“机器视觉”的用途很多,随着20世纪90年代以来光电、自动化和计算机图像处理技术的迅速发展,机器视觉已在包括汽车制造业在内的很多工业部门得到越来越广泛的应用。作为一种新颖而又实用的传感技术,图像检测单元近年已实现产品化,一些知名的厂商,如日本的松下公司、德国的西门子公司等都推出了品种规格齐全的系列化产品,包括光源、摄像头、处理器等,对图像检测技术的推广应用创造了有利的条件。与此同时,所颁布的相关标准不但规范了生产,而且为用户在不同情形下选用合适的检测单元,更快、更好地进行系统设计提供了依据。
相比之下,国内在这方面尚处于起步阶段,即使在近20年获得迅速发展的汽车制造业,机器视觉的应用也相当有限。但通过以下应用实例,可清楚地看出这项新技术的应用前景。
在精密测量中的应用
图1 位移检测系统示意图
精密测量是机器视觉一个重要的应用领域,其对被测对象进行测量的原理如图1所示。检测系统主要由光学系统、CCD摄像头和计算机处理系统(图中未表示)等组成。由光源发出的平行光束照射到被测对象的检测部位上,其边缘轮廓经过显微光学镜组成像在摄像机的面阵CCD像面上,经计算机进行图像处理后获得被测对象边缘轮廓的位置。如果使被测对象产生位移,再次测量其边缘轮廓位置,则两次位置之差便是位移量。显然,若被测对象的两条平行的边缘轮廓能处于同一幅图像内,则其二者位置之差即为相应尺寸。
上述系统极为适合对大批量生产情况下工件的在线检测,尤其是当被测对象尺寸较小、形状比较简单时,更能显示其优越性。电子接插件,包括汽车电子产品中的接插件就是典型例子,它们的生产效率和成品尺寸精度都较高,前者可达到每分钟数百件,而后者多数为0.01mm的数量级。当采用图1所示系统进行测量时,零件(插脚)所形成的图像由于与其明亮背景之间的强烈对比,而具有清晰的剪影效果。这样的理想图像为准确测量被检对象的尺寸和轮廓(形状)特征创造了条件。图2显示了一部分冲压成形的插脚随着金属输送带通过检测工位时产生的典型背光图像。
需指出的一点是,尽管采用的是对零件图像的边缘检测,但根据工件的不同情况,具体做法上仍有差别。如对图2所示零件(插脚)的图像上可以设置3条(L1、L2、L3)或多条检测线,分别采用简单的阀值法或单双峰法检测出零件的边缘信息。由于3条检测线之间保持着相互垂直交叉的关系,因此可以通过联立3线(或多线)的边缘检测点确定插脚相对于图像平面的位置(X、Y)和转角(?)。这些目标零件的位置信息(边缘坐标和起始转角)将传送给计算机处理系统,以做出相应的评价。
图像检测技术用于精密测量的另一个实例是在刀具预调测量中的应用。传统的检测方式是光学投影和光栅数显表相结合,前者用于瞄准定位,后者用于测量、读数。整个过程需较多的人工参与,对操作人员的要求高,效率却较低。几年前诞生的新颖刀具预调测量仪把机器视觉、光栅技术、计算机软硬件、自动控制技术等有机结合,使传统的工作方式发生了根本变化,无论在测量精度、操作方便和工作效率上都有了极大的提高。而主要原因就是以机器视觉替代了传统的光学投影,从而彻底改变了原有的工作模式。
在这种新颖仪器中,作为运动导轨的Z轴、X轴和C(回转)轴内,分别装有直线光栅和圆光栅,被测刀具沿转台中心线(即C轴)0安装。机器视觉传感器位于叉形支架两侧,也就是跨越转台的中心线。支架的一端安放光源,而另一端是摄像头,被测刀具的图像由摄像头读取。
对工件表面缺陷的检测
对表面缺陷的探测在批量生产的汽车、摩托车、内燃机等行业,迄今基本都采用人工目测方法。这样的方法不但效率低、劳动强度大,且对工艺标准中规定的定量评定要求往往难以准确执行,从而影响对产品质量的有效监控。
[page]
以连杆结合面爆口为例,其评定标准的具体要求是:破口面积小于3mm2;破口任一方向的线性长度小于2.5mm。只要符合上述任一条件,就将判定不合格而被剔除。
必须指出,与以上精密测量中机器视觉系统采用的透射方式(又称“背光” 方式)不同,用于表面缺陷探测时,需采取图3所示的反射方式。
该系统通过一个方形框式LED漫反射光源照亮待检测工件的破口区域,光线照射到对象表面后,反射到摄像头内的光电耦合CCD元件上,即转化成对应的电量信号;图像处理系统根据电量信号对得到的图像进行分析和计算,最终得到所需的数据。系统将得到的图像进行二值化处理后,把二值图像作为对象进行进一步的计算分析。
在实际使用中,该系统对于灰度的二值化阈值和光源的设定采用比对的方法实现,即用已知的样件作为标定的参照物。把已知的参照物测量
值除以参照物对应的像素值,即可得到像素与实际值之间的对应比例值。通过调整光源亮度以及系统的二值化阈值,对灰度的二值化阈值进行优化,保证系统对对象边界具有相对较高的分辨率,即优化后的二值化阈值和光源可以使边界的变化产生尽量大的像素值变化。
根据被测对象的特征(工件形状、被测部位)和要求,参照视觉系统产品的有关标准,并按照所完成的设计,将能方便地选取合适的图像检测单元(器件),组成相应的检测系统。以连杆结合面爆口为例,其系统的检测要求如图4所示,即分别检测互为15。夹角的A-B-C三个(连杆侧面的)破口面,最终以3个检测结果中的最大值作为破口的真实值,进行判断后并输出结果。图5为该系统组成示意图,其中:
1. CD摄像头用于采集破口图像并转换成数字图像信号;
2. LED光源用于提供稳定的、均匀的照明,保证取像质量;
3.图像处理单元的用途是根据需要对采集到的图像进行处理、分析,同时把分析结果和图像系统的状态信息通过RS232接口传向PLC提供信号输出和数据交换;
4.PLC控制整个检测系统各项功能的执行,同时也对图像处理单元传过来的数据进行校验和判断;
5. 监示器作为人机交互界面,显示图像处理系统的状态和数据分析结果。
在汽车制造业中的应用
用于图像识别的机器视觉系统的检测原理虽然与以上表面缺陷探测相似,但作用、目的完全不同。且相比之下,即使在国内汽车制造业中的应用也较前两个领域为多。
.
现代工业则已越来越多地采取让最终产品、甚至半成品(零部件)带有用于识别的一维、二维条码。在大批量生产条件下,如何对它们识别、判断?若依靠人工肉眼检查,不但劳动强度大,也难免错检漏判。另一方面,在生产线、特别是其中那些装配工序的运行中,为正确完成规定的要求,往往也需解读一维、二维条码或识别某些印刷字体;此外,很多情况下,对零件的姿态、位置(方向)也必须进行辨识,特别在采用选择装配方式时。电子标签也是近年发展起来的一项新技术,它采用机器视觉的识别技术,将涉及发动机的各种质量信息通过读写器无线写入标签或读出。在有些发动机生产线的输送装置(托盘)上安装有一个电子标签,而每个加工或装配工位则布置有一个读写器。读写器与PLC或计算机相连。
1. 活塞在缸体内的装配
图像识别技术在用于“活塞—缸体装配工序”时,其主要环节包括:判断缸体到位并做好检测准备;探测缸体上缘(准确到位的标志),如果未发现该特征部分,即发出报警信号;在检测系统中建立坐标系;识别这样三项内容:活塞的有无,活塞位置的正确性(确切地讲
是“方位”),活塞顶部表面的标识和字符——用于表明型号、选择装配时的组别及其他相关含义。
整个检测、识别过程如下:发动机被翻转、装入活塞,输送系统使发动机随托盘向检测工位移动;当发动机即将到达检测工位时,由电子标签读写器验明其“身份”,然后发信号给PLC;而当发动机到达检测工位,接近开关触发,PLC给机器视觉系统发出工作指令;如果活塞在缸体内的装配正确,视觉系统发信给PLC,然后写入电子标签,发动机继续流向下一工位。如果活塞装配有错,则视觉系统提示PLC,并通过人机界面报警,显示屏将指示哪一缸的活塞装配有错、何种错误。操作者确认检测结果后,通过使人机界面PLC发出指令将结果写入电子标签,并且将发动机直接输送到返修区域进行返修。整个检测过程全部自动完成,只是在出现装配错误、发出报警时才由人工干预。
2.主轴承盖在缸体上的装配
在四缸发动机的缸体生产线,主轴承盖在缸体上的装配是又一个典型示例。5个主轴承盖的前端部呈不同的台阶状,各不相同。通过每个零件上的数字标识,按规定顺序和方向安装。由于零件混杂、数量又大,常发生错装现象,导致下道工序产生废品。
为此,在生产线的拧紧装配工位和翻转工位之间设置一检测工位,通过自动识别,判断装配结果的正确性。若全部正确,则缸体继续流向下一工位,否则报警并给PLC发出指令,使生产线停机,将有问题的缸体下线返修。为了适应1件/min的装配节拍,采用在缸体移动过程中检测,2个光电视觉传感器分别前后布置在生产线的上方和一侧。前一个为零件定位传感器,用以自动准确地触发采样,后一个用于动态识别5个主轴承盖的表面几何形状。根据预先置入的各主轴承盖特征参数和采集到的传感器输出信号,可确定是否装错并指示具体出错位置。
整个检测、识别过程为:缸体在完成主轴承盖的拧紧工序后,沿辊道向检测工位移动,而两侧导轨的约束作用,保证了零件自动找正位置。当进入检测工位时,定位传感器首先探测到第1主轴承盖边缘,随即由另一个传感器识别其前端部的几何形状,经控制器采样、处理;然后缸体继续前移,对第2至第5个主轴承盖进行探测和识别。通过与预置值比较,就可对有否错装零件做出判断。每次探测都有计数和显示,整个检测过程在缸体输送移动中完成,不必额外增加检测时间。
上一篇:基于Sitsang平台的汽车黑匣子开发
下一篇:"新捷达"型汽车组合仪表的串行通讯的实现
推荐阅读最新更新时间:2024-05-02 22:14
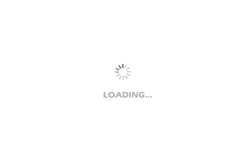
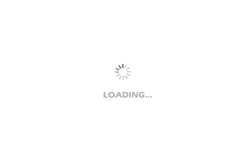
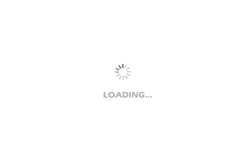
- Allegro MicroSystems 在 2024 年德国慕尼黑电子展上推出先进的磁性和电感式位置感测解决方案
- 左手车钥匙,右手活体检测雷达,UWB上车势在必行!
- 狂飙十年,国产CIS挤上牌桌
- 神盾短刀电池+雷神EM-i超级电混,吉利新能源甩出了两张“王炸”
- 浅谈功能安全之故障(fault),错误(error),失效(failure)
- 智能汽车2.0周期,这几大核心产业链迎来重大机会!
- 美日研发新型电池,宁德时代面临挑战?中国新能源电池产业如何应对?
- Rambus推出业界首款HBM 4控制器IP:背后有哪些技术细节?
- 村田推出高精度汽车用6轴惯性传感器
- 福特获得预充电报警专利 有助于节约成本和应对紧急情况