许多早期的汽车电子系统属于定制型产品,不但非常复杂而且成本高昂,即便是最新的设计也无法满足不同供应商(一级供应商)和汽车制造商的广泛需求。
本文旨在探讨LED照明系统中的这一重要元件,指出在开发LED外灯驱动电子架构时需要考虑的因素。文章将简要说明在汽车外部照明应用中使用LED灯的原因(如使用寿命长、功耗低),同时讨论在这些应用中引入LED灯所面临的挑战,其中包括行业要求(AEC-Q100)和功能要求。
在此基础上,我们将深入研究这些应用要求对电子器件的影响,以便充分挖掘LED灯的巨大潜力。我们将提出一种通用型LED照明系统架构,同时列出电子控制装置所要求的特性。这些特性包括LED散热管理、灵活地驱动不同LED配置以及具有成本优势的系统设计等。
文章最后将提出一种完全集成、灵活的汽车LED驱动IC解决方案,不但能满足汽车外部照明应用的各种要求,同时还能克服现有电子器件设计存在的诸多不足。
发光二极管(LED)在汽车领域的应用已超过15年。过去,可提供的色彩和功率水平将LED的应用限制在仪表板、内部灯饰和一些低功耗的尾灯混合照明功能。但近年来,随着LED性能的不断提升,LED逐渐在一些前部车外照明应用中得到使用,如日间行驶灯和头灯。
LED灯在这些汽车前部照明应用中得到日益广泛的使用,其主要原因在于:相对于常规白炽灯或高亮度放电(HID)灯,LED灯在款式和设计方面具有独到的优势,近期则更是得益于低功耗这一特性。
但是,同样重要的是随着LED技术的不断发展,已经可以提供更高的功率水平和更宽的色域。目前,在汽车前部照明应用中,LED灯的性能已不亚于白炽灯。
为什么在汽车照明中采用LED?
对于汽车制造商来说,款式上的优势仍然是使用LED灯的主要原因之一。显然,汽车制造商看到了进一步巩固其汽车品牌的机会。已有多种照明设计从LED灯提供的更大设计自由度中受益。较为著名的早期案例包括奥迪A8/A6。
不过,关注点正在向LED灯对汽车照明应用带来的其他优势上转移。其中包括更低的功耗、更长的使用寿命和更快的启动时间。
密歇根大学运输研究学院(UMTRI)在2008年发布了一份报告,评估了常规白炽灯和LED解决方案在白天行驶照明功能的能耗水平。他们发现,对于等效功能,LED解决方案的能耗水平要低50%(23W对46W)。这种节省可以直接转换成燃油效率,同时还能使客车的二氧化碳排放量减少50%。
对于准备开发全电动汽车的汽车制造商来说,这种燃油效率十分重要。而对于消费者来说,一个重要的购买标准是电动汽车在充满电的情况下能行驶的距离。为此,汽车制造商们正在寻找适当的方式,以改善各种功能的能耗水平,从而提高汽车的续航能力。LED灯显然具有极大的节能优势,因而日益成为照明设计工程师们的自然选择。
另一个对LED效率的提升以及LED在汽车照明应用领域的渗透做出了不可磨灭的贡献的重要因素是LED的照明效率,即每瓦特的流明(lm/W)。该指标衡量的是LED灯每消耗一瓦特能量所产生的光输出量。该值越高,LED将输入功率转换为光输出的效率就越高。如今的高亮度LED灯能实现100-150lm/W的照明效率,而一只60W白炽灯仅为10-18lm/W。
这项指标的改进极大地扩大了LED灯的应用范围,并拓展到完全以LED灯为基础的汽车前部照明系统之中。尤其是完全以LED为基础的大灯,其中包括远光和近光调整等功能。下一节将介绍在汽车应用中使用LED灯所面临的部分挑战。
LED在汽车应用领域面临的挑战
汽车环境为LED带来了巨大的挑战,LED必须能提供稳定的光输出,即使大灯周围的电气条件和散热条件不断变化,灯光的通量和色点也必须保持恒定。
由于LED的光输出与应用于LED的电流成比例,同时,LED采用的是扩散式生产工艺,因此即使是同一批次的产品,也可能在驱动电流相同的情况下,其光输出存在差异。为了避免这种不利差异,往往根据某些参数(如正向电压、通量输出)来选择LED(也称"筛选")。通过筛选,可以确保同一批次的LED在光输出和色点方面更加一致。
LED还必须保证在-40℃至+125℃的环境温度范围内,光输出达到具体应用的最低法定光通量要求。头灯的光通量需要达到1,000流明左右,并能在工作温度范围内提供要求的最低光输出。
为了达到这种光通量要求,可能要将数个LED串联或并联起来。将多个高亮度LED灯集合到一起同时对散热管理提出了很高的要求,因为随着LED温度的升高,LED的光输出会大幅下降,色点会发生偏移。因此,LED在产生这种量级的光的过程中散发的热量必须通过散热器传导出去。在一些极端情况下,可能需要降低LED的驱动电流,以避免LED过热和损毁。 [page]
汽车工业对LED的可靠性同样提出了严格的要求。LED解决方案必须能够达到AEC-Q100标准的严格要求。这就意味着,LED及驱动器电子器件必须通过该标准的认证。
此外,汽车制造商以及一级照明产品供应商提出了其他的功能要求,比如利用LED来提供双重功能,举例来说,日间行驶灯有时充当停车灯,尾灯有时用作停止灯。这就意味着,LED提供的光必须具有两个可以控制的输出水平。为了避免不同电流水平下的色点偏移,多数系统设计通过对LED电流进行一种脉冲宽度调制(PWM)处理,以减少LED的平均电流,同时还能使峰值电流维持恒定。这样在相同的色点下,可以实现较低的光输出水平。
LED对电子系统架构的影响
实际上,LED的诸多功能和优势取决于用于驱动它们的电子器件。电子驱动器解决方案会对LED以及整个系统的效率和性能产生巨大影响。
图1所示为一种针对外部LED灯的通用型LED照明系统架构。图中显示了用于驱动LED的一种通用照明控制模块(LCM)的主要组件。虽然有些架构的LED与驱动器电子器件位于同一模块上,但本方案的LED设于驱动器控制模块的一个独立LED模块上。
图1:一种通用型汽车LED照明系统架构
为了识别LED的批次,通常要采用一个筛选电阻或编码电阻。通过测量该电阻的值,LCM可以确定应向LED提供的确切电流量,以确保达到具体功能的光输出要求。
LCM从车身控制模块接收功率和控制信号。其中往往包括用于提供动力的电池和地电源。有些架构含有来自车身控制模块的一条控制线路,通过其中的控制信号来改变LED串的功能。例如,当用同一LED串来充当日间行驶灯和停车灯时,就需要控制信号来选择所需功能。更先进的架构采用CAN网络来控制照明,因而采用一条CAN总线电缆来确定具体功能。
为了对来自LED模块和车身控制器的这些控制信号进行处理,LCM有时会采用一个微控制器。该微控制器可以读取这些控制信号,并对驱动器IC进行相应的配置。这有利于增加LCM的灵活性,使其可以驱动任意LED配置,从而提高驱动器控制板在不同汽车平台中的重复利用价值。
驱动器电路本身的主要功能是为LED串提供受控电流。该电路可以采用不同的架构,比如线性调节器或开关调节器。然而,随着功率水平的增加,效率变得越来越重要,因而通常采用开关调节器。这些转换器可以采用升压、降压或降压/升压拓扑结构。每种拓扑结构都有其自身的优势和不足,与输出灵活性、效率和系统成本相关,具体应用取决于具体设计。
在确定采用哪种拓扑结构时,必须考虑以下事实:电池向LCM提供的电源电压的变化范围非常大,低至6V(现代起止发动机的冷启动),高达24V。就如多数汽车制造商坚持的那样,在这些条件下,外部照明功能应能正常运行,因此,驱动器电路必须能在如此宽的输入电压范围内向LED串提供相应的输出电压/电流,以驱动LED。在这些要求下,经常采用降压/升压拓扑结构。
另外,随着照明控制模块向通用型不断发展,降压/升压转换器拓扑结构成了首要选择,因为这种结构在输出电压方面具有最大的灵活性,不受输入电压影响,有效地弥补了不同拓扑结构在效率方面的微小差异。
如前所述,LCM为LED提供PWM电流。然而,为了避免该PWM电流使LED光发生肉眼可见的闪烁,一般采用200Hz以上的PWM频率。PWM占空比也可以发生变化,以根据所需功能(如日间行驶灯或停车灯)向LED串提供不同的平均电流。
可见,灯光控制模块必须能将来自车身控制器的输入功率转换成频率超过200Hz且具有相应占空比的PWM电流,以便向LED提供适当的平均电流,从而实现所需要的功能。
采用DC/DC开关调节器拓扑结构同样需要确保控制模块不辐射且不受电磁干扰。因此,需要采用正确的电子器件设计和电路板布局,以避免这种干扰。
在图1的示意图中,LED与驱动器控制模块相互独立,二者由一个连接器相连。这种架构要求对LED进行保护,防止其电池或地引脚因连接器故障而意外短路,从而避免LED和驱动器电路遭到损坏。[page]
除了短路条件以外,LCM还需具备检测LED故障的能力。其中包括检测LED的开路故障和短路故障。LED串中的单个LED发生开路故障时,检测起来相对容易,但短路故障的检测更具挑战性。单个LED正向电压的内在扩散性在较长LED串中积聚时,会变得非常明显。这增加了检测短路发生时间的难度。当LCM检测到故障LED时,可能同时需要将诊断信号发回车身控制模块,以便提醒驾驶员。
这就需要采用灯光控制模块,以便提供所有上述功能,同时达到汽车工业标准的严格要求。这就意味着,该模块和相关组件必须通过符合AEC-Q100标准的汽车认证。汽车照明被认为是一种事关安全的重要功能,因此,其可靠性是重中之重。
驱动器IC解决方案
从上述各项要求可以看出,挑战在于如何设计一种解决方案,能在降低系统成本的同时提供所需的功能、灵活性、系统可靠性和集成度。
一种可能的解决方案是采用恩智浦半导体提供的ASL1010PTK驱动器IC。ASL1010PTK驱动器IC集成了汽车LED灯必需的核心功能,是一种紧凑型一体化解决方案,且无需增添额外部件。对于LED模块设计而言,有利于降低成本、增强美感、提高可靠性。
此外,这一系统解决方案具有极高的灵活性,不受汽车平台和LED配置的限制,而且无需重新设计PCB电路板。集成式设计免除了不同平台的冗余功能以及对外置微控制器的需要,从而将系统成本控制在较低水平。
ASL1010PTK驱动器IC采用降压/升压拓扑结构,利用标准汽车电池电压即可安全驱动多达20个LED灯;输出电压极其灵活,范围为6V至60V,支持目前市场上的各类LED,非常适合驱动汽车应用中的高亮度LED。
图2中的示意图展示了一种驱动器电路的典型基准电压设计。
图2:典型应用示意图(采用面向汽车前部照明的ASL1010PTK)。
由于驱动器IC集成度很高,因此应用设计在只需极少的外部组件的同时,还能维持系统的灵活性。在图2所示的应用示意图中,通过少量组件就实现了温度反馈功能,可控制LED的温度和性能;故障检测功能,可在LED出现故障时提供反馈;短路保护功能,使LED和驱动器IC免受电池和地引脚短路影响;灵活的电流选择和PWM编程功能;可调LED内部PWM产生功能,允许同一LED灯同时用作日间行驶灯和停车灯。LED欠压和过压保护。
借助这款尺寸小、散热性能良好的器件(HVSON14),驱动器IC可为LED串提供最高1A的电流。由于采用了高精度的集成电流源,该驱动器IC可以有效消除任何LED纹波电流,无需添加额外的外部组件。
本文小结
近年来,LED在汽车领域的应用呈大幅增长之势,究其原因在于LED具有无与伦比的设计灵活性、更长的使用寿命和更低的功耗水平。LED本身的性能也得到了大幅提升,增加了其在汽车应用领域的可用性。
随着LED应用的不断增多,我们还需要一种更加高效、更加稳健、更具成本优势的电子器件和驱动器IC,以便使LED的优势在汽车应用中得到充分发挥。
基于一种通用型LED照明系统架构,我们探讨了电子控制装置需要的特性,其中包括LED散热管理、驱动不同LED配置的灵活性以及具有成本优势的系统设计等。
为了满足这些不同的要求,我们提出了一种完全集成且非常灵活的汽车LED驱动器IC解决方案。ASL1010PTK为电路的设计提供了极大的便利,将外部组件的数量减至最少,同时还能提供驱动汽车LED所需要的必要功能,并可在系统层次维持较大的灵活性。
上一篇:轮胎压力监控系统的设计
下一篇:为汽车应用而优化的CMOS收音机IC解决方案
推荐阅读最新更新时间:2024-05-02 22:28
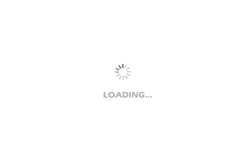
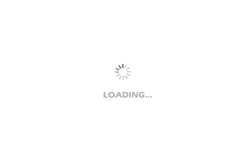
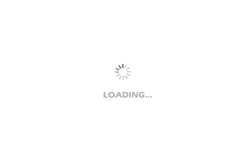
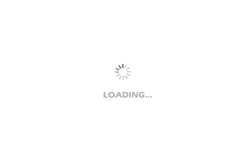
- 恩智浦LPC54100迅猛来袭,关注有礼
- 【已结束】PI 直播【适合工业市场辅助电源的碳化硅和氮化镓 IC】(9:30入场)
- 有奖直播|ADI在可穿戴产品中的生命体征监测解决方案
- 下载《ADI 任意波形发生器方案》抢楼有礼啦!
- 【直播已结束】一起深挖 TI 新发布的 Robotics SDK,看干货直播赢好礼!
- 有奖直播|安森美高能效产品在 EV-Charger 市场的应用
- 罗姆有奖直播|从0到1,带你了解电机及其驱动 开始报名啦~
- 有奖直播【如何在几分钟之内完成高效可靠的USB PD电源设计——PI Expert™分步教程】(9:30开始入场)
- 有奖直播|5G多场景终端应用对连接器的新要求及Molex的5G连接方案
- 下载《Altera SoC深度体验》,打分评论赢好礼