基于对更高安全性,例如防抱死(ABS)系统和气囊;更佳的操作性能,例如引擎控制和自动换档;以及更高的舒适度(如采用自动空调和座椅调节)需求的增长,汽车中集成了更多的电子控制器件,而且这一趋势愈演愈烈。
在各种工业应用中,电子控制电路的复杂性也提出了日益严格的要求,这使得EMC这种一个电子设备的运行对另一个设备功能的影响变得至关重要。
图1:SOI晶圆的横截面。 |
如今,越来越多的厂商通过CAN数据总线将电子控制设备集成到汽车及其他领域。该总线的EMC性能通常由网络节点和传输媒介间接口所采用的CAN收发器IC决定。现在,采用创新的“A-BCD”SOI技术,飞利浦推出了EMC性能得到极大改善的CAN收发器模块。
飞利浦引领SOI智能功率BCD技术潮流,目前在该领域已推出超过5亿个产品,大多面向汽车应用。“A-BCD”技术在一颗芯片上集成了双极、CMOS和高压DMOS晶体管,能够实现复杂混合信号SoC设计。“SOI”是“绝缘体上硅芯片”的缩略语,充分表达了该半导体工艺的独特性能:与传统技术不同,这种工艺是在硅基板和实际有效硅层之间放一个厚度为1微米的氧化物埋层(如图1所示),利用氧化物埋层可以完全隔离芯片上所有的元器件。
SOI保证EMC性能的优化
隔离所有的元器件能极大地降低寄生电容。因此,与传统工艺相比,SOI技术可以更简便地实现芯片设计。这是由于传统工艺的寄生效应只能通过建模来预测,而且实现难度大,因而不得不采用耗时的、反复的实验工艺。
最为重要的是,这是有史以来的第一次,采用SOI工艺,IC设计者可以同时独立地优化收发器的抗干扰性及辐射性能,从而开辟了新天地。比较而言,传统工艺的设计限制意味着在辐射优化和抗干扰优化之间必需要进行妥协。而采用SOI技术,这种双重妥协就会成为历史。[page]
图2:容错低速CAN收发器TJA1054(SOI)和TJA1053的辐射对比。 |
飞利浦通过其TJA1050成功验证了SOI工艺在高速CAN收发器中的可用性。与采用传统技术生产的PCA82C250产品相比,极大地降低了辐射,甚至可能同时大幅提高抗干扰性。TJA1040、TJA1041和TJA1041A进一步扩展了采用SOI技术的高速CAN系列产品,提供低功率模式和附加特性。
基于网络架构,SOI工艺第一次实现了避免使用至今仍广泛采用的电抗线圈。这就节约了元器件成本,简化了电路板装配,并提高了控制电子元器件的机械负载能力。
SOI和A-BCD3技术前景无限
除了卓越的EMC性能和简便设计外,SOI工艺还拥有诸多其他的显著优势。例如,较之传统的结点绝缘工艺,其封装密度可降低20%到30%,因而缩小了芯片的表面积。此外,掩膜数量的减少能简化工艺,缩短上市时间,降低成本。此外,SOI工艺能提供固有的、强劲的抗电压脉冲性能,而且Rds(on) 值可降低20%左右,因此能将功率元器件和小信号模拟及密集的CMOS有源器件直接集成在单个硅芯片上。最后,隔离氧化物埋层能减少泄漏电流,可在高于150°C的温度下工作。在某种意义上,SOI工艺是集成总线收发器、电源和逻辑的理想选择,这种技术将日益得到广泛部署,例如在汽车的局域互联网络(LIN)子总线的从动节点以及故障安全系统基础芯片等领域。
为了支持下一代SoC应用,飞利浦目前正在力推其第三代A-BCD3 SOI技术。这种通用0.6微米SOI BCD技术包含单个多晶硅栅层及3个金属层,具有120V电压处理能力,完全适用于下一代42V电池供电系统。器件被做在位于一个1微米氧化物埋层上的厚度为1.5微米的硅器件层上,其间用氧化物和多晶硅填充的沟道隔离。与结点绝缘工艺相比,在所有器件间都进行小沟道隔离能将小信号模拟电路的面积缩小50%。
A-BCD3工艺包含诸多有源/无源器件,包括:5V CMOS、同类产品中Rds(on) 值最佳的12到120V DMOS器件(如图4所示)、18V NPN和PNP双极晶体管、60V结点FET晶体管、9V齐纳管以及各种晶体管和低/高压电容器。此外,还包括RAM和ROM存储器、用于进行修改和识别的非易失性EEPROM存储器及中型程序存储器。
该工艺有两种金属化方法可供选择,其一是采用一个能实现密集数字CMOS(每平方微米4500栅)的第三金属层,其二是采用3 微米厚的第三金属层,用于将金属对功率器件总电阻的影响降至最小,实现高电流功率布线。合适的器件设计确实能进一步实现在有源器件上的布线,显著削减布线费用。SOI技术及金属层下面的钛氮化合物隔离层能够支持温度高达200°C的汽车应用。
飞利浦半导体正在推出的LIN I/O从动器件UJA1023就具备了基于A-BCD3技术的SoC性能。这是一个自主的LIN从动系统,无需添加微控制器或软件。它集成了一个LIN 2.0收发器、8个独立的可配置I/O引脚以及集成的模数转换器,并可通过LIN总线进行编程。由于采用了A-BCD3技术,LIN I/O从动装置可直接由电源供电。
A-BCD3技术发挥关键作用的另一领域是故障安全系统基础芯片(SBC)系列产品UJA106x。该系列将LIN、高速CAN及容错CAN等各种物理层与电压调节监视器、片上振荡器及SPI接口集成在一起。基于密集数字功能,状态机可与每个故障安全SBC集成在一起,以设计出真正的故障安全系统。故障安全性能意味着一旦电子控制单元(ECU)发生故障,故障安全SBC会将ECU置于最低功耗模式,以防止耗尽电池电量。此外,产生故障的ECU将不再与总线进行通信,以保证总线和其他ECU的通信继续进行。
A-BCD3这种下一代SOI能将系统功能集成到一颗可靠的单片电路芯片中。
结论
飞利浦半导体的SOI技术已被证实是用于汽车车内网络收发器的理想技术。高压元器件和低泄漏电流相结合能够实现具有卓越EMC性能的耐用设计。正是这些高压元器件使得设计出的收发器既能用12V电池驱动,也能在24V及42V电压下运作。因此,模块的设计适用于卡车和客车,而42V电压驱动被期望用于诸如电子控制悬架等高功耗应用。
A-BCD技术除具有卓越的模拟性能外,还具有密集数字工艺功能,能实现数字功能的高度集成。模拟和数字功能的结合为未来提供了新的可能。EUC设计的进一步集成可以节省空间并降低系统成本。此外,收发器、电压调节器、监视器、振荡器及SPI接口等通用ECU功能的巧妙集成能创建更加可靠且故障安全的车内网络。随着未来汽车车内网络节点数量的不断增加,这一功能变得日益重要。因为一个节点发生故障就会阻碍总线通信,而且停车时电池电量也会很快耗完。
诸如故障安全系统基础芯片和LIN I/O从动装置等最初的集成步骤已经完成。这当然不是最终的集成,事实上只是迈向未来的初级阶段,而且这将决定车内网络收发器的发展路线。这一路线图将继续在LIN和CAN中采用独立的收发器。同时,故障安全系统基础芯片和集成的LIN I/O从动装置等集成解决方案有待进一步开发。
上一篇:在一个稳固的基础上高效的开发汽车诊断功能
下一篇:如何选择汽车电子系统中的处理器
推荐阅读最新更新时间:2024-05-02 22:27
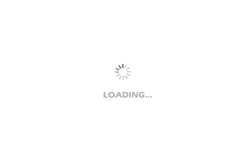
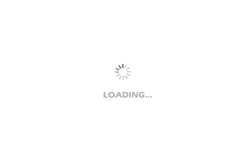
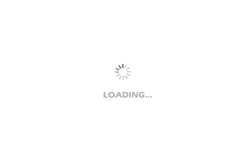
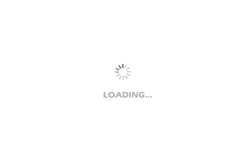
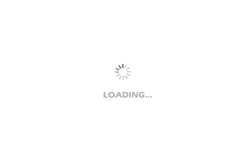