近年来,节能成为全新汽车技术和趋势的热门话题。回顾过去20年,汽车的电子化主要由驾驶者对更舒适和更豪华的设备,例如电动车窗、电动天窗和敞篷车盖、高级音响器材、电动座椅、空调或电动液压助力转向系统等的渴求所推动,这些设备全都增加了汽车对半导体及电子零件的需求。现在,电子化汽车设计的首要目标已经有所不同。虽然豪华设备和更好的驾驶功能对汽车来说仍然重要,但现在以至可见的未来,当代汽车所采用的大部分电子系统,也是以减少排放、提高燃料效率,并且降低车内系统的电力消耗为推动力。
达到这个目标的最好方法,便是使用更有效率,也更智能的电子系统去替代汽车的机械及液压系统。典型的例子有以电动转向系统替代液压或者电动液压系统;电力电机驱动替代连续运行的皮带驱动系统,就像空调压缩器、涡轮充电器,或其它的泵和风扇。即使是一些照明应用,如能够节能的“高强度气体放电灯”(HID)或LED灯,也用来代替欠缺效率的传统灯泡。最终,内燃引擎亦将会由具效率的电动电机所取代,就像我们现在于混合动力和电动汽车的动力系统所看到的一样。
汽车电子化也使国际整流器公司(IR)这些半导体供应商以开发高效率的电源管理解决方案为己任,从而尽量提高这些应用的能源效益。IR先进的电源管理解决方案结合了非常先进的硅技术及革命性的新封装技术,能够同时改善汽车系统的性能和耐用性。特别是在封装方面,我们为系统设计师带来创新解决方案,以及设计ECU、电机驱动和电源的新方法。
现今的硅技术实现了非常好的开关,例如最新的沟道MOSFET和IGBT。不过,相关的封装技术经常利用十分保守的焊接方法把硅芯片装贴到基片或铅框架,并且以键合线连接其表面。早在2002年,IR已经开始发展新的连接界面,希望通过简单的封装,就能把我们最好的硅技术连接到电力电路,还把电流和热流的界面减到最少。最终的成果是,我们开发出免除键合线的DirectFET技术。这种技术的实现有赖于硅开关的正面金属可焊,以便使由简单金属外壳包围的MOSFET 可直接焊接到印刷电路板。图1和图2所展示的概念主要是设计简单、尽量减少物料和界面,最特别的是无需再用键合线去达到最好的电力和温度性能。此外,这个概念也能够提高汽车系统的质量和可靠性,因为它消除了汽车功率周期中的主导失效模式:也就是所谓的键合线脱离。
图2:DirectFET的横切面:硅芯片的温度和电力接口尽量缩小尺寸,同时电力和温度性能也远远超出采用键合线的标准封装。
直接封装概念非常适合同时要求卓越性能、质量、耐用性和长久可靠性的汽车应用。与此同时,IR优化了DirectFET概念,结果造就了我们在今年初推出、全面汽车认可的DirectFET2产品线。有关的汽车芯片由一个小外壳包围,让的客户可以为其电子控制单元和功率级引入非常创新的设计概念。这些 DirectFET2开关能够通过不同的方法散热,包括从器件的上方散热,免除了组件要通过PCB,甚至利用ECU外壳两侧进行冷却的需要,也不用藉着在 ECU设计里的其它散热部分来降低温度。客户因而可生产专有的系统解决方案,从而在其它采用标准封装零件和键合线的竞争对中脱颖而出。
图3:汽车用DirectFET2的各种创新散热方法选择
IR 将其无键合线策略伸延到所有汽车用的功率开关。其最新一代的IGBT也具备IR专有的正面金属可焊技术,提供完全没有键合线的芯片连接,也为采用IGBT 和二极管的高电压系统实现了双面散热概念。据我所知,IR是首家以裸芯片搭配正面金属可焊技术来推出商用汽车认可IGBT的公司,使拥有硅处理能力的客户可以建立和设计它们自己的双面散热无键合线功率模块或功率级。有了IR的正面金属可焊器件,平常无法接触专有硅技术的系统设计师,现在也可享受“无线汽车电源管理”的世界。
除了裸芯片,IR亦将提供专有的芯片载体解决方案。该方案附有正面金属可焊IGBT,来支持那些生产线没有能力处理裸芯片的客户。最先进的高性能IGBT是以非常纤薄的晶圆制造,厚度仅为60到70微米。这些硅晶圆既薄且具弹性,就如纸张一样,所以必须使用极为专业的程序和昂贵的器材去处理。很多第一级和第二级的系统供应商都不愿意投资这种昂贵的器材,也不想经历需要长久学习才会熟练的纤薄芯片处理过程,更不希望要承受薄芯片处理期间非常高的良率耗损。[page]
IR推出的这种贴在专有芯片载体上的新款汽车功率开关将会把上述顾虑一扫而空。我们将提供预先贴上IR大型芯片(IGBT及MOSFET)的标准化专有芯片载体。它们随后会成为客户电源模块的一部分,比方说,我们的DirectFET2金属外壳变成PCB电路的一部分,并且让每一个人都可以利用最精密的IGBT和薄芯片,而不用使用薄芯片器材。IR作为硅技术专家,将负责最困难的部分,也就是把薄芯片制成基片的制造过程,还有在裸芯片和晶圆层面的开关最后测试,都会一一解决。只要利用IR的汽车用正面金属可焊产品线,即使标准的安装机械和焊接器材也将足以应付非常先进的功率模块或ECU概念。
对我们的客户和系统设计师来说,新器件的最大好处并不单单在电力性能上的改进,更好的开关效能、经过优化的双面散热 (我们能够增加最少50%的整体热交换面积、减少35%的RthJC,以及提高大约25%的硅电流密度),还有简单的制造过程都是重要的优点。另一个非凡的效益,将在与应用相关的系统布置和应用尺寸,以及在汽车的寿命要求层面上实现。当键合线在相对耐用的DBC模块中或功率周期压力中的首个失效模式中脱离,采用IR专有正面金属可焊技术的无键合线IGBT将有机会将功率周期能力延展一个量级。
图4展示了IR正在运行的功率周期测试。这个测试针是针对一个客户的定制IGBT系统,将在几个10,000温度周期后发生的键合线脱离故障,与使用无键合线系统进行相同持续周期测试所得的结果作出比较,可以看到结果显示出极大的分别。借助大幅度的可靠性延展,功率周期能效系统设计师便能缩小他们的功率级尺寸。
图4:在专有客户陶瓷封装中,键合线IGBT与无键合线双面焊接IGBT的功率周期能效比较。上面两个图表显示不同的温度压力状况,每一条色带代表测试中的各个独立器件。
为了避免在实际应用中过早出现键合线脱离故障,设计师通常会采用昂贵的基片和散热器方式,再加上过大尺寸的功率开关来降低每个功率周期的Delta-T温度摆动。相较而言,一个无键合线系统的芯片尺寸可以大幅减小,同时系统能够在更严苛的周期条件下运作更长时间。这表明,汽车中的逆变器、直流-直流转换器和其它电源管理应用得以通过正面金属可焊器件显著降低系统成本。设计师因而可以在性能、可靠性等多方面取得改善。
为了帮助系统设计师以适当的控制IC来完成整个功率级开发工作,IR提供了多款汽车用驱动器IC选择,可满足先进逆变器、转换器、电源拓扑和系统要求。我们专有的汽车用高/低电压栅极驱动器拥有卓越的耐用性和闭锁抗扰性。在低于75V的电压范围内,设计可基于专有智能功率程序操控驱动器,实现非常大的电流开关。当电压介于100V到 1,200V之间时,IR也提供了一个极高电压接口隔离驱动器IC系列,该系列配备市场领先的负瞬态电压尖峰安全操作区 (NTSOA) 。IC的失效模式,通常由于采用大电流电感负载实现开关半桥,因而造成大的负电压尖峰,被称为闭锁效应。这些IC都是以耐用性和闭锁抗扰性为目标来设计,是驱动拥有极高电流密度的大型IGBT(诸如正面金属可焊器件)的最佳选择。如果系统设计师需要更大的驱动电流,也可利用器件所提供的缓冲IC来提供最大 10A电流的能力。
总之,IR提供一系列的器件,让汽车功率系统设计师可以为非常先进的“无线”电源管理选择完整的芯片组,从而支持未来汽车的能源效益,即使要在最严苛的环境中完成最艰难的开关任务,这些器件也可应付自如。
上一篇:SD卡在记录汽车CAN总线数据中的应用
下一篇:电子燃油喷射系统的分析与检测
推荐阅读最新更新时间:2024-05-02 21:29
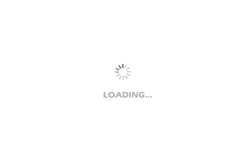
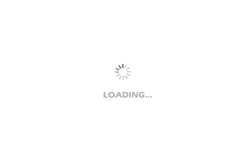
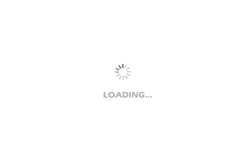
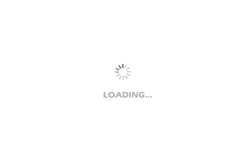
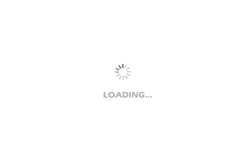
- Allegro MicroSystems 在 2024 年德国慕尼黑电子展上推出先进的磁性和电感式位置感测解决方案
- 左手车钥匙,右手活体检测雷达,UWB上车势在必行!
- 狂飙十年,国产CIS挤上牌桌
- 神盾短刀电池+雷神EM-i超级电混,吉利新能源甩出了两张“王炸”
- 浅谈功能安全之故障(fault),错误(error),失效(failure)
- 智能汽车2.0周期,这几大核心产业链迎来重大机会!
- 美日研发新型电池,宁德时代面临挑战?中国新能源电池产业如何应对?
- Rambus推出业界首款HBM 4控制器IP:背后有哪些技术细节?
- 村田推出高精度汽车用6轴惯性传感器
- 福特获得预充电报警专利 有助于节约成本和应对紧急情况