目前,随着自动化技术在工业领域的广泛应用,对传统生产流程和工作方式进行自动化改造己成为一种热门趋势。油田作为国家的重要石油生产基地大范围地进行自动化改造已成为必要的发展趋势。本文从油田联合站的数据采集自动化改造方案,结合笔者建设的实际经验,对数据采集与监控系统的构建进行了一定程度的剖析。对上位机、PLC、各种仪表的互联通信做了介绍,并以力控6.1组态软件作为组态工具进行了监控界面的组态。
油田计量数据采集与监控系统即是将自动化技术与油田生产过程相结合,以数据采集的自动化来替代传统的人员抄表、专人巡检等老旧生产方式,从而构造一个可对生产过程进行实时、精准、安全、方便监控的自动化平台,可精简冗余人员、降低生产成本,显著提升油气田的生产效益。对其他联合站、注水站的自动化改造具有指导意义。
1 系统结构
1.1 总体结构图
联合站数据采集系统是将站内各油、气、水三相分离器上压力、温度、流量传感器的采集值供PLC读取,PLC又通过交换机一方面与工控机通信,将数据显示在组态软件组态的界面之上,供站内值班人员监视与控制;另一方面将数据传输给油田服务器,服务器再以报表的形式传送给采油厂计算机,以此完成整个联合站数据的采集、接收、监视过程。油田计量数据采集与监控系统总体结构如图1。
三相分离器仪器仪表的详细架设如图2所示。
[page]
1.2 硬件结构
1.2.1 工控机
工控机即工业控制计算机,英文简称IPC。本系统采用研华工控机,其具有以下特点:
(1)机箱采用钢结构,有较强的防尘、防磁、抗冲击的能力;
(2)机箱内有专用底板,底板上有PCI和ISA插槽;
(3)机箱内有专门电源,电源有较强的抗干扰能力。
1.2.2 PLC
PLC选用的是广域科技公司的智能WAT05控制器,该PLC采用模块化的结构,运用在该系统中的有CPU模块、电源模块、模拟量输入模块、RS485通信模块。
1.2.3 仪器仪表
选择传感器最基本的要求是:抗干扰能力强,在工作范围内线性度好,并输出标准的电压或电流信号以保证和智能采集模块能很好地配合使用。同时,其必须具有良好的保护措施,以适应施工现场多油渍、多灰尘、多碰砸、多泥沙的情况。具体所使用的变送器类型及参数如表1。
2 网络结构
2.1 以太网
以太网是当前应用最普遍的局域网,它很大程度上取代了其他局域网标准,如令牌环、FDDI和ARCNET。经历100M以太网在上世纪末的飞速发展后,目前Gb以太网甚至10G以太网正在国际组织和领导企业的推动下不断拓展应用范围。
该系统中联合站内PLC通过交换机以双绞线为传输介质与服务器连接,服务器又和油田计算机相连,共同组成一个以太局域网,形成局部的星形拓扑结构。整个胜利油田又以光缆为传输介质组成大的环形拓扑的以太局域网。
2.2 MODBUS通信协议
工控机和PLC之间采用MODBUS通信协议进行串口通信,标准的MODBUS口是使用的RS232兼容串行接口。控制器能直接或经由Modem组网,通信使用主-从技术,即仅一设备(主设备)能初始化传输(查询)。其它设备(从设备)根据主设备查询提供的数据做出相应反应。典型的主设备是主机和可编程仪表,典型的从设备是PLC。
主设备可单独和从设备通信,也能以广播方式和所有从设备通信。如果单独通信,从设备返回一消息作为回应,如果是以广播方式查询的,则不作任何回应。MODBUS协议建立了主设备查询的格式:设备(或广播)地址、功能代码、所有要发送的数据、一错误检测域。
3 组态监控界面设计
3.1 组态分析
联合站内共有6个分离器,需对每个分离器上压力变送器、流量变送器、温度变送器上的采集数据进行监视。在PLC内的保持寄存器中,所有的压力数据、温度数据,放于HRU存储区域;天然气出口流量数据、低含水油流量数据、以及气的累计数据放于HRF存储区域;污水出口流量数据、污水累计数据、低含水油的累计数据放于HRD存储区域。
[page]
3.2 组态过程
(1)双击桌面力控快捷方式,进入工作界面,点新建出新建工程导航;
(2)点击开发,进入开发环境;
(3)点击导航栏中的IO设备组态,选择标准MODBUS(RTU),开始设定与PLC的连接;
(4)在导航栏中点击数据库组态,选择区域0,模拟IO变量,开始定义所有的数据变量,如图3所示,建立实时曲线如图4所示;
(5)与设备调试完成之后即可进入运行状态,建立组态现场监控界面如图5所示。
4 结语
自动化数据采集系统正朝着计算机化、标准化和网络化三大趋势发展。基于PLC的油田计量数据采集与监控系统解决了联合站无人值守的数据采集和传输问题,网络结构简单,方案可行,充分利用已有的线路资源,廉价且有效,在实际应用中发挥着一定的作用。以此为基础可进一步完善油田自动化监控系统,降低劳动强度,节约人员,提高生产效率,向建立数字化油田方向而努力。
上一篇:基于过零点检测的高分辨率DAC静态测试方法研究
下一篇:费思推出针对移动电源测试项目及测试指南
推荐阅读最新更新时间:2024-03-30 22:38
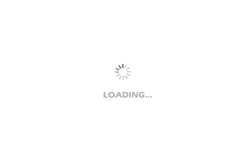
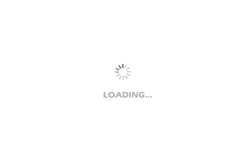
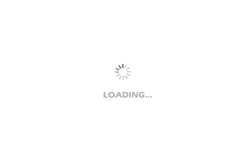
- 希润医疗孟铭强:手功能软体机器人,让脑卒中患者重获新生
- 柔灵科技陈涵:将小型、柔性的脑机接口睡眠设备,做到千家万户
- 微灵医疗李骁健:脑机接口技术正在开启意识与AI融合的新纪元
- USB Type-C® 和 USB Power Delivery:专为扩展功率范围和电池供电型系统而设计
- 景昱医疗耿东:脑机接口DBS治疗技术已实现国产替代
- 首都医科大学王长明:针对癫痫的数字疗法已进入使用阶段
- 非常见问题解答第223期:如何在没有软启动方程的情况下测量和确定软启动时序?
- 兆易创新GD25/55全系列车规级SPI NOR Flash荣获ISO 26262 ASIL D功能安全认证证书
- 新型IsoVu™ 隔离电流探头:为电流测量带来全新维度
- 英飞凌推出简化电机控制开发的ModusToolbox™电机套件