胺薄膜在柔性显示应用中的发展机遇。“我认为聚酰亚胺薄膜一定会销售得非常好,因为这个技术得到了非常好的应用。特别是我刚才所讲到的S-Plate会非常贵,它的采光效果非常好,对光的要求没那么高,同时它的薄膜的尺寸会非常薄。” 哈里斯教授表示。 据介绍,APS公司在美国俄亥俄州的阿克伦,当地的阿克伦大学有高分子科学学院和聚合物工程,在俄亥俄萨米特县已经有超过360家专注聚合物的企业。APS目前可以提供的产品包括平板显示器、光学薄膜、LCD、光互联的半拨片,同时还有高抗压纤维和高膜量的薄膜。目前的柔性OLED灯都需要用到聚酰亚胺薄膜,因为需要非常高的透明度和高折射率。哈里斯教授表示,APS希望能在中国打开更多的市场,此次与新纶科技的合作也是希望尽可能将高科技技术引入中国。
上一篇:群创首创DST技术 将实现多点3D传感
下一篇:从4K到双色激光 2017五大投影技术盘点
推荐阅读最新更新时间:2024-05-03 20:12
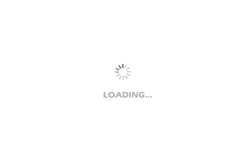